Enhancing Process Control and Monitoring: Implementing ISO 9001 Standards with Professional Precision
- islam Arid
- Apr 7
- 4 min read
In a world where quality can make or break a business, organizations are increasingly adopting structured frameworks like ISO 9001 to deliver excellence. This international standard for Quality Management Systems (QMS) is not just about meeting compliance; it is a powerful tool that drives continuous improvement and enhances process control. In this blog post, we will discuss actionable techniques for establishing effective process controls and monitoring systems under ISO 9001.
Understanding ISO 9001: A Foundation for Quality Management
ISO 9001 provides comprehensive guidelines for organizations aiming to implement a quality management system. The main goal is to consistently deliver high-quality products and services, ultimately leading to higher customer satisfaction. According to a survey by ISO, organizations that implement ISO 9001 have reported an average improvement of 16% in customer satisfaction.
To conform to ISO 9001, businesses must define quality objectives, assess risks, maintain thorough documentation, and conduct regular audits. These elements serve as the foundation for building robust process control and monitoring systems that are key to maintaining quality and compliance.
The Importance of Process Control in ISO 9001
Process control focuses on ensuring processes operate within defined limits to achieve consistent outcomes. The importance of effective process control in the context of ISO 9001 cannot be overstated:
Consistency in Performance: Companies that implement routine monitoring typically experience a 30% reduction in product defects, ensuring they deliver the same high-quality results consistently.
Risk Management: With process controls in place, organizations can identify potential risks early on. Evidence shows that companies focused on risk management have reduced operational losses by 25%.
Enhanced Efficiency: Organizations can streamline operations by 15% through regular evaluation of performance metrics, which helps them identify bottlenecks and optimize processes.
Customer Satisfaction: Delivering consistent quality results not only keeps current customers happy but also attracts new ones, leading to a 20% increase in customer loyalty.
Establishing strong process control systems is essential for organizations aiming for ISO 9001 compliance and overall performance improvement.
Establishing Effective Process Controls
Creating effective process controls requires a systematic approach that aligns with organizational needs. Here are crucial steps:
1. Defining Process Objectives
Begin by defining clear, measurable process objectives. Use SMART criteria—Specific, Measurable, Achievable, Relevant, and Time-bound—to ensure these objectives are actionable. For example, aim to reduce customer complaints by 10% over six months.
2. Documenting Procedures
Comprehensive documentation is vital for ensuring everyone understands their roles. ISO 9001 underlines the importance of document control, which includes maintaining records of processes and procedures. This not only aids compliance but also allows organizations to consistently monitor performance.
Utilize templates and checklists to streamline this documentation. For instance, having a standardized procedure for quality checks can greatly reduce ambiguity and errors.
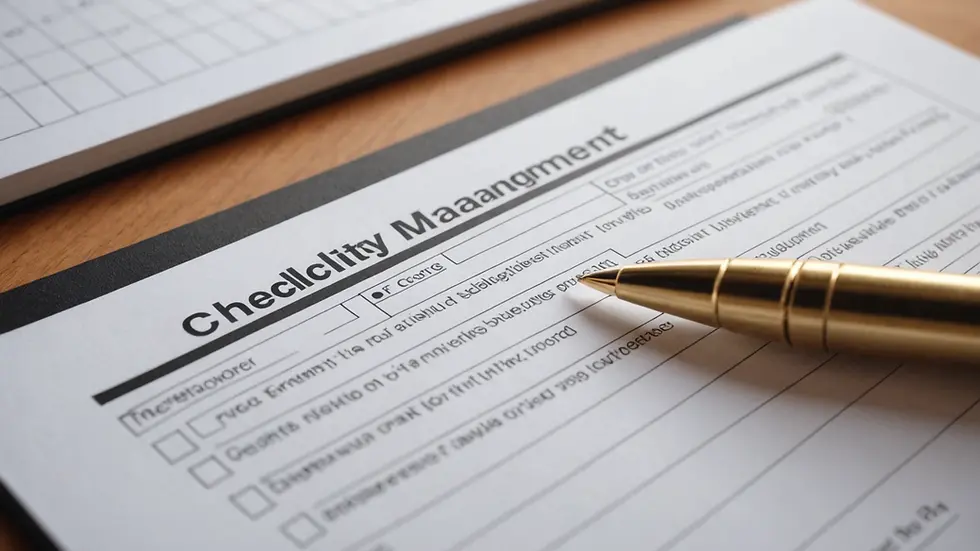
3. Implementing Performance Metrics
Establish relevant performance metrics to evaluate process effectiveness continuously. For example, the following Key Performance Indicators (KPIs) could be useful:
Time Efficiency: Measure how long it takes to complete each phase of production. For example, aim to cut production time by 5% each quarter.
