How ISO 9001 Can Help You Achieve Consistent Product Quality
- islam Arid
- Nov 30, 2024
- 4 min read
One effective way to accomplish this is through ISO 9001. This globally recognized standard emphasizes process standardization, ensuring that products meet quality expectations consistently. This article dives into how ISO 9001 helps businesses streamline their quality management and highlights practical examples and actionable strategies.
Understanding ISO 9001
ISO 9001 is a recognized international standard for quality management systems (QMS). It revolves around key principles like:
Customer Focus: Ensuring that customer needs are prioritized.
Leadership: Top management plays a crucial role in driving quality initiatives.
Process Approach: Streamlining processes leads to better outcomes.
Continuous Improvement: Regularly improving processes boosts efficiency.
By adopting ISO 9001, organizations can enhance their ability to consistently deliver products that meet both customer needs and legal requirements. For example, a small manufacturing firm implementing ISO 9001 reported a 30% increase in customer satisfaction within the first year.
The Role of Process Standardization in Quality
Process standardization is fundamental to achieving quality through ISO 9001. By clearly defining and documenting all processes, organizations can significantly reduce errors that lead to defects or rework. For instance, a food production company that standardized its recipe documentation saw a 50% reduction in product inconsistencies.
Here are key benefits of process standardization:
Defining Roles and Responsibilities: Everyone knows their tasks, minimizing confusion and boosting efficiency.
Establishing Best Practices: Documenting successful approaches ensures they are replicated throughout the organization.
Facilitating Training: New hires can be onboarded quickly, allowing them to contribute to quality efforts immediately.
Monitoring and Measurement for Quality Assurance
Monitoring and measurement are crucial for any ISO 9001 implementation. Organizations need to define key performance indicators (KPIs) that track performance over time. For instance, a service provider noticed a 20% increase in service delivery efficiency by regularly measuring turnaround times.
Key benefits of monitoring and measuring include:
Identifying Variations: Early detection of deviations prevents bigger issues later.
Informed Decision Making: Companies can allocate their resources more effectively and focus improvement efforts on areas that need it the most.
Benchmarking Performance: Assessing performance against past data helps organizations to strive for continuous improvement.
The Importance of Continuous Feedback Loops
For consistent product quality, feedback loops need to be a part of the process. Gathering feedback from both internal and external sources helps companies refine their processes continuously.
Internal Feedback Loops
Encouraging regular team discussions allows organizations to address quality issues proactively. For example, software development teams that hold weekly retrospectives often find and correct software bugs faster, reducing the bug count by up to 40%.
Customer Feedback
Understanding customer experiences is equally important. Organizations can use surveys and direct communications to gather feedback. For instance, a retail business that actively seeks customer reviews increased its repeat purchase rate by 25% after implementing changes based on feedback.
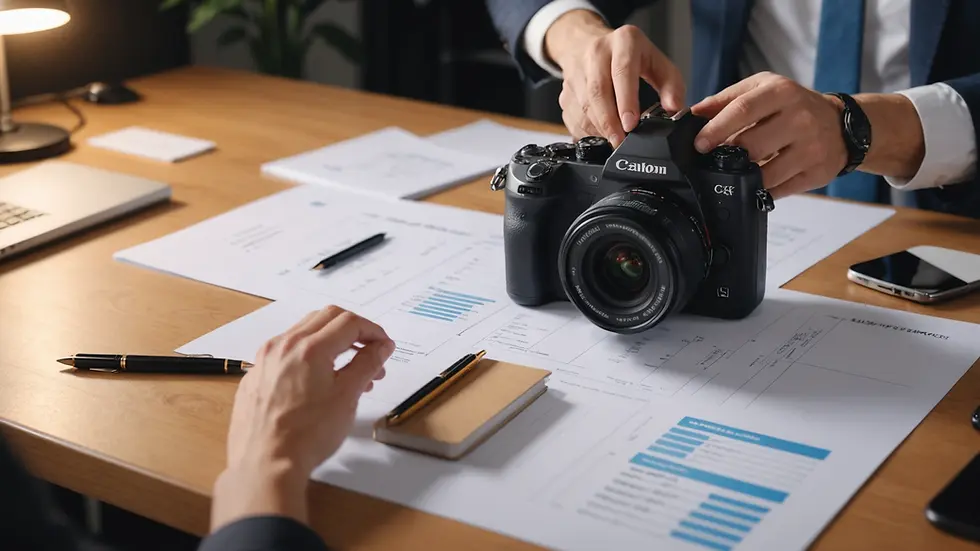
Managing and Tracking Variations
To maintain consistent quality, organizations must effectively manage variations in their processes. Variations can occur due to shifting workforce dynamics, equipment maintenance, and material consistency. ISO 9001 helps in identifying and addressing these challenges.
Change Control
By implementing a change control process, companies can ensure modifications are assessed properly before being introduced. For instance, manufacturers that follow structured change control processes report a 15% decrease in quality-related issues.
Root Cause Analysis
When defects occur, conducting root cause analyses is vital. By identifying the "why" behind quality failures, organizations can implement corrective measures to prevent recurrence. For example, a pharmaceutical company using this method reduced its product recall incidents by 30%.
Continuous Improvement Initiatives
Implementing methodologies like Plan-Do-Check-Act (PDCA) ensures organizations remain proactive. These frameworks empower teams to consistently evaluate and enhance their processes.
Building a Quality-Centric Culture
Creating a culture centered around quality is fundamental for successful ISO 9001 implementation. When everyone in the organization understands their role in quality management, the commitment to excellence increases.
Training and Development
Investing in training is essential. Programs that equip employees with quality management knowledge improve awareness and accountability. Firms that offer regular quality training report a 20% decrease in defects.
Leadership Commitment
Top management must actively support quality initiatives. When leaders prioritize quality, employees feel motivated to follow suit. This commitment can drive organizational success and enhance overall performance.
Recognition and Incentives
Recognizing employees' contributions to quality can motivate and inspire. For instance, businesses that reward quality improvement suggestions see increased employee involvement in quality efforts.
Evaluating Supplier Quality
The quality of products often depends on the quality of sourced materials. ISO 9001 guides organizations on assessing and managing supplier quality effectively.
Supplier Selection
A thorough supplier selection process ensures partnerships with those who share the same commitment to quality. Companies that evaluate supplier quality have fewer disruptions, evidenced by a 40% reduction in late shipments.
Performance Reviews
Conducting regular performance reviews helps in assessing suppliers based on criteria such as defect rates and delivery times. This approach allows organizations to maintain high standards across their supply chains.
Embracing the ISO 9001 Journey
ISO 9001 provides a robust framework for businesses striving for consistent product quality. By standardizing processes, monitoring performance, and fostering an environment of continuous improvement, organizations can significantly reduce defects and enhance customer satisfaction.
To make the most of ISO 9001, companies should create a culture that values quality. Engaging in thorough supplier evaluations and staying committed to improvement ensures products consistently meet or exceed customer expectations.
Embracing ISO 9001 is not only about meeting a standard; it is about wholeheartedly committing to quality that benefits both customers and stakeholders. The quest for consistent product quality is an ongoing journey, and ISO 9001 is a trustworthy guide throughout this process.
Comments