Maximizing Efficiency: Developing and Implementing ISO 9001 Corrective and Preventive Action Plans for Quality Excellence
- islam Arid
- Apr 30
- 5 min read
Engaging Start
In a rapidly changing business landscape, ensuring top-notch quality isn't just a goal—it's a necessity. Organizations that prioritize quality gain a competitive edge, ensuring customer trust and loyalty. One vital tool in achieving this is the ISO 9001 standard, which provides a roadmap for effective quality management.
A central aspect of this framework is the Corrective and Preventive Action (CAPA) plans. This blog post will guide you on creating CAPA plans that effectively tackle issues, prevent future problems, and foster a culture of continuous improvement.
Understanding ISO 9001 and Its Importance
ISO 9001 is a globally recognized standard that helps organizations create quality management systems (QMS). Adhering to these guidelines helps to enhance customer satisfaction and meet regulatory demands. Attaining ISO 9001 certification sends a strong message: your organization is dedicated to maintaining quality across all business processes.
The significance of ISO 9001 is immense. According to a survey by ISO, over 1.1 million organizations worldwide hold ISO 9001 certifications. By implementing ISO 9001 effectively, companies can streamline operations, increase efficiency, and significantly reduce costs.
The Role of Corrective and Preventive Actions in Quality Management
Corrective Actions
Corrective actions are reactive measures needed when nonconformities arise. For example, suppose a manufacturing plant faces repeated equipment failures. In that case, a corrective action plan might involve investigating the failures to find the root cause and implementing repairs or replacements. Reactively addressing these issues not only resolves them but also strengthens the organization's QMS.
Preventive Actions
Preventive actions focus on stopping potential nonconformities before they occur. For instance, a software company might implement regular system updates and employee training sessions to prevent bugs in future software releases. By developing preventive measures, organizations can save time and money while maintaining high-quality standards.
By integrating both corrective and preventive actions, businesses enhance overall efficiency and establish a culture of continuous quality improvement.
Key Steps in Developing Effective CAPA Plans
1. Identify the Nonconformity
Start the CAPA process by identifying the specific issue. This may come from customer feedback, internal audits, or regular process evaluations. For example, if a customer repeatedly reports delays in service delivery, these complaints should prompt a thorough investigation.
Use metrics and analysis tools, such as Control Charts, to spot trends. By accurately defining the problem, teams can narrow down their focus to develop effective solutions.
2. Determine the Root Cause
Pinpointing the root cause of a nonconformity is key to developing useful corrective actions. Tools like the "Five Whys" technique can help. If a product consistently fails quality checks, you might ask why it fails, then dig deeper with each answer. This approach often uncovers underlying issues like inadequate training or flawed processes.
Understanding and addressing root causes ensures that problems do not just recur.
3. Develop Corrective Actions
Once the root cause is identified, it is time to create specific corrective actions. These actions should be:
Specific: Clearly state what needs to be done.
Measurable: Define how success will be evaluated.
Achievable: Actions should be feasible to implement.
Relevant: Align corrective actions with broader organizational goals.
Time-bound: Set deadlines for implementing actions.
Involving relevant stakeholders is crucial to ensure full support and cooperation in executing corrective actions.
4. Implement Preventive Actions
After corrective measures are established, focus on preventive actions to guard against similar issues. For example, if a recurring quality issue stems from employee mistakes, incorporate regular training sessions into employee development programs. This proactive approach helps ensure quality is prioritized across the organization.
5. Monitor and Evaluate Effectiveness
It's essential to monitor the implemented corrective and preventive actions to determine their effectiveness. Regular audits and data analysis can highlight whether the measures are achieving their intended outcomes. If results fall short, be prepared to revisit the actions taken and make necessary adjustments.
6. Document the Process
Meticulous documentation is vital within the ISO 9001 framework. Keeping detailed records of your CAPA processes not only demonstrates compliance but also serves as a guide for future audits and assessments. Documentation fosters transparency and accountability within the organization.
