Optimizing ISO 9001 Performance: Implementing Industry Benchmarks for Continuous Improvement
- islam Arid
- Apr 30
- 4 min read
In a world where quality management is essential for success, meeting the standards of ISO 9001 isn't simply about compliance; it is a chance to improve your entire organization. ISO 9001 is a cornerstone in quality management systems (QMS), providing a structured approach to enhance business processes. One of the most effective ways to achieve this is by leveraging benchmarking against industry standards. This article explores how you can implement ISO 9001 benchmarking to measure your organization's performance alongside industry leaders, resulting in the identification of gaps and opportunities for noticeable improvement.
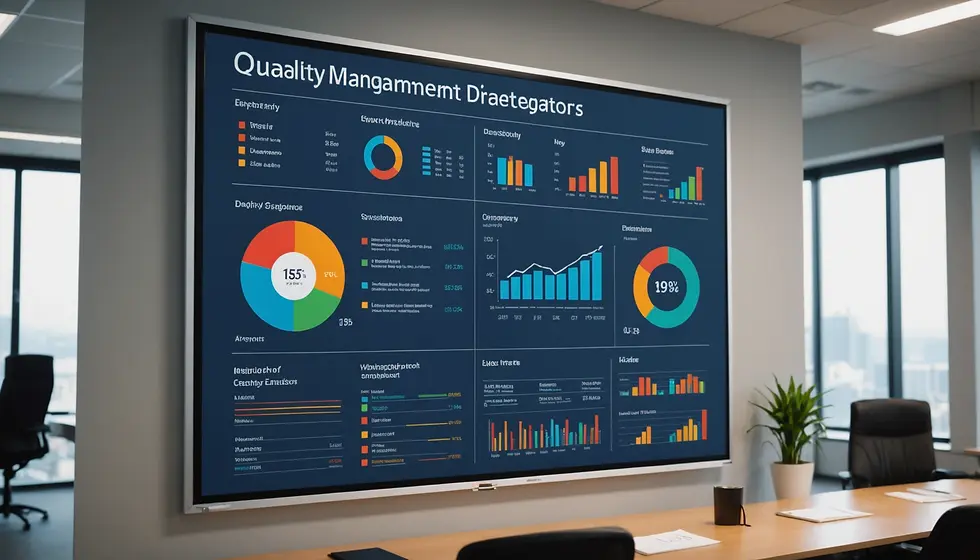
Understanding ISO 9001 and Its Significance
ISO 9001 is an international standard that outlines the requirements for a quality management system. It helps organizations ensure they meet customer and regulatory needs while focusing on improving customer satisfaction. This standard is versatile and applies to organizations of all sizes and industries.
By embracing ISO 9001's core principles—like customer focus, leadership involvement, and continuous enhancement—companies can foster a strong quality culture. For instance, organizations applying these principles have reported up to a 20% increase in customer satisfaction rates and a 15% reduction in complaints. Compliance with ISO 9001 not only meets regulatory needs but also enhances quality control practices.
The Need for Benchmarking in ISO 9001 Performance
Benchmarking allows organizations to assess their performance in relation to industry standards. This process is especially beneficial for those working under ISO 9001. By evaluating performance metrics against peers, businesses can gain insights into areas of strength and identify weaknesses.
For example, when a company compares its customer satisfaction ratings with those of similar businesses, it may discover that despite achieving an 80% satisfaction rate, industry leaders are achieving scores above 90%. Such insights guide targeted improvements, help organizations comply with standards, and ultimately drive operational success.
Setting Up the Benchmarking Process
1. Define Objectives
Establishing clear objectives is crucial for any benchmarking initiative. Organizations need to determine what they aim to achieve, such as improving customer experience, reducing errors, or enhancing process efficiency.
For example, a goal to decrease nonconformity rates by 25% within a year would provide a clear target that helps guide benchmarking efforts and keeps the organization focused.
