Building a Strong Quality Culture: ISO 9001 Implementation and Leadership Role in Quality Management
- islam Arid
- Apr 30
- 4 min read
Engaging Beginning
In a world where customer choices are plentiful, the need for a strong quality culture becomes critically important. Organizations that prioritize quality can outperform their competitors, enhance customer satisfaction, and pave the way for long-term success. A thriving quality culture not only supports compliance with standards like ISO 9001 but also inspires employees to contribute to consistent improvement. Let’s explore how effective ISO 9001 implementation can shape a culture of quality and the essential role leadership plays in this process.
Understanding ISO 9001
ISO 9001 is a globally accepted standard for quality management systems (QMS). Organizations that embrace ISO 9001 can improve operational efficiency and customer satisfaction through structured practices. The framework defines specific requirements to achieve ISO 9001 certification. However, simply obtaining the certification is not enough—it is the leadership’s dedication to embedding quality management values that truly makes a difference.
For example, organizations that implemented ISO 9001 reported a 16% improvement in operational efficiency. They also saw a reduction in defects by up to 30%, showcasing how a focus on quality can translate into tangible benefits.
The Role of Leadership in Quality Management
Leadership is vital in building and promoting a robust quality culture. Leaders set the foundation for quality management practices by clearly communicating the organization’s quality policies and objectives. When leaders demonstrate their commitment to quality, they show that it is a core aspect of the organization’s mission.
For instance, when leaders participate in ISO 9001 audits or management reviews, they reinforce their commitment to quality and ensure that issues are addressed promptly. This helps to create a culture where everyone understands the importance of their role in delivering quality.
Establishing a Vision for Quality
Creating a clear vision for quality is fundamental to developing a culture of excellence. Leaders should articulate this vision in a way that resonates with all employees. When team members grasp how quality initiatives contribute to personal and organizational success, they are more likely to engage with these goals.
Setting performance objectives aligned with ISO 9001 standards can provide insight into areas needing improvement. For instance, a company might track customer satisfaction rates, aiming for a 10% increase year over year, to motivate employees towards quality enhancements.
Encouraging Employee Engagement
Engaging employees in the quality management process is crucial. Leaders can foster this engagement by promoting ownership of quality initiatives among team members. This can be achieved through dedicated training sessions on ISO 9001 procedures, enabling employees to understand their roles and responsibilities.
Creating an environment that welcomes open discussions about quality challenges leads to collaboration. Employees should feel safe suggesting improvements or discussing issues without fear of negative consequences. Regular internal audits can also serve as feedback mechanisms, reinforcing shared responsibility for quality.
Recognizing and Rewarding Contributions
Recognizing employee contributions to quality improvement can significantly boost morale and motivation. Acknowledging successes, whether big or small, can enhance employee satisfaction and reinforce a culture of quality.
For example, a monthly recognition program could reward individuals or teams that have implemented effective quality improvements. This not only uplifts the spirits of employees but also cultivates a culture where everyone is eager to contribute toward organizational excellence.
Integrating Quality into Daily Operations
For a robust quality culture to take root, quality management principles must be woven into everyday operations. Employees should consider quality in every task they perform, supported by clear ISO 9001 procedures.
Adopting methodologies like Lean Management can help streamline processes. Companies that implemented Lean practices reported a 25% reduction in waste and improved productivity by up to 20%. Monitoring performance metrics can further highlight areas for improvement and prompt timely corrective actions.
Developing a Quality Control System
A comprehensive quality control system is essential for sustaining high standards in product and service delivery. This system should include documentation processes and risk management strategies to identify potential issues before they escalate.
Regular internal audits and ongoing evaluations can ensure compliance and optimize the quality management system. Insights gained from ISO 9001 audits can spotlight weaknesses, leading organizations to exceed quality standards and enhance customer satisfaction.
Tracking and Managing Nonconformities
Quickly addressing nonconformities is vital for maintaining a strong quality culture. Organizations should implement systematic methods for identifying, documenting, and rectifying nonconformities. This might involve conducting root cause analyses to understand issues and developing preventive measures.
Leadership should support employees in these efforts, fostering confidence to tackle quality challenges head-on. Emphasizing learning from mistakes rather than assigning blame encourages a resilient organization that is agile in its approach to quality.
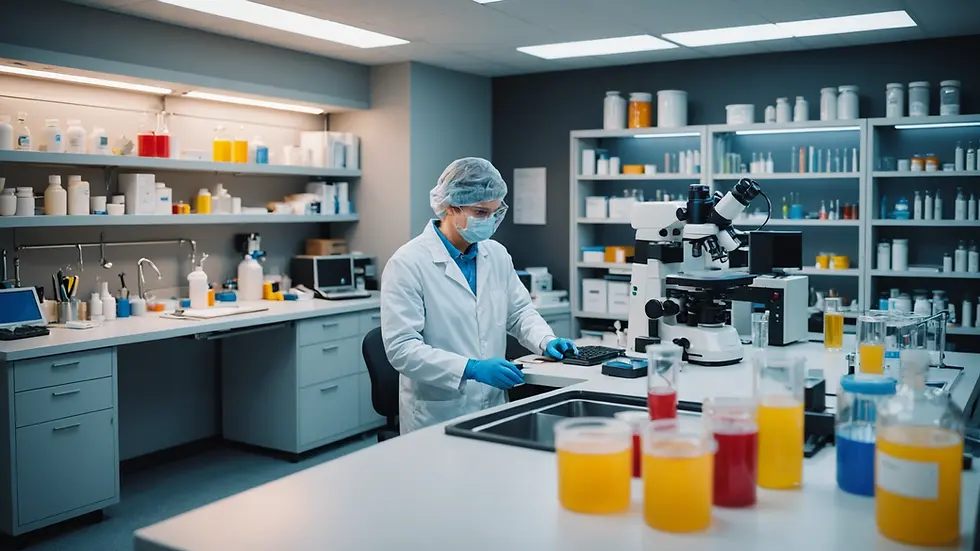
The Impact of a Quality Culture on Customer Satisfaction
The benefits of fostering a strong quality culture extend directly to customer satisfaction. Businesses that prioritize quality management are better equipped to meet and exceed customer expectations, leading to increased loyalty. Research indicates that companies with a strong quality focus can see customer loyalty grow by as much as 30%.
By ensuring consistent product and service quality, organizations can create reliable and positive customer experiences. Proactively addressing customer feedback based on ISO 9001 guidelines creates a loop of continuous improvement.
Leveraging Feedback for Continuous Improvement
Continuous improvement is a cornerstone of effective quality management. Organizations should actively seek customer feedback to inform quality initiatives. An ongoing dialogue with customers provides valuable insights that can sharpen processes.
Using tools like Plan-Do-Check-Act (PDCA) cycles allows organizations to adopt a systematic approach to refining quality measures. Testing changes, assessing their impact, and fine-tuning strategies can help businesses remain responsive to evolving customer needs.
Wrapping Up the Journey
Cultivating a strong quality culture through ISO 9001 implementation is a dynamic journey requiring commitment and involvement from both leadership and employees. Leaders shape the foundation for quality management, emphasizing excellence, addressing issues, and creating an environment focused on quality.
As organizations embrace this quality culture, they align their goals with customer satisfaction and operational efficiency. This alignment paves the way for improved business performance and enhanced relationships with customers. By embracing continuous improvement, organizations not only meet ISO 9001 standards but also set themselves up for sustained growth.
By focusing on a quality-driven environment, organizations embark on a transformative path towards better compliance, stronger customer relations, and optimized processes that lead to lasting success.
コメント