How to Integrate Six Sigma and Lean Tools into ISO 9001 for Advanced Quality Management
- islam Arid
- Apr 30
- 4 min read
In today's fast-paced and competitive landscape, organizations constantly seek effective methods to enhance their quality management practices. Integrating ISO 9001, Six Sigma, and Lean methodologies offers a powerful strategy for achieving advanced quality management. This blog post will explore practical steps to synergistically combine these frameworks, enhancing quality management within your organization.
Understanding ISO 9001
ISO 9001 is a globally recognized standard for quality management systems (QMS). It provides a framework for organizations to consistently deliver products and services that fulfill customer and regulatory requirements. One key goal of ISO 9001 is improving customer satisfaction. This is achieved through a systematic approach to process management, improvement, and risk management.
By documenting procedures, conducting internal audits, and performing management reviews, organizations can ensure compliance and foster continuous improvement. For example, organizations that implemented ISO 9001 reported a 20% increase in customer satisfaction scores within the first year. These practices help cultivate a robust quality culture that promotes efficiency and effectiveness.
The Fundamentals of Six Sigma
Six Sigma is a data-driven methodology targeted at reducing defects and variances in processes. It uses the DMAIC (Define, Measure, Analyze, Improve, Control) framework to identify root causes of issues and develop effective solutions.
Six Sigma emphasizes measurement and analysis, enabling organizations to quantify performance metrics and identify key improvement areas. For instance, companies applying Six Sigma methodologies saw a 50% reduction in defects, significantly raising overall product quality and ensuring customer satisfaction.
The Lean Approach
Lean management centers on maximizing value by minimizing waste. It highlights efficiency through the elimination of non-value-added activities, streamlining processes, and enhancing customer value.
Key principles of Lean include:
Value: Identify what is valuable to the customer. For example, a fast-food chain redefined its menu based on customer preferences, increasing sales by 15%.
Value Stream: Map out steps involved in delivering a product or service. A manufacturer that used value stream mapping identified wasteful steps, reducing production time by 25%.
Integrating Lean with ISO 9001 can create a powerful synergy, enhancing compliance with quality standards while streamlining operations for optimal performance.
The Case for Integration
Combining ISO 9001 with Six Sigma and Lean methodologies can lead to significant improvements in quality management practices. Here's why integration matters:
Holistic Improvement: Integration allows organizations to enhance documentation, optimize processes, and reduce waste simultaneously.
Data-Driven Decisions: The data-centric approach of Six Sigma enriches ISO 9001, providing insights for informed decision-making regarding quality improvements.
Enhanced Customer Satisfaction: A focus on process efficiency and defect reduction can improve customer satisfaction. Reports indicate that organizations using this integrated approach achieved customer satisfaction ratings above 90%.
Continuous Improvement: All three methodologies emphasize continuous improvement, fostering a culture of ongoing progress.
Steps for Integration
Integrating Six Sigma and Lean tools into an ISO 9001 framework requires thoughtful planning and execution. Here are essential steps to guide the integration process:
Step 1: Assess Current Practices
Begin by auditing existing quality management practices. Evaluate compliance with ISO 9001 standards, the effectiveness of current processes, and potential benefits from Lean and Six Sigma.
Step 2: Define Quality Objectives
Establish clear quality objectives aligned with organizational goals. Ensure these objectives uphold ISO 9001 standards while integrating Six Sigma's focus on defect reduction and Lean's waste elimination.
Step 3: Train and Develop Skills
Invest in training programs to build competencies in Six Sigma and Lean tools. Encourage a knowledge-sharing culture where best practices are exchanged. This supports a continuous learning environment.
Step 4: Implement Lean Tools
Employ Lean tools such as value stream mapping, 5S, and Kaizen. These tools identify and eliminate waste within processes. Integrate them into the ISO 9001 framework to boost efficiency while ensuring compliance.
Step 5: Utilize Six Sigma Methodologies
Adopt the DMAIC framework to drive process improvement initiatives. Systematically document each phase to maintain compliance with ISO 9001 procedures. Analyzing data helps identify performance metrics and implement corrective actions.
Step 6: Conduct Regular Audits
Perform internal audits frequently to assess compliance with ISO 9001 and evaluate Lean and Six Sigma initiatives. Identify improvement areas and adapt processes for continuous enhancement.
