Optimizing Resource Utilization for ISO 9001: Best Practices for Effective Resource Management
- islam Arid
- Apr 7
- 5 min read
Effective resource management is vital for organizations aiming to achieve ISO 9001 certification. This international standard focuses on quality management and continuous improvement. It promotes a culture where resources are allocated efficiently to meet quality objectives. In this blog post, we’ll explore practical strategies to ensure resource availability and enhance allocation effectiveness, ultimately helping you meet your organizational quality standards.
Understanding ISO 9001 Resource Management
ISO 9001 provides a framework for establishing a Quality Management System (QMS). It guides organizations in enhancing operations, boosting customer satisfaction, and improving overall efficiency. Resource management within ISO 9001 involves ensuring that all necessary resources—whether they are human, technological, informational, or physical—are available and effectively managed.
Effective resource management can help organizations achieve ISO 9001 certification. For instance, organizations that systematically manage their resources can see customer satisfaction scores increase by up to 20%, as they provide higher quality products and services.
The Importance of Resource Allocation in ISO 9001
Resource allocation is crucial in ISO 9001 for several key reasons:
Quality Assurance: Properly managing resources is essential for maintaining high-quality standards.
Customer Satisfaction: Adequate resources lead to superior products, increasing customer satisfaction rates.
Cost-Effectiveness: Efficient resource allocation reduces waste and lowers operational costs.
Regulatory Compliance: Henceforth maintaining strict compliance with ISO 9001 requires strategic resource utilization.
Recognizing the importance of resource allocation empowers organizations to enhance their processes systematically. Research indicates that organizations with robust resource management see process efficiency improvements of around 25%.
Best Practices for Effective Resource Management
1. Conduct a Resource Needs Assessment
Conduct a thorough assessment of your resources before allocation. This includes:
Current resources: Identify what human, physical, and technological resources are presently available.
Required resources: Determine the resources needed to achieve your quality objectives.
Gaps: Analyze discrepancies between what is available and what is needed for ISO 9001 compliance.
A resource needs assessment sets the stage for effective planning, ensuring that all necessary resources are identified and prioritized. For example, after a resource assessment, a company might discover they need 15% more staff in their quality assurance team to meet their targets.
2. Establish Clear Quality Objectives
Align quality objectives with your overall strategy and the ISO 9001 guidelines. Setting clear, specific, and measurable objectives allows organizations to allocate resources more effectively. Consider involving all relevant stakeholders to guarantee the objectives reflect both organizational needs and customer expectations. This collaborative approach fosters unity and dedication towards achieving quality goals.
3. Develop a Resource Management Plan
Create a structured resource management plan that details how resources will be allocated to meet quality objectives. This plan should highlight:
Timelines: Outline when each resource will be needed.
Responsibilities: Assign roles for resource management tasks.
Monitoring mechanisms: Set up ways to track resource utilization.
A solid resource management plan can streamline processes and foster accountability. For example, organizations with clearly defined resource roles report a 30% improvement in project delivery times.
4. Implement Lean Management Principles
Lean management aims to minimize waste and enhance value. By applying these principles, organizations can identify non-value-adding activities and streamline operations. Some practical lean strategies include:
Value Stream Mapping: This tool helps identify which activities add value and which do not, guiding resource allocation decisions.
Continuous Improvement: Fostering a culture focused on ongoing improvement encourages employees to identify ways to enhance resource management.
By integrating lean principles, organizations can effectively allocate resources and align efforts with quality objectives, often achieving a 50% reduction in resource-related delays.
5. Conduct Regular Training and Development
Investing in employee training ensures staff possess the necessary skills and knowledge to utilize resources effectively. This training should emphasize:
Quality management principles: Familiarize employees with ISO 9001 standards.
Compliance: Teach compliance requirements and their significance.
Engaging employees in training programs enhances morale and fosters a dedicated culture of quality, pushing towards better customer satisfaction.
6. Implement Document Control Procedures
Establish effective document control practices for resource management under ISO 9001. Key documents should consist of:
Resource allocation plans.
Training and compliance records.
Quality objectives documentation.
Thorough documentation ensures clarity in roles and processes, aligning operations with ISO 9001 standards. Organizations using strong document control practices can lower document errors by 40%.
Monitoring and Reviewing Resource Utilization
1. Establish Performance Metrics
Metrics enable organizations to assess resource utilization. Important Key Performance Indicators (KPIs) might include:
Resource availability rates: Measure how often resources meet project demands.
Efficiency rates: Track how well resources are utilized.
Customer satisfaction ratings: Collect feedback to gauge the quality of outputs.
