Implementing ISO 9001: Ensuring Quality Throughout the Product Lifecycle
- islam Arid
- May 1
- 5 min read
Quality management is vital in today’s business world. Companies must focus on quality throughout all stages of a product's life, from design and development to after-sales support. If done correctly, this focus can lead to greater efficiency and increased customer satisfaction. ISO 9001 provides an effective framework for achieving these goals and ensuring that quality remains a top priority.
In this blog post, we will discuss why ISO 9001 matters in product lifecycle management, the steps needed for implementation, and how adhering to these standards fosters a culture of continuous improvement. Let’s explore the world of ISO 9001 and its significance in quality management.
Understanding ISO 9001
ISO 9001 is a global standard that defines the requirements for a quality management system (QMS). It provides organizations with guidelines to enhance operations while prioritizing customer satisfaction and continuous improvement.
One important aspect of ISO 9001 entails setting specific quality requirements. For example, companies must define a quality policy, document processes, and perform regular internal audits to ensure compliance. According to ISO's research, organizations that adopt this standard can see up to a 30% improvement in operational efficiency, a clear benefit that highlights its importance.
The Importance of Product Lifecycle Management
Product lifecycle management (PLM) is the process that oversees a product's development from inception to disposal. Every stage must be managed carefully to ensure that products meet customer expectations and comply with industry regulations.
Integrating ISO 9001 within PLM lays the groundwork for a quality management system that spans every phase of a product's lifecycle. This holistic approach emphasizes quality control, risk management, and compliance, ultimately leading to higher customer satisfaction. For instance, businesses that effectively manage their PLM can reduce product development costs by as much as 40%, showcasing the financial benefits of such practices.
Implementing ISO 9001 in Product Lifecycle Management
1. Define Quality Objectives
To implement ISO 9001, begin by defining clear quality objectives aligned with the organization's strategic goals. Aim to make these objectives SMART: specific, measurable, achievable, relevant, and time-bound. For instance, a tech company might set a goal to reduce product defects by 20% within the next year. This targeted approach guides quality efforts throughout the product lifecycle.
2. Establish a Quality Policy
A well-defined quality policy communicates the organization's commitment to maintaining quality. It should reflect the goals and principles of quality management. Make sure this policy is communicated effectively to all employees, as a shared understanding fosters a quality-focused culture.
3. Document Control
Documentation is essential in ISO 9001 implementation. Organizations must create and maintain documented processes, procedures, and records to back quality management efforts. Proper document control helps ensure that the crucial information is available to the right people at the right time, streamlining decision-making and process enhancement. For instance, a manufacturing company could use standard operating procedures to ensure consistency in production operations.
4. Risk Management
Managing risks effectively is critical. Regular risk assessments help identify potential threats to product quality. By developing strategies to address these risks, organizations can bolster their quality management processes. For example, a food manufacturer might assess the risk of contamination and proactively implement safety measures to ensure compliance with health regulations.
5. Internal Audits
Conducting regular internal audits is vital for evaluating ISO 9001 compliance and spotting areas that need improvement. A systematic audit process helps organizations identify nonconformities, enabling corrective actions to enhance product quality. Companies that perform internal audits can see a reduction in errors by as much as 25%, illustrating the power of this practice.
6. Management Review
Management review is crucial in ensuring the quality management system's effectiveness. Senior leaders should analyze performance metrics, audit results, and customer feedback to assess the organization's quality objectives. This ongoing review process ensures that the QMS continues to align with the organization's strategies and goals.
7. Training and Development
Investing in training is essential to nurture a culture of quality. Organizations should identify training needs and create opportunities for skill development in quality management. A well-trained workforce can lead to a 40% increase in productivity, allowing for a more robust operation.
8. Continuous Improvement
ISO 9001 drives organizations to adopt a mindset of continuous improvement. Regularly evaluate performance metrics, gather customer feedback, and identify improvement areas. This proactive stance on improvement allows businesses to innovate and adapt to changes in the market swiftly.