Defect Rates: Track the number of defects per production cycle. A target could be reducing defects from 3% to 1%.
Customer Feedback: Collect and analyze customer satisfaction ratings after service delivery, aiming to reach a 90% customer satisfaction score within a year.
Regularly reviewing these metrics will help organizations spot areas that require improvement.
4. Conducting Internal Audits
Internal audits are critical in assessing the efficacy of process controls. During audits, organizations should:
Check documentation for accuracy.
Interview employees to ensure they understand procedures.
Review performance metrics and customer feedback.
Internal audits enable organizations to take corrective actions promptly and maintain quality.
5. Training and Development
Employee training is vital for successful process control. A robust training program enhances staff understanding of ISO 9001 requirements. Provide training in areas like:
Quality management principles
Importance of process control
Corrective action procedures
Risk management strategies
Investing in comprehensive training can lead to employees being 30% more effective in their roles, promoting a strong culture of quality.
Monitoring Process Performance
Once process controls are established, ongoing monitoring is essential for continuous improvement. Here are effective strategies for monitoring processes:
1. Regular Performance Reviews
Schedule monthly or quarterly performance reviews to assess whether processes are meeting established objectives. This ensures a consistent evaluation of the set KPIs.
2. Engaging in Management Reviews
ISO 9001 emphasizes the need for a management review process. Senior management should evaluate:
Audit results
Customer feedback
Performance against objectives
Resource allocation needs
Management reviews align all levels of the organization with quality improvement goals.
3. Addressing Nonconformities
Nonconformities will arise, making it essential to have a strategy for addressing them. Follow these steps:
Identification: Record the nonconformity as it arises.
Investigation: Analyze to find the root cause.
Corrective Actions: Implement actions to prevent recurrence.
A well-functioning corrective action system can improve process reliability by up to 40%.
4. Fostering a Culture of Continuous Improvement
Encourage employees to identify improvements regularly. Integrating techniques like Lean Management can help eliminate waste and enhance efficiency. Consider brainstorming sessions or feedback loops to generate innovative ideas.
Utilizing ISO 9001 Tools for Effective Monitoring
Several tools can facilitate process control and monitoring under ISO 9001:
1. Statistical Process Control (SPC)
SPC utilizes statistical methods for ongoing process monitoring. By analyzing real-time process data, organizations can maintain consistent output quality and respond swiftly to deviations.
2. Quality Management Software
Using quality management software can centralize documentation, track metrics, and manage audits. This streamlined approach can enhance the efficiency of monitoring activities significantly.
3. Root Cause Analysis (RCA) Tools
RCA tools like the 5 Whys or Fishbone diagrams help identify nonconformities' root causes. These tools improve organizations' overall understanding of their processes, leading to more effective monitoring and control systems.
Achieving Excellence through ISO 9001
Embarking on the journey of effective process control and monitoring is crucial for organizations seeking ISO 9001 certification. By establishing clear objectives, documenting procedures, and committing to training, businesses can cultivate a culture of continuous improvement.
Utilizing modern tools and techniques, organizations can not only meet compliance but also enhance operational efficiency and customer satisfaction. In a competitive landscape, effective quality management under ISO 9001 is not just a standard—it's a pathway to excellence.
Commentaires