By consistently reviewing these metrics, organizations can make data-informed decisions to enhance their resource management.
2. Conduct Internal Audits
Regular internal audits are essential for ISO 9001 compliance and resource management. They help organizations:
Pinpoint areas needing improvement in resource allocation.
Verify alignment with quality objectives.
Audits cultivate a culture of accountability, enabling swift rectification of any identified issues.
3. Perform Management Reviews
Management reviews evaluate the effectiveness of the resource management plan against quality objectives. These reviews should involve:
Assessment of resource efficacy.
Identification of improvement opportunities.
Structured management reviews encourage higher-level engagement with quality policies, leading to data-driven resource management decisions.
Addressing Nonconformities in Resource Management
Nonconformities can arise when resource management practices fall short of ISO 9001 standards. Organizations should establish a process to tackle these issues, which includes:
Root Cause Analysis: Identifying the fundamental causes of nonconformities in resource management.
Corrective Actions: Implementing measures to resolve identified issues.
Preventive Actions: Proactively addressing nonconformities to prevent their recurrence.
By addressing nonconformities systematically, organizations can nurture a culture committed to continuous improvement in resource management.
Enhancing Supplier Quality
When examining resource management, the quality of external suppliers is often overlooked. Supplier quality has direct effects on overall product and service quality. Best practices for improving supplier quality include:
Supplier Evaluation: Consistently assess suppliers against established quality standards.
Collaborative Relationships: Build partnerships with key suppliers to enhance communication and resource allocation.
Effective supplier quality management can lead to a 15% increase in product quality, helping organizations achieve and maintain ISO 9001 certification.
Building a Quality Culture
Fostering a quality culture is essential for lasting effective resource management in ISO 9001. Organizations should cultivate an environment where every employee understands and values quality and resource utilization. Key components of this culture include:
Employee Engagement: Actively solicit feedback and involvement from employees in quality initiatives.
Recognition Programs: Reward employees for their commitment to quality and efficient resource management.
Creating a strong quality culture ensures ongoing dedication to quality goals and helps enhance resource utilization.
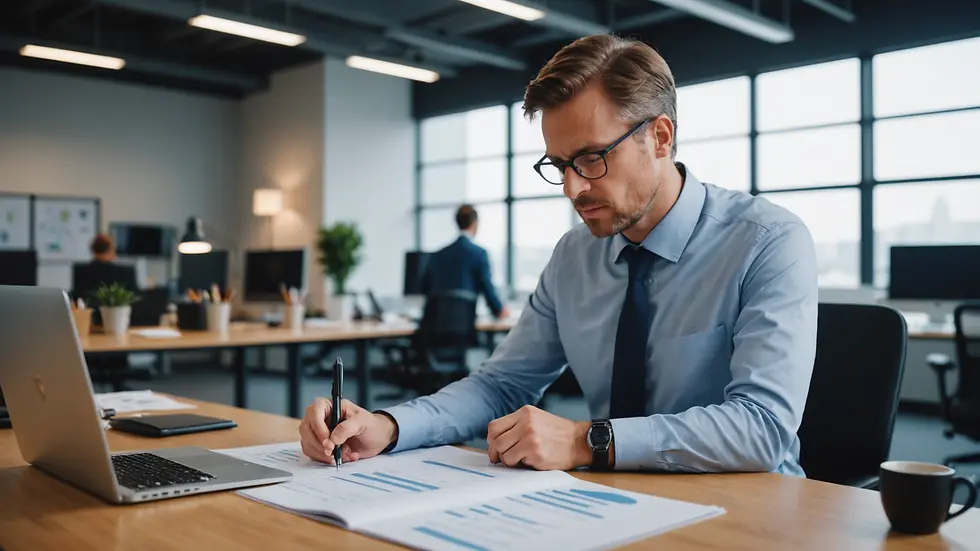
Achieving Quality Excellence
Effective resource management is vital for organizations pursuing ISO 9001 certification and striving for quality management excellence. By conducting resource assessments, setting clear objectives, and implementing best practices, organizations can optimize their resources to meet quality goals.
With a focus on continuous improvement, training, and robust monitoring, organizations can align their resource management with ISO 9001 requirements. Building a quality culture further enhances the likelihood of success, resulting in adherence to quality standards and heightened customer satisfaction.
Optimizing resource utilization not only aids organizations in achieving ISO 9001 certification but also fosters a quality-driven environment that benefits all stakeholders. Following these best practices positions organizations to achieve their quality management objectives while maintaining compliance with the ISO 9001 framework.
Comentarios