2. Identify Key Performance Indicators (KPIs)
Selecting the right KPIs is essential for effective benchmarking. Key metrics related to ISO 9001 may include:
Customer satisfaction ratings: Measure through surveys and feedback.
Rate of nonconformities: Track instances where products or services fall short of quality expectations.
Internal audit results: Evaluate the consistency and thoroughness of internal audits.
Process cycle times: Monitor the time taken to complete key business processes.
Training effectiveness: Assess the impact of training programs on employee performance.
These KPIs offer measurable data on how well the organization adheres to ISO 9001 and highlight areas ripe for improvement.
3. Research Benchmarking Partners
Identifying suitable benchmarking partners is vital. Seek organizations within the same industry that already have a solid ISO 9001 framework. This group could include competitors or businesses with similar goals.
Collaborative relationships with these partners allow for valuable data sharing. According to industry surveys, organizations that engage in benchmarking with peers are 50% more likely to achieve significant performance improvements.
Conducting a Benchmarking Analysis
1. Collect Data
Data collection serves as the cornerstone of the benchmarking effort. Gather both quantitative and qualitative data on your performance metrics and those of your benchmarking partners. Information can include performance reviews, customer feedback, and compliance audit findings.
2. Analyze Gaps
After collecting data, analyze the performance gaps between your organization and others. Identifying specific areas where your performance lags helps in formulating action plans for improvement.
Suppose your competitor has achieved a 10% quicker process cycle time. By focusing on this gap, your organization can streamline processes and improve efficiency.
3. Develop Action Plans
Following the gap analysis, create actionable plans that outline the steps necessary for improvement. These plans should address any weaknesses and align with ISO 9001 standards.
For instance, if your analysis shows that customer satisfaction feedback is lacking, the action plan can involve implementing more robust follow-up processes and trained customer service teams.
Implementing Continuous Improvement
1. Monitor Progress
Benchmarking is an ongoing process. Regularly monitoring performance against established metrics helps ensure that organizations stay on track towards their quality goals.
Implement quarterly reviews to assess KPIs and update action plans based on what the data reveals.
2. Foster a Quality Culture
Building a culture of quality is crucial for sustaining improvements. Engaging employees at all levels empowers them to take responsibility for quality management.
Consider hosting workshops and training sessions to enhance understanding of ISO 9001 principles. Research shows that companies with a strong quality culture see a 25% increase in employee engagement.
3. Benchmark Regularly
Commit to regular benchmarking exercises. As industry standards change, evaluating your performance against the latest benchmarks will keep your organization competitive and ensure continuous improvement in quality management systems.
Common Challenges in Benchmarking ISO 9001 Performance
While the advantages of benchmarking are clear, organizations can face challenges:
1. Data Limitations
Access to reliable data may be difficult. Some organizations often hesitate to share performance data due to concerns over confidentiality. Building trusting relationships can encourage transparency.
2. Misalignment of Objectives
If the benchmarking objectives do not clearly align with organizational goals, the process may be ineffective. Ensure all benchmarking efforts directly support your quality objectives.
3. Resistance to Change
Organizational culture can obstruct the implementation of improvements. Employees may resist changes prompted by benchmarking insights. Effectively communicating the benefits of such changes is essential to gaining support.
Final Thoughts
In the quest for operational excellence, implementing ISO 9001 benchmarking can significantly transform the way organizations optimize their quality management performance. By assessing internal metrics against industry standards, organizations can pinpoint gaps, enhance processes, and nurture an unwavering commitment to continuous improvement.
The road to effective ISO 9001 implementation requires ongoing evaluation and adaptation. With a structured benchmarking approach, companies can meet compliance requirements and aim for heightened customer satisfaction and operational efficiency.
Letting the philosophy of continuous improvement guide organizational efforts ensures that the journey toward ISO 9001 certification is more than a mere destination; it becomes an integral part of the organization’s success narrative. By fostering a commitment to quality, companies can not only meet standards but also thrive in an ever-competitive landscape.
Comments