Ensuring Resilience: Integrating ISO 9001 with Business Continuity Plans for Uninterrupted Operations
- islam Arid
- Apr 30
- 5 min read
In today's rapidly changing business environment, organizational resilience is more important than ever. Disruptions from natural disasters, economic shifts, or sudden operational challenges can hurt a company's ability to deliver products and services. As businesses strive to improve operational capabilities, integrating ISO 9001 with strong business continuity plans is crucial. This combination not only strengthens an organization's processes but also ensures compliance with quality standards and encourages continuous improvement.
When organizations understand how ISO 9001, a globally recognized standard for Quality Management Systems (QMS), aligns with business continuity practices, they can build a powerful framework for risk management and operational strength.
The Significance of ISO 9001
ISO 9001 outlines the criteria for a quality management system and is the only standard in its family that can be certified. This standard relies on key quality management principles, including a strong focus on customer needs, the participation of top management, a process-oriented approach, and ongoing improvement.
Implementing ISO 9001 can help organizations to:
Streamline Processes: By improving overall performance, organizations can deliver high-quality products or services consistently.
Boost Customer Satisfaction: Certification can enhance trust and confidence among customers, essential for sustaining operations in tough times. For instance, studies show that companies with ISO 9001 certification see up to a 20% increase in customer satisfaction on average.
Understanding Business Continuity
Business continuity involves the strategies and processes organizations use to continue operations in the face of disruptions. This planning includes preparing for various scenarios, such as natural disasters, technology failures, and unexpected incidents.
A solid business continuity plan enables organizations to:
Identify Potential Risks: Recognizing vulnerabilities is vital for developing effective strategies to mitigate them.
Safeguard the Reputation: A well-prepared organization can protect its reputation and maintain stakeholder interests during crises. For example, organizations that fail to plan for business continuity can experience up to a 60% drop in customer trust following a major disruption.
Why Integrate ISO 9001 with Business Continuity Plans?
Integrating ISO 9001 with business continuity planning creates a relationship that boosts operational resilience. This alignment allows companies to leverage the strengths of both frameworks, leading to various benefits.
Enhanced Risk Management: ISO 9001's focus on risk management aligns with business continuity planning goals. By effectively identifying and addressing risks, organizations can reduce the chances of severe consequences during disruptions.
Consistent Quality Control: By merging quality goals with continuity strategies, organizations can maintain standards even during unexpected disruptions. Preserving product and service quality is crucial for keeping customers satisfied.
Efficient Processes: ISO 9001's process approach allows businesses to make their continuity procedures more effective and speedy. This efficiency is paramount when rolling out immediate responses to crises.
Clear Performance Metrics: Integrating performance monitoring and evaluation from both ISO 9001 and business continuity planning helps to set measurable standards for resilience and responsiveness.
Targeted Training Programs: Combining ISO 9001 requirements with business continuity plans simplifies the development of training programs, preparing employees to handle quality management and continuity challenges proficiently.
Steps for Integration
To integrate ISO 9001 with business continuity plans effectively, organizations can follow these steps:
1. Assess Current ISO 9001 Compliance
Evaluate your existing ISO 9001 implementation and identify areas needing improvement. Use internal audits to assess compliance with quality criteria and locate any nonconformities.
2. Identify Key Business Processes
Map out and prioritize the critical business processes essential to operations. This step helps determine which processes need protective measures during disruptions.
3. Conduct a Business Impact Analysis
Perform a business impact analysis (BIA) to identify risks to key processes. This analysis should gauge how disruptions might affect product quality, customer satisfaction, and overall operations.
4. Develop Business Continuity Procedures
Draft detailed business continuity procedures that include elements from the ISO 9001 framework. Make sure these procedures cover quality control, corrective actions, and performance metrics.
5. Train and Educate Employees
Create training programs to educate employees on both ISO 9001 principles and business continuity measures. This awareness enhances their understanding of quality management and their roles in maintaining resilience.
6. Monitor and Review
Regularly assess the integrated system’s effectiveness. Conduct management reviews and internal audits to ensure compliance with ISO 9001 standards and the practicality of business continuity plans.
Operational Benefits of Integration
When organizations integrate ISO 9001 and business continuity plans effectively, they can experience many operational benefits:
Higher Employee Engagement: A unified approach fosters a positive corporate culture. Employees feel more connected when they understand their contributions to resilience.
Optimized Resource Use: Aligning quality processes with continuity planning ensures critical areas receive necessary attention and investment. This can lead to up to a 30% increase in efficiency.
Quicker Recovery Times: An integrated approach reduces downtime significantly. Defined procedures and established roles lead to faster responses and limit disruption impact.
