Establishing a Culture of Continuous Improvement through ISO 9001 Implementation and Quality Standards
- islam Arid
- Apr 30
- 5 min read
Creating a culture of continuous improvement grabs attention because it impacts every aspect of an organization. When companies aim to enhance operational efficiency and customer satisfaction, ISO 9001 serves as a powerful guide. This globally recognized standard promotes a work environment where improvement is not just a goal but a way of life. This blog post explores how implementing ISO 9001 can foster a culture of continuous improvement and highlights the essential roles that all organizational levels play in this journey.
Understanding ISO 9001 and Its Importance
ISO 9001 is an influential standard for Quality Management Systems (QMS). It provides clear guidelines to help organizations enhance their quality management processes. Following ISO 9001 helps companies consistently deliver quality products and services, meet customer expectations, and comply with regulatory requirements.
In fact, companies that implement ISO 9001 have reported a 10-20% increase in customer satisfaction within the first year. By committing to ISO 9001, organizations transition from a reactive to a proactive mindset about quality management, which is crucial for staying competitive in today’s fast-paced market.
The Role of Continuous Improvement in ISO 9001
Continuous improvement is at the heart of ISO 9001. Often linked to the concept of Kaizen, it encourages organizations to create a workplace where every employee is empowered to suggest changes.
Defining Continuous Improvement (Kaizen)
Kaizen means "change for better." It promotes small, consistent improvements in processes, products, or services. For example, a manufacturing team may find a way to reduce product defects by implementing a simple checklist, leading to a 25% reduction in errors over six months. Such incremental changes foster a culture of ongoing enhancement.
Benefits of Embracing Continuous Improvement
Improved Efficiency: Organizations can cut costs by 15-30% by streamlining processes and eliminating waste. A case study from a manufacturing company showed how introducing continuous improvement practices significantly reduced production time.
Higher Employee Engagement: When employees contribute to improvement efforts, they feel more valued. Engaged employees can lead to productivity increases of up to 20%.
Better Customer Satisfaction: Continuous improvement strategies lead to higher quality, resulting in increased customer loyalty. A study indicated that companies focused on quality improvements experienced a 20% rise in repeat business.
Establishing a Framework for Continuous Improvement with ISO 9001
Setting Quality Objectives
A vital component of fostering a culture of continuous improvement through ISO 9001 is setting quality objectives. These objectives should reflect the SMART criteria (specific, measurable, achievable, relevant, and time-bound). For example, a business might aim to reduce customer complaints by 30% over a year, guiding efforts across departments.
Leadership Commitment
Leadership plays a pivotal role in demonstrating commitment to quality. When top management actively participates in establishing the QMS and encourages participation throughout the organization, it sets a positive example. Regular management reviews, assessing alignment with quality objectives and compliance with ISO 9001, are essential for driving company-wide efforts.
Effective Training and Development
Empowering Employees through Training
Training is crucial for promoting a culture of continuous improvement. Organizations should invest in training that covers:
ISO 9001 Requirements: Ensuring that employees understand the standard’s applications is vital. Research shows that effective training can improve compliance rates by 40%.
Problem-Solving Skills: Equip employees with the ability to recognize and resolve issues, which can lead to quicker turnaround times.
Process Improvement Techniques: Teach methodologies like Lean Management or Six Sigma for ongoing improvement. For instance, a retail company found that after training on Lean principles, they reduced inventory holding costs by 22%.
Encouraging Knowledge Sharing
Creating platforms for employees to share insights fosters collaboration. This can include regular team meetings or digital forums. Sharing best practices can lead to innovative solutions and a unified approach to quality.
Implementing ISO 9001 Procedures
Document Control
Maintaining effective document control is essential for clarity within processes. ISO 9001 has specific requirements regarding record-keeping and versioning. A manufacturing firm that revamped its document management reported improved process adherence, enhancing efficiency by 18%.
Performing Internal Audits
Regular internal audits not only ensure compliance with ISO 9001 but also identify areas for improvement. A global study showed that organizations conducting internal assessments reported a 22% boost in operational effectiveness as they quickly addressed gaps in performance.
