Strategies for Implementing Quality Controls in ISO 9001 Certified Organizations
- islam Arid
- May 1
- 4 min read
Quality control is vital for organizations seeking ISO 9001 certification. This standard provides a roadmap for quality management, helping organizations consistently meet customer expectations and regulatory guidelines. In this post, we will explore practical strategies for implementing effective quality controls in ISO 9001 certified organizations. These strategies will help boost efficiency and enhance customer satisfaction.
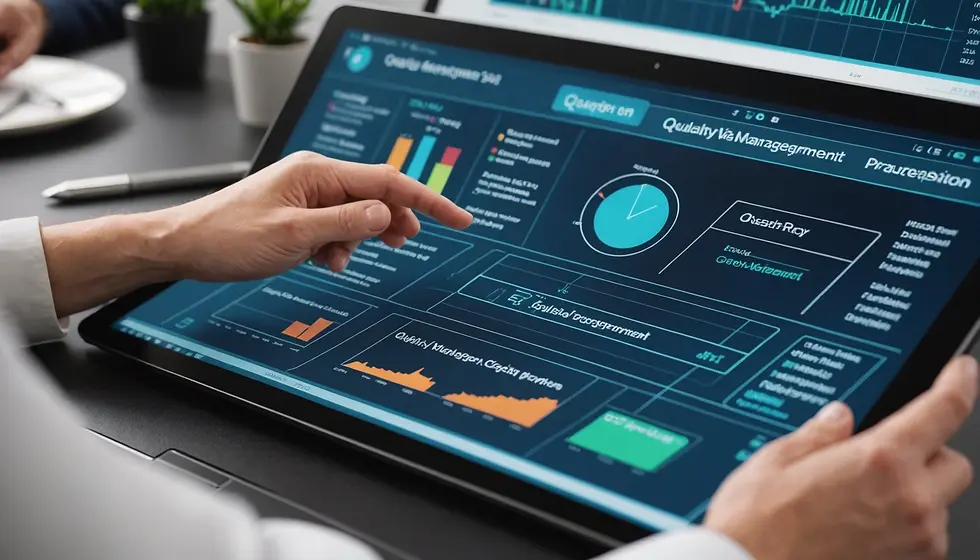
What is ISO 9001?
ISO 9001 is a globally recognized standard for quality management systems (QMS). This framework enables organizations to improve their overall performance while ensuring quality consistency in products and services.
Implementing ISO 9001 helps organizations effectively manage processes, mitigate risks, and seize opportunities for improvement. Research shows that companies with ISO 9001 certification can experience a 20% increase in customer satisfaction and a 15% reduction in operational costs over time, emphasizing the significant benefits of this standard.
Why Quality Control Matters in Product and Service Delivery
Quality control is essential in today's competitive marketplace. It sets the standards that products and services must meet to fulfill customer needs. Enhanced quality control can lead to increased customer satisfaction, resulting in repeat business and referrals.
For instance, a study by the American Society for Quality found that 80% of customers are likely to make repeat purchases from companies that demonstrate consistent product quality. Additionally, strong quality controls can help organizations identify issues early, saving costs and preventing disruptions in the supply chain.
Effective Strategies for Quality Control Implementation
1. Establish a Quality Policy
Creating a well-defined quality policy is foundational for quality control activities. This policy should express the organization's commitment to quality and outline its quality objectives.
A clear quality policy fosters a shared understanding of quality goals among employees. Consider reviewing and updating the policy annually to ensure its relevance.
2. Set Clear Quality Objectives
Establishing measurable quality objectives is critical for effective quality management. These objectives should align with your organization’s strategic goals and adhere to the SMART criteria: Specific, Measurable, Achievable, Relevant, and Time-bound.
For example, a manufacturing company may set a goal to reduce production defects by 10% within six months. By monitoring these objectives, organizations can track performance and adjust their processes as needed.
3. Implement Document Control Procedures
Document control is essential for ISO 9001 compliance. A robust document management system ensures that employees access the most up-to-date quality standards and procedures.
By controlling documents effectively, organizations can minimize errors arising from outdated information. For instance, utilizing a digital document management system can reduce document retrieval time by 30%.
4. Conduct Regular Internal Audits
Regular internal audits are crucial for assessing compliance with ISO 9001 standards and evaluating the effectiveness of quality controls. These audits help organizations identify areas for improvement and preemptively address potential issues.