Stronger Trust Among Stakeholders: A commitment to quality and continuity cultivates trust with customers, suppliers, and partners, enhancing long-term relationships. A survey indicated that 78% of businesses reported enhanced supplier trust after integrating these frameworks.
Improved Compliance: Adhering to ISO 9001 standards via integrated business continuity plans helps avoid legal challenges, ensuring uninterrupted operations.
Case Studies in Successful Integration
Case Study 1: Manufacturing Industry
A manufacturing company frequently struggled with supply chain disruptions. By integrating ISO 9001 into its business continuity planning, the organization identified high-risk suppliers and implemented improvement strategies. As a result, they achieved a 20% increase in operational efficiency and significantly reduced downtime during disruptions.
Case Study 2: Healthcare Sector
A healthcare provider implemented ISO 9001 principles into its business continuity strategy, focusing on quality objectives. They created a feedback loop to maintain quality control, ensuring compliance with regulations while keeping operational capabilities intact during emergencies. Surveys showed patient care quality improved, leading to a 15% increase in patient satisfaction rates.
Addressing Common Challenges
Integrating ISO 9001 and business continuity presents several challenges. Here’s how to mitigate them:
Resistance to Change: Employees might resist new processes. Leadership should communicate integration benefits and involve employees in the transition journey to ease concerns.
Resource Limitations: Limited resources may slow integration efforts. Organizations should focus on critical areas and consider phased approaches for implementing changes.
Technical Complexity: ISO 9001’s requirements can feel daunting. Hiring consultants for training and support can ease the process and promote better understanding.
Future Trends in Quality Management and Business Continuity
As organizations move forward, several trends will likely influence the integration of ISO 9001 and business continuity:
Digital Transformation: The rise of digital technologies will enhance data collection, analysis, and reporting, proving invaluable for quality management and continuity planning.
Artificial Intelligence and Automation: AI can streamline compliance audits and risk assessments. Automation can handle routine monitoring, freeing up resources for more strategic tasks.
Sustainable Practices: More companies are focusing on sustainability. Merging sustainability with quality management practices can create resilient and responsible operations.
Global Standards Alignment: As markets become increasingly interconnected, organizations will need to ensure quality and continuity standards align internationally. Collaborating and sharing best practices across borders will facilitate this goal.
The Path Forward
Integrating ISO 9001 with business continuity plans is a vital step for organizations aiming to enhance their resilience during disruptions. This integration fortifies quality management systems and provides a robust framework for risk mitigation and organizational continuity.
Focusing on risk management, quality assurance, and continuous improvement allows businesses to nurture a culture that delivers exceptional performance and customer satisfaction.
Ultimately, proactive alignment of ISO 9001 standards with strategic business continuity planning empowers organizations to not only survive but thrive in an unpredictable world.
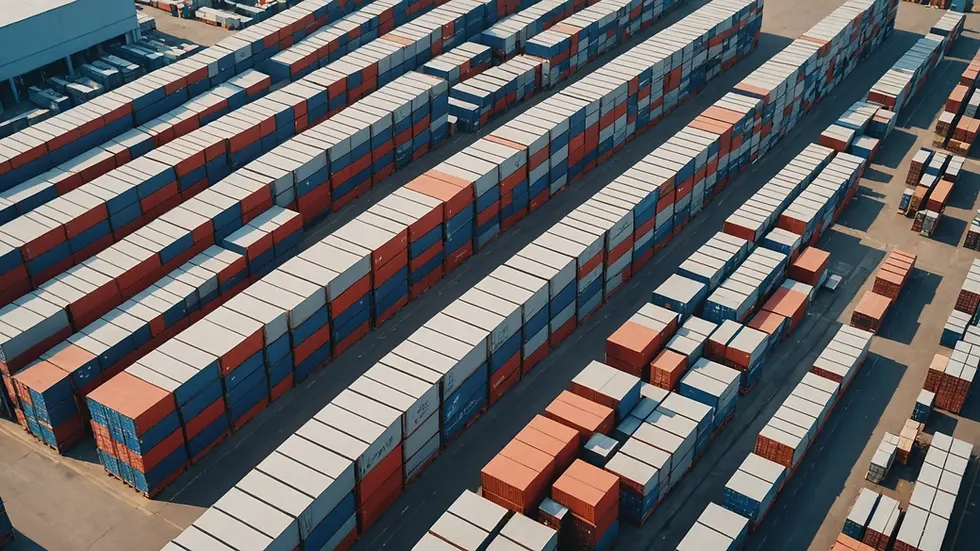
Comments