Tailoring ISO 9001: Expert Strategies for Healthcare, Manufacturing, IT, and More
- islam Arid
- Apr 30
- 4 min read
Engaging Overview
In a world where quality drives success, ISO 9001 stands out as a key standard for optimizing operational performance and ensuring customer satisfaction. As more organizations globally embrace ISO 9001, tailoring its principles to fit varied industries becomes crucial. The different nuances and challenges of sectors like healthcare, manufacturing, and IT mean that a one-size-fits-all approach is insufficient. In this article, we will explore practical strategies for customizing ISO 9001 implementation to meet industry-specific needs, enhancing quality management practices.
Understanding ISO 9001 and Its Importance
ISO 9001 provides essential guidelines to help organizations satisfy customer and regulatory expectations while promoting ongoing improvement. This standard advocates for a process-driven approach that fosters efficiency and quality throughout the organization.
When successfully implemented, ISO 9001 can lead to remarkable benefits such as a 20% reduction in operational errors, enhanced risk management, and improved customer satisfaction scores, often exceeding 90%. Yet, defining “effective implementation” varies widely across industries, making targeted strategies essential.
Tailoring ISO 9001 for the Healthcare Industry
In healthcare, quality assurance is vital—it's not just about compliance; it's about patient life. Therefore, implementing ISO 9001 requires a thoughtful strategy.
Key Strategies for Healthcare Implementation
Focus on Patient Safety and Quality Assurance:
In this sector, the primary measure is patient safety. Tailoring ISO 9001 involves developing detailed procedures for monitoring adverse events. For example, hospitals can implement reporting systems that track medication errors and patient feedback, using these insights to improve care quality. A recent study showed that hospitals using structured feedback systems reduced medication errors by 30%.
Document Control:
Managing a large volume of documentation is essential in healthcare. Implement robust document control to enhance compliance and ensure staff access the latest protocols. For instance, digital record systems that incorporate real-time updates can significantly decrease the chance of using outdated procedures, leading to better patient outcomes.
Risk Management:
Effective risk management is critical in healthcare. The ISO 9001 standard encourages organizations to identify hazards proactively. Conducting quarterly internal audits can reveal compliance gaps and potential safety risks. Tracking these findings against performance metrics enables timely adjustments that enhance patient safety.
Engagement and Communication:
A culture of quality in healthcare hinges on open communication among multidisciplinary teams. Regular management reviews can be structured to solicit feedback from all staff, leading to a more engaged workforce. Implementing quarterly quality improvement initiatives can foster accountability and promote shared learning.
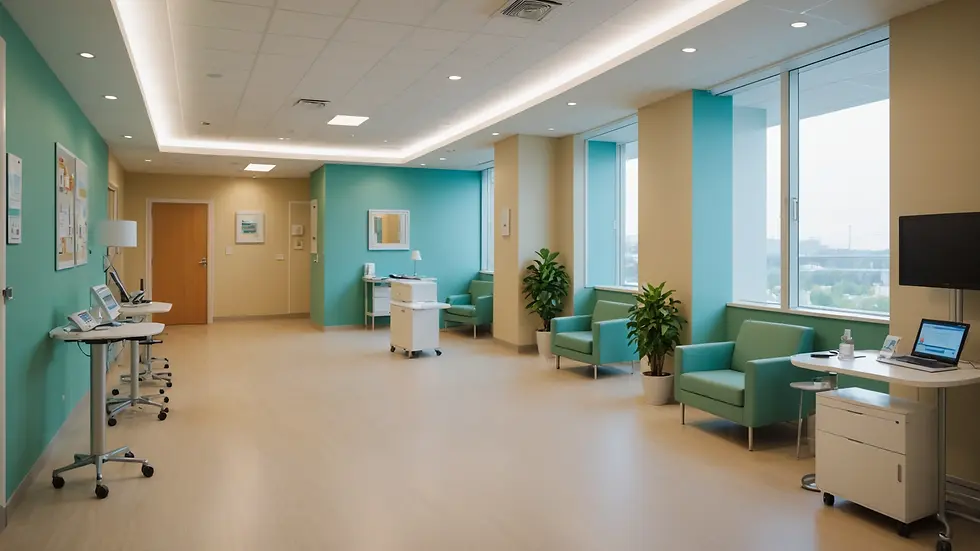
Tailoring ISO 9001 for the Manufacturing Industry
For the manufacturing sector, operational efficiency is key. ISO 9001 implementation can streamline processes and enhance product quality.
Key Strategies for Manufacturing Implementation
Streamlining Production Processes:
Documenting ISO 9001 procedures meticulously can drastically improve efficiency. Integrate Lean Management principles to reduce waste and maximize productivity. Companies that adopt these practices can achieve production cost reductions of up to 15% and improve delivery times.
Supplier Quality Management:
The quality of raw materials directly affects outcomes in manufacturing. Tailoring supplier evaluations to ensure compliance with quality standards is critical. Establish a supplier audit program that includes evaluating performance metrics, which can lead to improved consistency in product quality.
Performance Metrics and Data Analysis:
Create actionable performance metrics to monitor processes. Utilizing data analytics not only supports informed decision-making but helps identify improvement areas. For example, analyzing production downtime data can lead to operational changes that shorten lead times by 20%.
Training and Development:
Training programs should align with ISO 9001 principles, emphasizing quality assurance. Regular workshops focused on best practices can enhance skill sets and keep employees updated on compliance. Ensuring a trained workforce leads to fewer defects and higher customer satisfaction.
Tailoring ISO 9001 for the IT Industry
In the fast-moving IT industry, maintaining quality and agility is essential. Adapting ISO 9001 requires an approach that facilitates quick changes without sacrificing compliance.
Key Strategies for IT Implementation
Agile Quality Management:
Incorporate Agile methodologies into ISO 9001 frameworks. This approach allows teams to iterate rapidly while ensuring compliance through structured feedback loops. For instance, implementing bi-weekly reviews during software development can enhance product adaptability and responsiveness, improving end-user satisfaction by over 25%.
Document Control and Version Control:
An effective document control system is fundamental to IT. Adopting digital management systems ensures that everyone works from the latest version of documents, reducing errors and improving efficiency. Version control mandates detailed tracking of changes, safeguarding against outdated procedures.
Internal Audits and Compliance:
Conduct regular internal audits focusing on both ISO 9001 and relevant IT standards like ISO/IEC 27001. Use findings to inform team training and drive process enhancements. By scheduling audits quarterly, organizations can stay ahead in compliance and continuously refine their processes.
Customer Satisfaction Focus:
In IT, aligning quality management with customer experience is vital. Create channels for collecting real-time user feedback and integrate this into your ISO 9001 procedures. Regularly analyzing this feedback can guide product enhancements, driving higher satisfaction levels.
Summing It Up
ISO 9001 provides a robust structure for organizations to improve their quality management systems. However, success lies in the ability to adapt the standard to the specific needs of different industries.
In healthcare, priorities shift toward patient safety and compliance. For manufacturing, the focus is on process optimization and supplier quality. In IT, agility and user experience take the lead.
By implementing targeted strategies for tailoring ISO 9001, organizations can achieve compliance while fostering a culture that advocates for continuous improvement. This commitment to quality management should be ingrained within every facet of an organization's culture, allowing businesses to not only meet but exceed customer expectations.
Comments