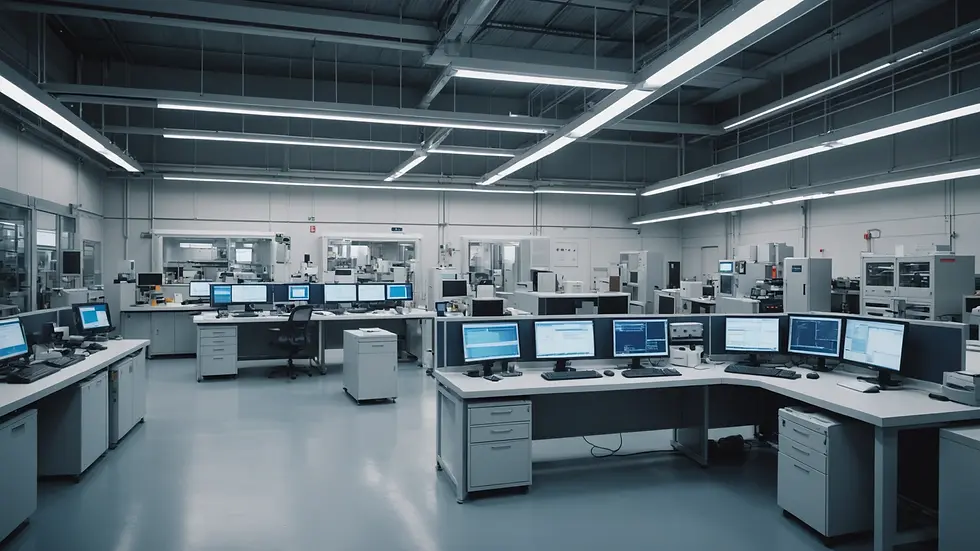
Managing Nonconformities and Corrective Actions
Identifying Nonconformities
Organizations should treat nonconformities as learning opportunities. For example, if a product fails quality checks, analyzing the root cause and addressing it can prevent future issues.
Implementing Corrective Actions
ISO 9001 requires procedures for managing nonconformities, including identifying causes, implementing corrective actions, and monitoring effectiveness. A systematic approach helps build accountability and a commitment to maintaining high standards.
Cultivating a Quality Culture
Engaging Employees at All Levels
A thriving continuous improvement culture relies on employee engagement. By involving everyone in improvement initiatives, organizations create a sense of ownership. This can lead to a 15-30% increase in employee satisfaction.
Recognizing and Rewarding Contributions
Celebrating employee contributions fosters ongoing engagement. Recognition programs or performance rewards encourage teams to stay committed to quality. Companies that recognize their employees have reported 20% higher retention rates.
Performance Metrics and Management Review
Defining Key Performance Indicators (KPIs)
Organizations should define KPIs to measure the impact of continuous improvement efforts. These metrics help assess progress and identify trends. Companies that actively track KPIs report more strategic decision-making, leading to a 10% increase in operational performance.
Conducting Regular Management Reviews
Management reviews help evaluate the effectiveness of the ISO 9001 QMS. Regular discussions on KPI performance, customer feedback, and nonconformities are opportunities to refine objectives. This cycle of evaluation and improvement can yield significant benefits over time.
Building Relationships with Suppliers
Assessing Supplier Quality
Organizations must also focus on the quality of their suppliers. Collaborating with suppliers on quality management fosters better processes across the supply chain. A logistics firm noted that assessing supplier quality led to a 15% improvement in delivery times.
Investing in Supplier Training
By investing in training for suppliers regarding ISO 9001 and quality practices, organizations enhance quality throughout the supply chain. Such collaboration can lead to overall improvements in product and service quality.
Embracing Continuous Improvement
Establishing a culture of continuous improvement through ISO 9001 implementation is about a commitment to quality that touches every corner of the organization. By integrating quality standards into the company culture, organizations empower every individual to contribute to enhancements.
Continuous improvement is a journey that requires dedication to quality management principles. By embracing ISO 9001, investing in training, promoting employee engagement, and maintaining open communication, organizations can set the stage for success in an evolving landscape.
The pursuit of continuous improvement offers countless opportunities to innovate and enhance operations. With the right mindset and strategies, organizations can achieve their goals for quality and excellence.
Commentaires