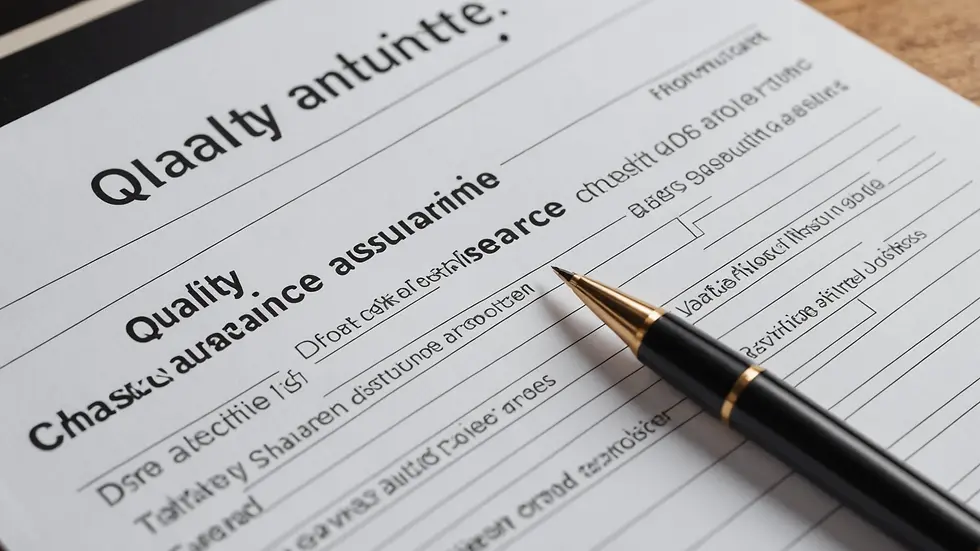
Best Practices for Creating ISO 9001 CAPA Plans
Foster a Quality Culture
Creating a culture that prioritizes quality is essential for the success of CAPA plans. This involves engaging everyone from top management to frontline employees. Encourage open discussions about quality issues, promoting a safe environment where employees can report nonconformities without fearing consequences.
This culture leads to swifter problem detection and resolution.
Utilize ISO 9001 Tools
Investing in ISO 9001 tools can streamline CAPA plan development and execution. For instance, using Quality Management Software can efficiently track nonconformities and actions taken, providing clear visibility at all stages of the process.
Engage in Continuous Improvement
Establish a mindset focused on continuous improvement throughout the organization. Conduct regular management reviews and audits to assess effectiveness and find new improvement opportunities.
Harness feedback from both customers and employees to inspire innovative solutions.
Provide Training and Development
Invest in training for all employees. Make sure they understand ISO 9001 requirements and CAPA processes. When they have the right knowledge, employees become empowered to make meaningful contributions to quality improvement initiatives.
Benchmark Against Industry Standards
Regularly compare your performance metrics with industry standards to better understand where your organization stands. This evaluation sheds light on areas for improvement and allows for the integration of best practices from high-performing organizations.
Measuring Success: Key Performance Indicators for CAPA
To gauge the effectiveness of CAPA plans, organizations should establish specific key performance indicators (KPIs). These metrics guide organizations in assessing the success of corrective and preventive actions.
Examples of CAPA KPIs:
Number of Nonconformities Identified: Monitor how many issues arise within a defined period.
Time to Resolution: Track the average time needed to implement corrective actions after a nonconformity is reported.
Repeat Nonconformities: Watch for recurring issues to assess the effectiveness of implemented solutions.
Customer Satisfaction: Review customer feedback and satisfaction ratings before and after implementing CAPA to measure their impact.
Audit Results: Analyze internal and external audit results over time to evaluate compliance and process improvements.
Setting these KPIs is vital for monitoring progress and informing future quality management strategies.
Reflections on Quality and Improvement
Effective Corrective and Preventive Action plans aligned with ISO 9001 are essential for any organization aiming for quality excellence. By diligently identifying problems, uncovering root causes, and designing targeted solutions, organizations can build a culture of continuous improvement.
Integrating best practices, investing in training, and consistently monitoring performance ensures that CAPA plans positively influence organizational goals.
Remember, quality management goes beyond compliance; it’s about fostering a sustainable quality culture that enhances customer satisfaction and drives business success.
By embracing ISO 9001 principles and effectively executing CAPA plans, organizations can maximize efficiency and lay a strong foundation for ongoing process improvement.
Through understanding and implementing these strategies, you can unlock the full potential of ISO 9001, making quality an integral part of your operations and paving the way for long-term success and growth.
Comments