Unlocking Operational Excellence: Leveraging ISO 9001 Data-Driven Decision Making for Quality Improvements
- islam Arid
- May 1
- 5 min read
In today’s data-driven world, organizations can no longer rely solely on intuition for operational excellence. The effectiveness of data analytics and performance metrics is crucial when seeking improvements in quality. ISO 9001 certification provides a solid foundation for utilizing these tools. By combining data-driven decision-making with ISO 9001 principles, businesses can streamline quality control, initiate continuous improvement, and enhance customer satisfaction.
Understanding ISO 9001 and Its Relevance
ISO 9001 is a globally recognized standard that lays out the framework for establishing and enhancing a Quality Management System (QMS). This standard emphasizes the need for organizations to meet customer and regulatory requirements while consistently improving their processes. In fact, organizations that adopt ISO 9001 see a return on investment with a reported 10-15% increase in operational efficiencies and customer satisfaction rates.
The Importance of Data in ISO 9001 Implementation
Data plays a central role in successfully implementing ISO 9001. Organizations gather various performance metrics, such as production output, quality rates, and customer feedback. For instance, a manufacturing firm might track defect rates, which often reveal that small changes in processes can lead to a noticeable reduction in product flaws. These metrics help organizations identify areas needing improvement and implement corrective actions confidently.
Benefits of a Data-Driven Approach
Informed Decision Making: Relying on data leads to decisions grounded in solid evidence. For example, a company that uses customer feedback data may tweak its product line based on preferences, resulting in a sales increase of up to 20%.
Enhanced Quality Control: Ongoing data analysis allows for proactive quality measures. An electronics manufacturer, for example, might discover through data tracking that specific components lead to faults, allowing for early interventions.
Continuous Improvement: When organizations continually track performance metrics, they cultivate an environment of ongoing enhancement. Automotive companies that apply regular data assessment report faster cycle times and improved quality ratings.

Establishing a Quality Policy Based on Data Insights
A strong quality policy is essential for ISO 9001 compliance. Organizations should develop their policy by considering insights gathered from performance metrics. For instance, if data shows frequent customer complaints about delivery times, a company can commit to a policy that emphasizes improving logistics and communication with clients.
Setting Quality Objectives
Quality objectives should be Specific, Measurable, Achievable, Relevant, and Time-bound (SMART). For example, a retail organization might aim to reduce return rates by 5% within six months, using data insights from past customer returns to define its approach.
Implementing Performance Metrics for Effective Management Review
In the ISO 9001 context, performance metrics are vital indicators of an organization’s operational quality. They facilitate management reviews, allowing leadership to assess the QMS's effectiveness and make data-driven decisions.
Key Performance Metrics to Consider
Customer Satisfaction: Track customer feedback through surveys, aiming for at least 90% satisfaction to gauge service quality.
Nonconformities and Corrective Actions: Monitor the number of nonconformities each month. For instance, if a unit targets six nonconformities per quarter, a sudden spike may signal the need for urgent process review.
Process Performance: Metrics such as cycle times and defect rates can reveal trends over time. If defect rates exceed 2%, this may prompt a review of production processes.
Supplier Quality: Evaluating suppliers based on defect rates helps maintain quality across the supply chain. Organizations might require suppliers to have defect rates below 1% to ensure high standards.
Conducting Internal Audits for Continuous Improvement
Internal audits play a critical role in the ISO 9001 framework, allowing organizations to ensure adherence to quality standards. Through consistent data collection and analysis during audits, organizations can identify gaps and highlight areas for improvement, typically achieving a 15% uptick in compliance rates post-audit.
Leveraging ISO 9001 Tools for Enhanced Data Analysis
ISO 9001 offers several tools to improve data analysis, allowing organizations to optimize processes and boost quality assurance.
1. Statistical Process Control (SPC)
SPC methods bring structure to data monitoring. For example, control charts can help a manufacturer pinpoint when a process goes out of control, enabling swift corrections. In practice, companies using SPC often report a reduction in scrap rates by 30%.
2. Quality Management Software
Investing in quality management software streamlines data collection and reporting. Many systems incorporate analytics that simplify tracking key performance indicators and performance metrics, ultimately saving organizations 20% in time spent on quality reporting.
3. Six Sigma Methodology
The Six Sigma approach emphasizes eliminating defects with robust data analysis methods. Many organizations that have applied Six Sigma principles in conjunction with ISO 9001 have seen a spike in process efficiency by nearly 25%.
