Top Mistakes to Avoid During ISO 9001 Certification
- islam Arid
- Nov 30, 2024
- 5 min read
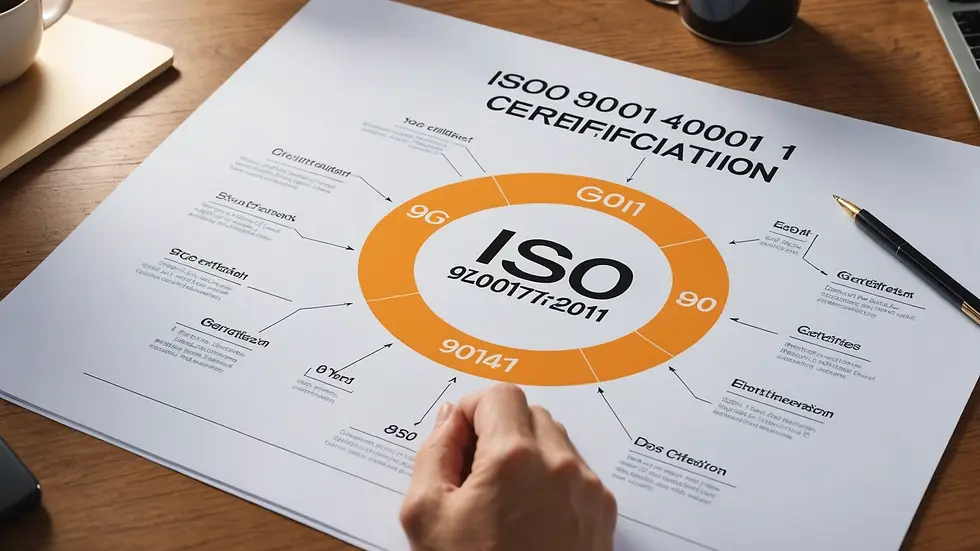
Achieving ISO 9001 certification is a transformative step for businesses seeking to improve their quality management systems. This certification not only demonstrates a commitment to quality but also enhances customer satisfaction. However, many organizations encounter challenges throughout the certification journey. Understanding common mistakes can help you navigate this process more smoothly. Below are pitfalls to avoid along with practical tips to ensure successful certification.
Inadequate Planning
One of the frequent challenges organizations face is inadequate planning. A lack of a detailed strategy can result in chaos, missed deadlines, and spiraling costs. It is vital to develop a clear project plan covering every aspect of the certification process.
When planning, incorporate the following considerations:
Define Objectives: Start by determining your specific goals related to ISO 9001 certification. For example, aim for a 15% improvement in customer satisfaction scores post-certification.
Establish a Timeline: Create a realistic timeline with specific milestones. For instance, allocate two months for training, three months for documentation preparation, and one month for internal audits.
Allocate Resources: Ensure you have the right team members and tools in place. For example, one project manager, three quality assurance specialists, and relevant software tools will be essential.
Investing time in planning means avoiding last-minute rushes and making the certification process more efficient.
Poor Documentation Practices
ISO 9001 emphasizes strong documentation practices. Organizations often overlook the significance of comprehensive documentation, which can lead to misunderstandings and inconsistencies.
To enhance documentation:
Create a Document Control System: Implement a system that covers version control, accessibility, and retention. For instance, establishing a shared drive for all QMS documents will streamline access and updates.
Standardize Processes: Ensure that every process is documented consistently. For instance, create templates for operational procedures that all departments must follow to maintain clarity.
Regular Reviews: Schedule reviews every quarter to keep documents relevant. According to a study, organizations that maintain updated documentation experience 20% fewer compliance issues.
Clear documentation will clarify the certification process and provide a reliable reference for audits.
Lack of Employee Involvement
Employee engagement is essential in the ISO 9001 certification journey. When only the leadership drives the initiative, it often leads to apathy and resistance.
To boost employee involvement:
Communicate Clearly: Be transparent about the certification's importance and benefits. Share statistics, such as companies that achieve ISO 9001 certification experience a 20% increase in operational efficiency.
Provide Training: Conduct training sessions about the quality management system and employee responsibilities. Consider organizing a workshop where each team member can contribute to process improvement discussions.
Encourage Feedback: Create anonymous feedback channels to understand employee concerns about the QMS. Employees who feel their input is valued are more likely to engage positively with the initiative.
Fostering a culture of involvement can boost morale and ensure smoother certification.
