Enhancing Organizational Efficiency: Process Optimization Through ISO 9001 Principles
- islam Arid
- Apr 7
- 5 min read
In today’s competitive business landscape, organizations face constant pressure to improve efficiency and effectiveness in their operations. One of the most effective frameworks to help achieve these goals is ISO 9001. This internationally recognized standard outlines a robust structure for quality management systems, guiding organizations to identify inefficiencies and optimize processes. This post examines how to leverage ISO 9001 principles to enhance performance and bolster customer satisfaction.
Understanding ISO 9001
ISO 9001 serves as a benchmark for quality management systems (QMS) globally. It specifies requirements for organizations aiming to demonstrate their commitment to consistently delivering products and services that meet customer and regulatory demands. The ultimate objective of this standard is to boost customer satisfaction by emphasizing effective process optimization and a commitment to continuous improvement.
Key Principles of ISO 9001
The principles at the heart of ISO 9001 are essential for building an effective quality management system. These include:
Customer Focus: Understanding and meeting customer expectations is critical. For instance, research shows that 85% of organizations with a strong customer focus outperform their competitors.
Leadership: Strong leadership cultivates a shared vision and clear direction. Effective leaders engage employees, promoting a quality-centric culture.
Engagement of People: Involve contributors at all levels. Empowering employees leads to improved performance and sparks innovation.
Process Approach: Managing interrelated processes systematically boosts consistency and efficiency. For example, organizations that adopt this approach have reported up to a 30% reduction in operational costs.
Improvement: Pursuing continuous improvement should be ingrained in the organization’s culture, driving regular evaluations of processes. Some companies see a 50% reduction in defects by adopting this principle.
Evidence-Based Decision Making: Relying on data and analysis enhances the accuracy of decisions, leading to targeted actions.
Relationship Management: Maintaining productive relationships with stakeholders, including suppliers and customers, is vital for sustained performance.
By embracing these principles, organizations can align their operations with customer requirements while enhancing overall efficiency.
Identifying Inefficiencies Using ISO 9001
The first step in optimizing processes is recognizing inefficiencies within workflows. ISO 9001 provides a structured framework for identifying these shortcomings through:
1. Internal Audits
Internal audits are crucial for assessing the QMS’s effectiveness. Conducting regular ISO 9001 audits allows organizations to evaluate compliance, identify nonconformities, and address issues. For example, a manufacturing company that implemented quarterly audits reduced production errors by 40% by identifying outdated practices.
2. Document Control
ISO 9001 highlights the need for effective document control. Well-documented procedures ensure that workflows are understandable and current. An organization that updated its documentation system saw a 25% decrease in operational delays due to procedural errors.
3. Performance Metrics
Defining key performance indicators (KPIs) is essential for evaluating process efficiency. By collecting and analyzing data on these metrics, organizations can track their progress towards quality goals. A company that regularly reviews KPIs can spot inefficiencies and make adjustments, resulting in a 15% improvement in delivery times.
4. Management Review
Conducting routine management reviews is essential for evaluating the QMS’s performance. These reviews enable leadership to focus on strategic goals, assess audits, and prioritize customer feedback. Organizations that hold biannual management reviews often experience a significant improvement in process alignment and resource allocation.
Optimizing Processes Through ISO 9001
Once inefficiencies are identified, organizations can leverage ISO 9001 principles to implement impactful process optimization strategies. Here are several practical steps:
1. Streamlining Processes
Organizations should focus on eliminating redundant steps and refining workflows. Techniques from lean management can complement ISO 9001 efforts by emphasizing activities that add value. For instance, a service-based company that mapped its workflows identified and removed 20% of unnecessary steps, leading to faster service delivery.
2. Standardization of Procedures
Creating standardized procedures ensures uniformity in task execution, which enhances both quality and efficiency. ISO 9001 encourages concise, clear documentation that every employee can access. A retail chain that standardized its inventory process improved accuracy by 30%, reducing stock discrepancies.
3. Training and Development
Investing in employee training is vital for upholding processes and quality standards. ISO 9001 stresses the importance of competence among staff. Ongoing training not only keeps employees informed but also boosts efficiency. Companies that prioritize employee development see a direct correlation to productivity increases of 20% or more.
