Implementing Risk-Based Thinking: Enhancing Quality Management in Alignment with ISO 9001
- islam Arid
- Nov 30, 2024
- 5 min read
In an ever-changing business landscape, companies face increasing pressure to enhance their performance while maintaining high-quality standards. One powerful strategy that has gained traction is "risk-based thinking." This approach, central to the recent updates to ISO 9001, allows businesses to proactively manage risks, leading to improved product quality and overall performance. In this article, we will explore how businesses can effectively implement risk management principles to anticipate and address potential challenges before they impact operations.
Understanding ISO 9001 and Risk-Based Thinking
ISO 9001 is the global standard that sets the requirements for a quality management system (QMS). It provides guidelines to help organizations meet the needs of customers and regulatory bodies effectively. With the 2015 revision, ISO 9001 has shifted focus to risk-based thinking, making it a fundamental part of quality management.
Risk-based thinking pushes organizations to identify risks proactively, addressing them before they can disrupt product or service quality. This approach marks a significant change from traditional quality management practices, which often only addressed issues once they became apparent.
By prioritizing risk-based thinking, ISO 9001 fosters an environment where risk evaluation is integrated into everyday operations, making it a vital aspect of an organization’s culture.
The Shift from Preventive Action to Risk Management
In the past, preventive action was the primary strategy for mitigating risks. While still important, this approach tends to react only to known issues. Risk-based thinking extends this by fostering a broader understanding of uncertainties that could affect all areas of an organization.
This shift means that companies must adopt more comprehensive methodologies for risk management. This involves not only dealing with known non-conformities but also addressing potential uncertainties across various aspects of their operations.
Benefits of Implementing Risk-Based Thinking
Integrating risk-based thinking into your QMS can lead to significant advantages, including:
Enhanced Decision-Making: Organizations that regularly assess risks can make informed decisions that align with their quality goals. For instance, companies using risk assessments in supply chain management report a 25% reduction in disruptions.
Proactive Identification of Opportunities: Risk-based thinking allows businesses not only to address problems but also to uncover opportunities for process improvements. For example, by evaluating customer feedback risks, companies can identify new product features that lead to a 15% increase in sales.
Stronger Customer Satisfaction: Consistently meeting quality requirements boosts customer trust. In fact, organizations that adopt risk management principles see an increase in customer satisfaction scores by up to 30%.
Increased Operational Efficiency: Understanding where risks lie helps organizations streamline operations. Companies that implement risk assessment strategies often find they can reduce operational costs by 20% through better resource allocation.
Sustainable Continuous Improvement: Regularly evaluating risks fosters a culture of ongoing improvement, enabling companies to adapt to market changes more effectively. Organizations that emphasize continuous improvement report a 10% annual increase in productivity levels.
Key Components of Risk Assessment
To successfully implement risk-based thinking, organizations should focus on these key components during risk assessments:
Identifying Risks
The first step is to pinpoint possible risks that could impact quality. This might include:
Internal Factors: Inefficiencies in processes could lead to product delays.
External Factors: Regulatory changes or fluctuating market conditions might introduce uncertainty.
Organizations can use various techniques to identify these risks:
Brainstorming Sessions: Gathering cross-departmental teams can reveal hidden risks.
Process Mapping: Visual aids help highlight vulnerability points in workflows.
Historical Data Analysis: Analyzing past incidents reveals trends that may indicate future risks.
Analyzing Risks
Once risks are identified, the next step involves assessing their potential impacts and likelihood. Useful tools include:
Risk Matrix: This tool categorizes risks by likelihood and impact, setting the stage for prioritized action.
Root Cause Analysis: Understanding underlying causes helps create targeted strategies for risk mitigation.
Evaluating Risks
In evaluating risks, organizations assess which ones warrant action, considering their risk tolerance and management capacity. A cost-benefit analysis helps evaluate the resources needed versus the risk's potential impact.
Treating Risks
This step involves devising and implementing strategies to manage the identified risks, which can include:
Risk Avoidance: Reworking processes to eliminate specific risks.
Risk Reduction: Enacting measures to lower the likelihood or impact of risks.
Risk Transfer: Outsourcing certain functions to mitigate risks.
Risk Acceptance: Accepting the risk when mitigation costs outstrip potential impact.