By developing an annual internal audit schedule and training assessors, businesses can nurture a culture of continuous improvement.
5. Train and Develop Employees
Training plays a key role in quality control. Well-trained employees can better understand quality standards, spot nonconformities, and take corrective actions.
For example, investing in staff training can lead to a 25% increase in employee productivity, as they become more capable of executing processes efficiently. Regular training sessions ensure that employees are always up-to-date with industry standards.
6. Utilize Performance Metrics
Implementing performance metrics is essential for measuring quality control success. Establish key performance indicators (KPIs) that relate to your quality objectives.
For instance, tracking customer complaints can provide valuable insight into quality issues. Organizations that effectively monitor KPIs can achieve a 15% improvement in response times for customer inquiries, enhancing overall satisfaction.
7. Manage Supplier Quality
Supplier quality is a critical component of quality control. Regular assessments and performance monitoring help ensure that materials and services meet established quality standards.
Implementing supplier evaluations can reduce defects by 20% by ensuring that only high-quality materials are used in production.
8. Foster a Quality Culture
Creating a strong quality culture is crucial for quality control success. Encourage employee involvement and ownership of quality initiatives, fostering collaboration and commitment to improvement.
Recognizing and rewarding efforts to enhance quality can motivate employees to prioritize quality in their daily tasks, leading to more consistent outcomes.
9. Implement Corrective Actions for Nonconformities
Establishing procedures to address nonconformities is essential. A well-structured corrective action process resolves issues while preventing their recurrence.
This process should encompass identification, investigation, root cause analysis, implementation of solutions, and verification of effectiveness. Research indicates that effective corrective actions can reduce repeat problems by 60%.
10. Ensure Continuous Improvement
ISO 9001 encourages continuous improvement through regular evaluation of processes and the implementation of enhancements. Establish a culture that embraces feedback and adapts to changing customer needs.
Regularly reviewing processes enables businesses to uncover opportunities for improvement, helping them stay competitive in a dynamic market.
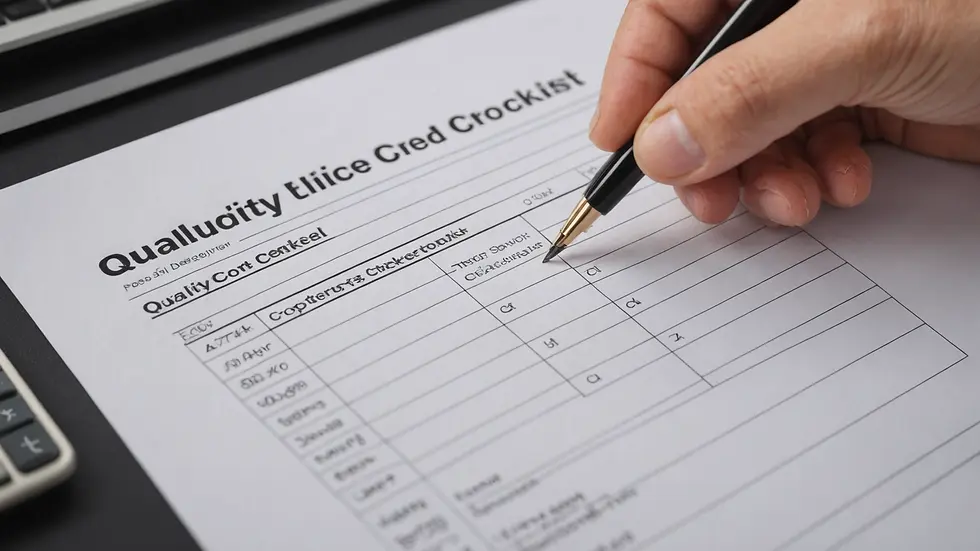
Why Quality Control is Key to Success
Implementing quality controls in ISO 9001 certified organizations is not just about compliance. It is a strategic approach to enhancing customer satisfaction, minimizing costs, and driving organizational excellence.
By establishing a solid quality policy, setting clear objectives, and committing to continuous improvement, organizations can successfully navigate the challenges of quality management. Proactive practices such as employee training, efficient document management, regular audits, and strong supplier quality management create a powerful framework for success.
Organizations that prioritize quality not only meet but exceed customer expectations, setting the stage for sustainable growth. Regularly reviewing quality practices in line with ISO 9001 standards will help ensure ongoing success in achieving quality objectives while building a strong reputation in the market.
Comentarios