4. Utilizing Technology
Embracing technology can significantly enhance process optimization. Quality management software can automate routine tasks, such as documentation and compliance tracking. Businesses that adopt data analytics tools may discover trends or issues that manual processes might overlook, leading to more informed decisions and higher efficiency.
5. Implementing Corrective Actions
ISO 9001 mandates organizations to tackle nonconformities swiftly. A structured corrective action plan not only fixes problems but also includes analysis to prevent future occurrences. For example, a software development firm that implemented corrective actions reduced coding errors by 35%, significantly improving product quality.
Building a Quality Culture
Establishing a robust ISO 9001 framework relies heavily on cultivating a quality-focused culture. Here are strategies to foster this environment:
1. Communication
Maintain open lines of communication regarding quality objectives. Regularly informing staff about improvements and changes encourages engagement and accountability.
2. Recognition and Reward
Celebrate employees who contribute to quality enhancements. Recognizing efforts bolsters morale and fosters a sense of ownership among teams.
3. Leadership Example
Leaders set the tone for a quality culture. Active support for ISO 9001 initiatives from leadership encourages employees to embrace quality as a shared responsibility.
Continuous Improvement: The Heart of Process Optimization
Continuous improvement is critical for enhancing products, services, and processes, forming the backbone of ISO 9001. Key components of continuous improvement include:
1. Feedback Loops
Establish robust feedback systems to gather insights from customers and employees regularly. Creating mechanisms for response, such as surveys or suggestion boxes, empowers organizations to make needed adjustments quickly.
2. Progressive Auditing
Rather than viewing audits as isolated events, incorporate them as an ongoing practice. This approach fosters dialogue and engagement among teams as they consistently evaluate their QMS against ISO 9001 standards.
3. Benchmarking
Aligning performance metrics with industry best practices helps organizations identify improvement areas. By routinely comparing themselves to leading companies, organizations can adapt innovative strategies that enhance operational effectiveness.
4. Fostering Innovation
Encourage a workplace culture that values and rewards innovative thinking. When team members feel safe to suggest new approaches, organizations unlock potential improvements and efficiencies.
Embracing the Journey of Improvement
Optimizing organizational processes with ISO 9001 principles is more than a one-time goal; it’s an ongoing commitment to excellence. By pinpointing inefficiencies, applying best practices, and nurturing a culture centered on quality, companies can significantly enhance their performance and boost customer satisfaction.
As organizations prioritize efficiency and quality, ISO 9001 stands out as a potent tool for those dedicated to continual improvement. By fully adopting the principles of this quality management standard, organizations are not only streamlining their processes but also preparing for sustained success in their industries.
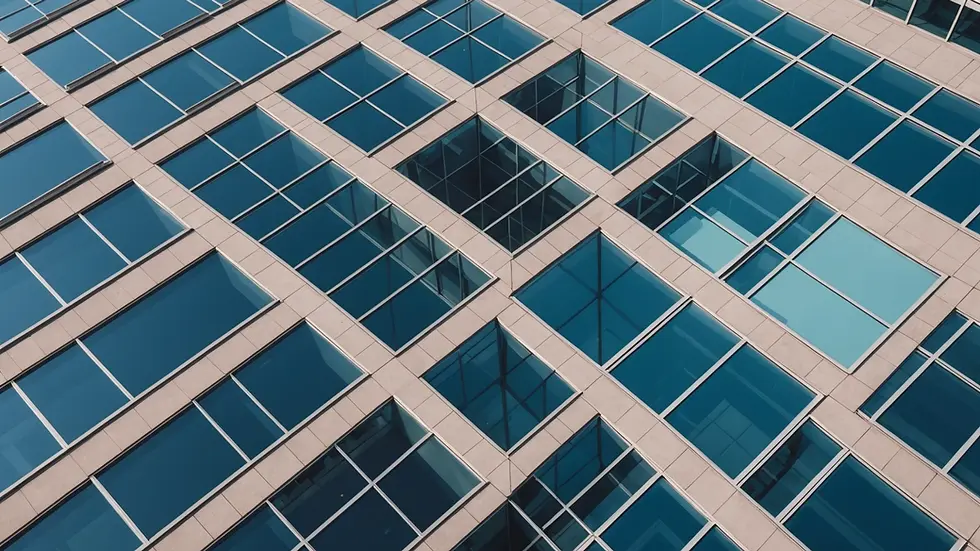
Comments