9. Customer Satisfaction
Enhancing customer satisfaction is a core principle of ISO 9001. By maintaining quality throughout the product lifecycle, organizations can not only meet but exceed customer expectations. A focus on quality often leads to improved customer retention rates, which can be as high as 45% for companies that actively engage in quality management.
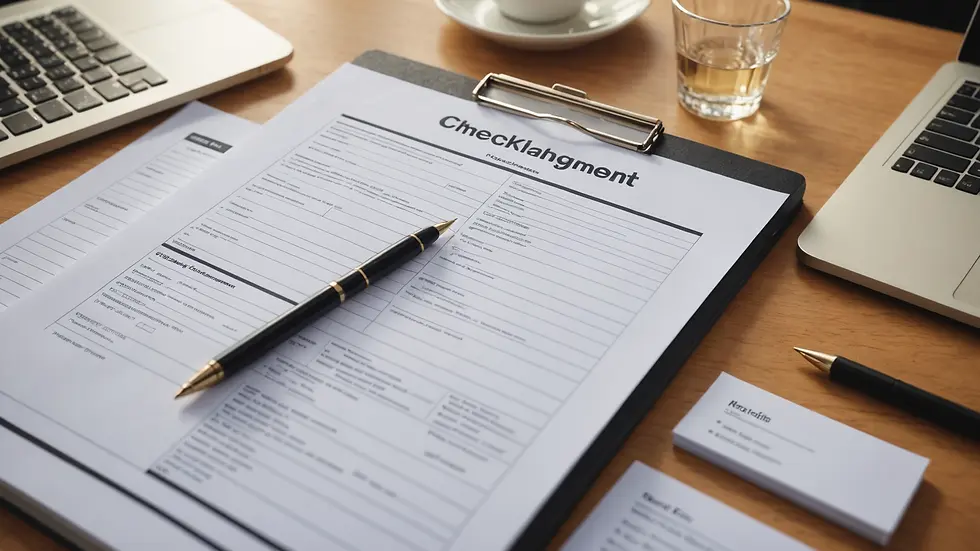
Challenges in Implementing ISO 9001
While implementing ISO 9001 offers significant benefits, challenges may arise, such as employee resistance to change and the need for sufficient resources. Overcoming these challenges is crucial. Companies can alleviate resistance by fostering a culture of quality, providing training, and ensuring clear communication from leadership.
For instance, a technology firm faced pushback on implementing new quality processes; however, by involving employees in the transition and offering relevant training, they achieved a smoother adoption process with increased buy-in from the team.
Real-World Examples of ISO 9001 Implementation
Examining real-world examples can shed light on the effectiveness of ISO 9001 in product lifecycle management.
Aerospace Industry: Companies in aerospace reporting ISO 9001 implementation often experience considerable gains in product reliability and safety. By adhering to stringent quality standards, they minimize regulatory risks and recall occurrences, saving substantial costs.
Automotive Industry: In the automotive sector, manufacturers that implement ISO 9001 see improvements in supply chain management. For instance, one automotive company reported a 15% increase in supplier quality after adopting ISO standards, leading to better customer satisfaction.
Healthcare Sector: In healthcare, the application of ISO 9001 has been linked to enhanced patient care. Organizations focusing on quality management not only comply with stringent industry regulations but also report increased patient outcomes, highlighting the standard’s positive impact on healthcare quality.
Final Thoughts
Adopting ISO 9001 within product lifecycle management provides a powerful pathway to ensure quality at every stage of a product's journey. By complying with established guidelines and committing to continuous improvement, organizations can enhance product quality, increase customer satisfaction, and optimize operational efficiency.
Companies that embrace ISO 9001 are better equipped to tackle challenges and adapt to a rapidly changing market. A strong commitment to quality management instills a culture of excellence that paves the way for long-term success. In essence, implementing ISO 9001 is more than achieving compliance; it is about fostering a quality-first mindset that benefits both the organization and its customers.
Comentarios