Enhancing ISO 9001 Nonconformities Resolution Through Root Cause Analysis Techniques
- islam Arid
- Apr 7
- 5 min read
In today's competitive business landscape, quality management is non-negotiable. ISO 9001 helps organizations establish strong systems for continuous improvement and customer satisfaction. However, challenges arise when nonconformities—deviations from established quality requirements—occur. Identifying and addressing the root causes of these nonconformities is vital for organizations aiming to enhance their quality management systems effectively.
This blog post explores practical root cause analysis (RCA) techniques that organizations can utilize to identify the underlying causes of nonconformities in their ISO 9001 initiatives. By incorporating these techniques into their corrective actions, businesses can nurture a culture of ongoing improvement and diligently maintain their ISO 9001 certification.
Understanding Nonconformities in ISO 9001
Nonconformities are critical indicators within ISO 9001’s quality management framework. These deviations stem from numerous sources like process breakdowns, insufficient training, or lack of proper documentation. Accurate identification and documentation of nonconformities are crucial for compliance and overall efficiency.
Nonconformities can be categorized into major and minor types. Major nonconformities often signify significant failures in critical areas, necessitating immediate corrective measures. In contrast, minor nonconformities may not pose imminent risks but still require prompt action to prevent escalation. For example, a major nonconformity could involve a failure in quality checks that leads to product recalls, while a minor issue might be missing paperwork that could cause delays in certification processes.
The Role of Root Cause Analysis
Root Cause Analysis is essential for revealing the fundamental reasons behind nonconformities. Rather than merely addressing symptoms, organizations need to focus on why a problem occurred. By doing so, they can develop long-term corrective actions that mitigate the risk of recurrence. This approach supports the continuous improvement philosophy inherent in ISO 9001, emphasizing an organization’s commitment to quality.
With various root cause analysis techniques available, organizations can choose methods tailored to their unique challenges, ensuring a robust approach to quality management.
Common Root Cause Analysis Techniques
1. The 5 Whys Technique
The 5 Whys technique is a simple yet effective method for uncovering the root cause of a problem through repetitive questioning. By asking "why" five times, organizations can dig deeper into the issue.
Example Process:
Identify the problem: A machine broke down during production.
Ask why: Why did it break down? Because it overheated.
Continue questioning: Why did it overheat? Because the cooling system failed. Why did the cooling system fail? Because it wasn’t maintained. Why was it not maintained? Because there is no maintenance schedule. Why is there no schedule? Because responsibility was unclear.
This technique emphasizes both problem definition and a focus on deeper issues, highlighting the necessity of accountability in maintenance processes.
2. Fishbone Diagram (Ishikawa)
The Fishbone Diagram, or Ishikawa diagram, provides a visual method for brainstorming potential causes of a problem in a structured manner. This technique enables teams to explore various factors contributing to a specific nonconformity.
Steps to Create a Fishbone Diagram:
Define the problem: Label the head of the fish with the specific issue (e.g., product defects).
Identify categories: Create main branches for categories such as People, Processes, Equipment, Materials, and Environment.
Brainstorm causes: Collaboratively list potential causes under each category. For instance, under People, you might list inadequate training, while under Process, you might cite unclear procedures.
This collaborative approach enhances team engagement and broadens perspectives on root causes.
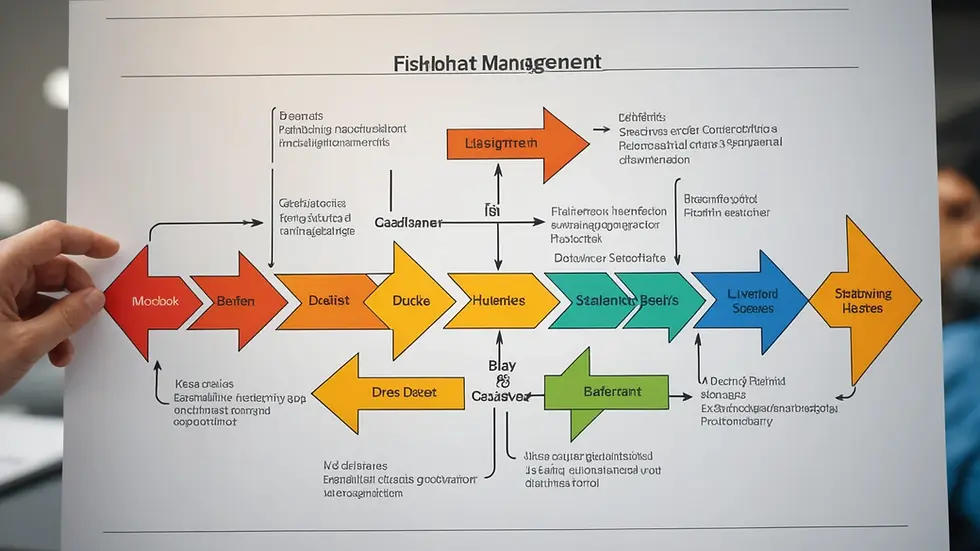
3. Pareto Analysis
Following the 80/20 rule, Pareto Analysis illustrates that about 80% of issues stem from 20% of the root causes. By prioritizing these significant issues, organizations can direct resources where they will have the most impact.