Skipping Internal Audits
Internal audits play a critical role in ISO 9001 certification. They help identify non-conformities before the official certification audit. Unfortunately, some organizations skip this essential step, thinking it is not vital.
To conduct effective internal audits:
Schedule Regular Audits: Include regular internal audits in your QMS calendar, ideally quarterly. Research shows that organizations that conduct regular audits are 30% more likely to pass certification on the first attempt.
Train Auditors: Ensure internal auditors are well-trained in ISO 9001. Competent auditors can provide insightful evaluations.
Act on Findings: Treat audits seriously by developing action plans to address identified issues. Organizations that do this typically improve their processes by 10% annually.
Ignoring internal audits can lead to significant setbacks during the external audit.
Inadequate Management Reviews
Management reviews are crucial for assessing the effectiveness of the QMS. Yet, many organizations do not conduct these reviews adequately.
To improve management reviews:
Establish a Review Schedule: Set a regular schedule, typically every six months, to ensure accountability.
Focus on Key Metrics: Utilize performance data and key performance indicators to evaluate QMS effectiveness. For example, track data on customer complaints and process efficiency metrics over time.
Document Outcomes: Keep records of discussions and decisions from management reviews. These records can serve as evidence during the certification audit.
By prioritizing management reviews, organizations can continuously enhance their QMS and maintain a strong certification preparation.
Ignoring Customer Feedback
ISO 9001 emphasizes the importance of customer satisfaction. However, some organizations fail to actively seek and act on customer feedback. Ignoring this aspect can lead to missed certification opportunities.
To ensure customer feedback is valued:
Implement Feedback Channels: Create multiple ways for customers to share feedback, such as online surveys or review platforms.
Analyze Feedback: Regularly review customer feedback to identify trends and areas for improvement. For example, if 40% of customers cite a similar complaint, it likely requires urgent attention.
Act on Insights: Demonstrate commitment by implementing changes based on customer feedback. Show certifying bodies that you actively seek to meet customer needs.
Integrating customer feedback into the QMS is vital for achieving ISO 9001 certification and enhancing overall satisfaction.
Underestimating Time and Resources
A frequent misstep is underestimating the time and resources needed for ISO 9001 certification. Doing so can lead to rushed implementations and compromise process quality.
To overcome this challenge:
Conduct a Resource Assessment: Evaluate existing resources and identify additional needs, such as hiring a quality consultant or purchasing software tools.
Factor in Contingencies: Build buffer time into your project timeline to account for unexpected challenges.
Monitor Progress: Regularly assess progress and adjust resource allocations as necessary. For instance, if documentation is lagging, consider extending deadlines or reallocating team members.
Taking a realistic approach to resource management can streamline the certification process.
Failing to Prepare for Leadership Engagement
Leadership involvement is critical for driving ISO 9001 certification. However, organizations often do not equip their leaders adequately, which can lead to a lack of direction.
To enhance leadership engagement:
Set Clear Expectations: Articulate what is expected from leadership during the certification process.
Provide Necessary Training: Offer training to leaders regarding ISO 9001 standards and their organizational implications.
Encourage Visibility: Leaders should actively participate in the certification efforts, signaling their commitment to quality.
Engaged leadership is essential for fostering a culture focused on quality and successful certification.
Neglecting Continuous Improvement
ISO 9001 requires a commitment to continuous improvement. Treating certification as a one-time event can jeopardize future compliance.
To cultivate a culture of continuous improvement:
Implement Improvement Processes: Create formal processes for continuous improvement, like utilizing the Plan-Do-Check-Act (PDCA) cycles.
Celebrate Successes: Recognize and reward improvements within the organization. Celebrating these moments can motivate personnel and maintain enthusiasm for ongoing quality initiatives.
Monitor and Report: Provide regular updates on improvement efforts to keep everyone informed. A culture of recognition can lead to a 25% increase in employee engagement.
By embedding continuous improvement into the company culture, organizations can achieve and maintain ISO 9001 certification.
Final Thoughts
Achieving ISO 9001 certification can greatly enhance a company's reputation and operational efficiency. However, this journey presents its fair share of challenges. By steering clear of mistakes like inadequate planning, poor documentation, and lack of employee involvement, organizations can pave a more efficient path to certification.
Taking proactive steps to engage your team, maintain robust documentation, and commit to continuous improvement will not only simplify the certification process but also contribute to long-term organizational success.
In essence, ISO 9001 certification represents more than just a status symbol; it embodies a commitment to quality and customer satisfaction that organizations should embrace wholeheartedly.
Comments