Step 7: Focus on Customer Feedback
Analyze customer feedback to gauge satisfaction levels. Use this information to refine processes and enhance quality control measures. Meeting customer needs is crucial for achieving ISO 9001 certification.
Step 8: Create a Culture of Continuous Improvement
Build a culture that encourages continuous improvement. Initiatives like employee suggestion programs can generate innovative ideas and support quality objectives.
Step 9: Review and Refine
Conduct periodic reviews to assess the effectiveness of the integration strategy. Use performance metrics for evaluation and refine processes when necessary, documenting changes as required by ISO 9001.
Benefits of Integration
Integrating Six Sigma and Lean tools into ISO 9001 offers many benefits that positively impact organizational performance:
Enhanced Efficiency: Streamlining processes and waste reduction boosts productivity and lowers operational costs.
Improved Quality Control: A data-driven approach enhances the ability to manage nonconformities and implement corrective actions quickly.
Stronger Compliance: Integration reinforces compliance with ISO 9001 standards, boosting the organization's reputation and credibility.
Increased Employee Engagement: A culture of continuous improvement encourages employee involvement, leading to higher job satisfaction and retention rates.
Sustainable Growth: A commitment to continuous improvement lays the groundwork for sustainable growth, enabling adaptability in an ever-changing market.
Challenges to Consider
While integrating Six Sigma and Lean with ISO 9001 offers notable advantages, organizations should be cautious of potential challenges:
Resistance to Change: Employees may resist adopting new methods. Clear communication and training can address concerns and foster buy-in.
Resource Intensive: Integration requires time and financial investment. Organizations must allocate sufficient resources and support for successful implementation.
Alignment with Organizational Culture: Integration success heavily depends on organizational culture. Leaders must promote a culture of quality and continuous improvement.
Advancing Quality Management Practices
Integrating Six Sigma and Lean tools into the ISO 9001 framework significantly advances quality management practices. By combining these methodologies systematically, organizations can improve efficiency, enhance customer satisfaction, and foster a culture centered on quality and continuous improvement.
As the competitive business landscape continues to evolve, aligning ISO 9001 with Six Sigma and Lean methodologies is not just beneficial; it is necessary for organizations aiming for excellence. By embracing the integration process, companies can position themselves as leaders in quality management, ultimately achieving their strategic objectives and exceeding customer expectations.
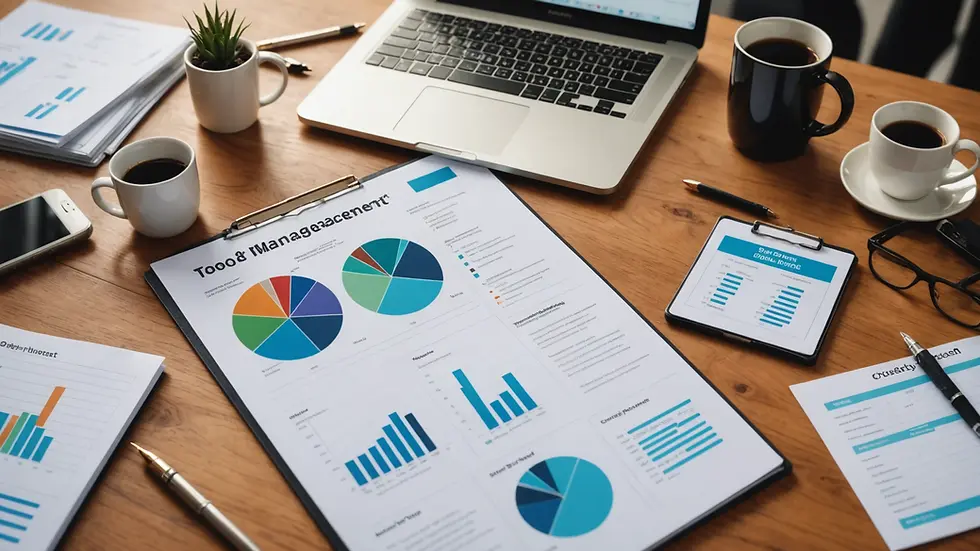
Comments