Example Steps:
Collect data: Gather information on nonconformities, categorizing occurrences by type.
Create a chart: Develop a Pareto chart that visually illustrates the frequency of nonconformities.
Analyze: Determine which issues occur most frequently, guiding corrective actions. For instance, if defects in one product line account for 70% of returns, prioritizing that line for quality improvements is beneficial.
This technique allows organizations to focus efforts on areas with the highest potential for improvement.
4. Failure Mode and Effects Analysis (FMEA)
FMEA is a proactive method that identifies potential failures before they happen by assessing their severity, occurrence, and detectability. This analysis helps organizations prioritize corrective actions effectively.
Example Process:
Identify the process: Define the scope of what is being analyzed, such as a manufacturing process.
List failure modes: Identify possible failures and their impacts. For instance, a failure mode could be a defective component.
Rate each failure: Assess severity, likelihood, and detectability, assigning scores. A critical defect might get a high severity rating.
Prioritize actions: Focus on addressing high-risk failure modes immediately.
Using FMEA allows organizations to anticipate problems and implement solutions to prevent nonconformities.
5. Root Cause Analysis using the 8D Method
The 8D problem-solving approach is structured and focuses on team collaboration for more complex issues. It comprises eight steps that guide teams through the analysis process.
Example Steps:
D0: Plan: Prepare for an effective problem-solving session.
D1: Team: Form a cross-functional team.
D2: Describe the problem: Clearly define the nonconformity issue.
D3: Interim containment actions: Apply short-term fixes to minimize the impact of the problem.
D4: Root cause analysis: Identify root causes through methods like the 5 Whys or Fishbone Diagram.
D5: Permanent corrective actions: Develop long-term solutions.
D6: Implement corrective actions: Execute these solutions.
D7: Prevent recurrence: Modify systems or processes to avoid reoccurrence.
D8: Congratulate the team: Celebrate successes as a team to reinforce engagement.
This method is particularly beneficial for complex problems, instilling a culture of collaboration focused on quality assurance.
Implementing Corrective Actions
Identifying root causes is only the first step; effectively implementing corrective actions is crucial in preventing future issues. Here are essential steps organizations can take:
1. Develop a Corrective Action Plan
Create a comprehensive corrective action plan detailing the steps needed to address identified root causes. This plan should specify responsibilities, timelines, and measurable goals to track progress.
2. Communicate Changes
Communicating changes effectively ensures that all relevant personnel understand the corrective actions, their rationale, and expected outcomes. Clear communication fosters accountability.
3. Train and Support Staff
Training staff on new procedures enhances compliance and strengthens the quality culture within the organization. For example, conducting workshops on proper documentation can vastly improve overall performance.
4. Monitor and Evaluate Results
Establish performance metrics to assess the results of corrective actions. Regular evaluations enable organizations to ensure that issues have been resolved and that improvements are ongoing.
5. Document Everything
Accurate documentation supports compliance with ISO 9001 and provides a detailed record of the corrective action process. This documentation is crucial during audits and can help identify future improvement areas.
Cultivating a Quality Culture
Successfully incorporating root cause analysis techniques into quality management systems requires a supportive quality culture. This culture encourages open communication, employee involvement, and a commitment to continuous improvement.
1. Encourage Employee Participation
Involve employees at all levels in quality initiatives by providing opportunities for them to share insights and experiences. Workshops and brainstorming sessions can harness collective creativity and improve nonconformity resolutions.
2. Set Clear Quality Objectives
Align quality objectives with the broader goals of the organization. Ensuring that everyone understands their role in achieving these objectives strengthens accountability and adherence to ISO 9001 standards.
3. Recognize and Reward Improvement
Acknowledging efforts toward quality initiatives creates a positive feedback loop. Celebrating achievements in quality improvements can motivate teams to pursue excellence consistently.
Reinforcing Commitment to Quality
Addressing nonconformities through root cause analysis techniques is essential in maintaining ISO 9001 compliance and enhancing operational processes. By utilizing proven methods such as the 5 Whys, Fishbone Diagram, Pareto Analysis, FMEA, and the 8D Method, organizations can identify key issues and implement corrective actions effectively.
Fostering a culture that emphasizes quality, accountability, and continuous improvement is vital in retaining ISO 9001 certification while improving overall operations. When nonconformities arise, tackling them with a comprehensive root cause analysis sets the stage for excellence, boosting customer satisfaction and overall business success.
By making root cause analysis an integral part of quality management, organizations can strengthen their commitment to delivering the best in every aspect of their operations.
Comments