Monitoring and Review
Implementing risk-based thinking requires ongoing monitoring of risks and the effectiveness of strategies. This can be achieved through:
Regular Audits: Scheduled reviews ensure adherence to risk management protocols.
Feedback Loops: Establishing channels for feedback assists in swift adaptation to new risks.
Integrating Risk-Based Thinking into the Quality Management System
To effectively integrate risk-based thinking into the QMS, organizations should follow these vital steps:
Top Management Commitment
For risk-based thinking to flourish, top management must demonstrate commitment. This entails promoting the significance of risk management in decision-making and allocating necessary resources.
Training and Development
Education on risk-based thinking should be a top priority. Offering training sessions empowers all employees to identify and manage risks relevant to their roles.
Communication of Risk Information
Maintaining open communication about risks is crucial. Sharing information across departments fosters collaboration for timely risk assessment and responses.
Documentation
Thorough documentation of risk management processes is essential. This not only ensures compliance with ISO 9001 but serves as a valuable reference for audits and future assessments.
Integration with Existing Processes
Risk-based thinking should seamlessly integrate with existing processes. Including risk assessments in projects and product developments ensures a holistic quality management approach.
Common Challenges and Solutions in Implementation
While the advantages of adopting risk-based thinking are clear, organizations may face several challenges. Here are common obstacles and their solutions:
Resistance to Change
Challenge: Employees may resist new practices, feeling overwhelmed by changes.
Solution: Clearly communicate the benefits of risk-based thinking and involve team members in its implementation to foster buy-in and reduce pushback.
Misinterpretation of Risks
Challenge: Confusion about what constitutes a risk and how to evaluate it can arise.
Solution: Provide clear definitions and real-world examples of risks coupled with training to align understanding across the organization.
Lack of Resources
Challenge: Organizations may struggle to allocate resources effectively.
Solution: Prioritize risk management by integrating it into business strategies, highlighting its potential for driving long-term financial benefits.
Maintaining Agile Processes
Challenge: Achieving agility while managing risks systematically might be difficult.
Solution: Utilize software tools for risk management to streamline assessments, keeping risk data current and facilitating faster decision-making.
Final Thoughts
Embracing risk-based thinking within quality management systems aligns perfectly with ISO 9001 principles. Organizations that systematically identify, analyze, and manage risks can continuously enhance quality performance. This leads to higher customer satisfaction and organizational success.
As businesses navigate increasingly complex and uncertain environments, adopting risk-based thinking will prove to be invaluable. Those who embrace this approach are more likely to exceed quality expectations, positioning themselves as leaders within their industries.
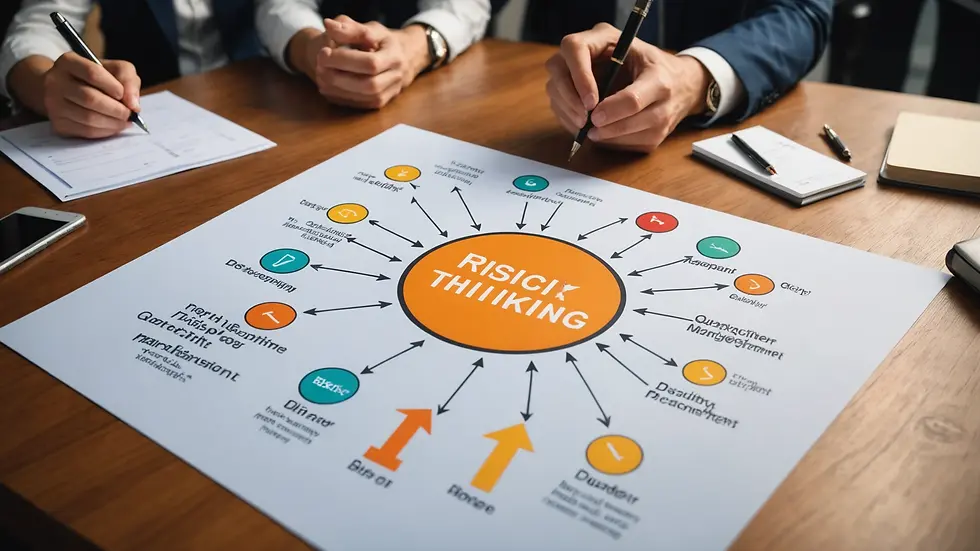
Commenti