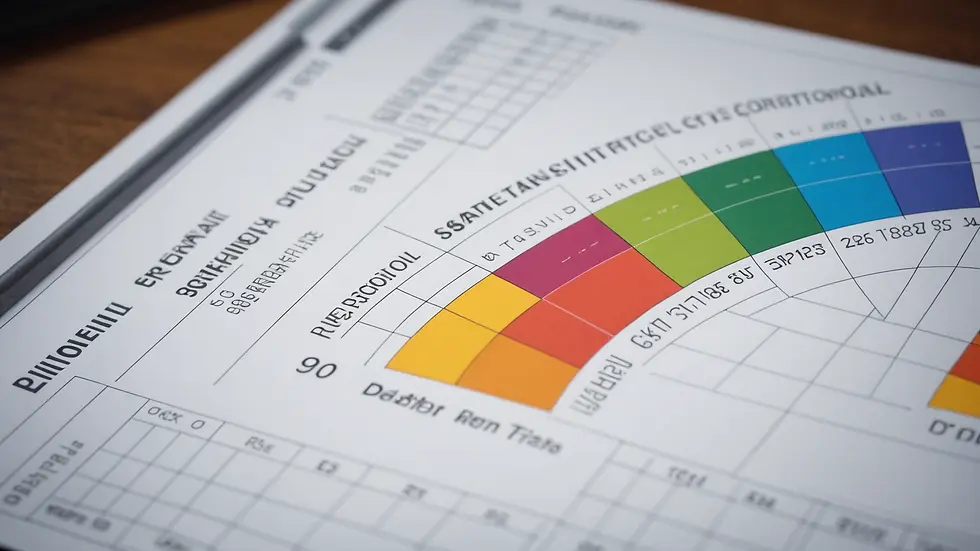
Risk Management and ISO 9001
Data analytics are vital for effective risk management within the ISO 9001 framework. Organizations need to assess risks related to their processes and implement controls to mitigate potential issues.
Identifying Risks through Data Analysis
By reviewing historical data, organizations can detect trends that signal risks. For instance, if defect trends correlate with specific production runs, preemptive actions can be taken to avert quality issues, potentially saving organizations thousands in costs resulting from rework and waste.
Building a Quality Culture through Training and Development
Integrating data-driven decision-making into training programs is crucial for nurturing a quality culture. Employees must understand the value of data in quality management and feel empowered to make contributions toward quality enhancement.
The Role of Leadership in Promoting a Quality Culture
Leadership significantly influences the creation of a quality culture. When leaders actively promote data-driven decision-making and encourage team collaboration, organizations can create an environment where quality is a priority for everyone.
Continuous Improvement and Performance Monitoring
Continuous improvement is central to ISO 9001. Organizations should consistently monitor performance to evaluate progress. By utilizing data analytics and tracking performance metrics, teams can refine processes and implement changes that drive quality enhancements.
Engaging Employees in Continuous Improvement Efforts
Involving employees in ongoing improvement initiatives strengthens commitment to quality and increases the chances of successful outcomes. Training programs focused on practical applications of data analytics help teams familiarize themselves with tools that support data-driven decision-making.
The Road Ahead: Future Trends in Quality Management
Future developments in quality management will be shaped by advances in technology and data analytics. Organizations that embrace these trends will enhance their ISO 9001 compliance while gaining competitive advantages.
Artificial Intelligence and Predictive Analytics
AI and predictive analytics are poised to revolutionize quality management. Organizations can use AI to efficiently analyze large datasets, recognize patterns, and anticipate outcomes. This leads to more proactive decision-making and greater operational efficiency.
The Integration of Internet of Things (IoT) in Quality Management
Integrating IoT devices into daily operations enables real-time data collection and monitoring. Organizations can use this instantaneous information to make adjustments that improve quality control, resulting in faster response times and reduced quality issues.
The Path to Operational Excellence
Incorporating ISO 9001 with data-driven decision-making is essential for organizations aiming for operational excellence. This approach allows companies to use data analytics and performance metrics effectively, leading to ongoing improvements and enhanced quality control. As quality management practices continue to evolve, staying agile and informed will pave the way for future success. With a solid dedication to quality and the right data insights, organizations can unlock new levels of operational excellence.
Комментарии