How to Turn ISO 9001 Audit Results into Effective Quality Improvement Strategies
- islam Arid
- Apr 7
- 5 min read
Quality management is essential for any organization that wants to improve its products and services. ISO 9001 is a well-known standard that helps businesses meet international quality management expectations. Regular audits are a key part of this process, helping to assess compliance and find areas needing attention. This blog post outlines actionable steps to use ISO 9001 audit results effectively to promote continuous improvement and maintain high quality.
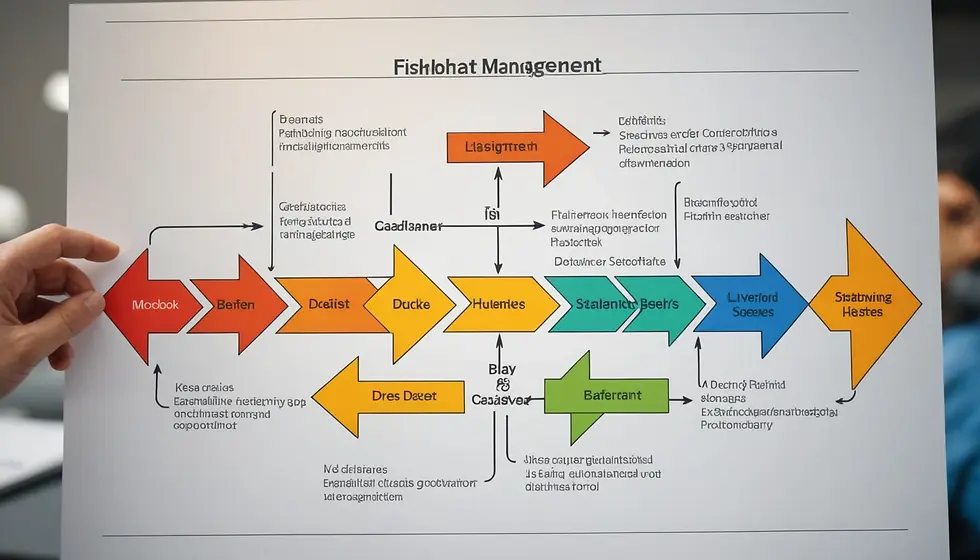
Understanding ISO 9001 Audits
ISO 9001 audits are thorough evaluations of a company’s quality management system (QMS). They check compliance with the ISO 9001 standard, ensuring that the organization follows established procedures. Audits can be either internal or external and typically focus on aspects like documentation, process efficiency, and compliance with quality objectives.
For example, organizations might find that 30% of their processes do not meet the established standards during an internal audit, which opens pathways for essential improvements.
The Importance of Quality Management Systems
In today’s competitive business climate, understanding quality management systems (QMS) is critical. A well-functioning QMS using ISO 9001 strategies can:
Increase customer satisfaction by up to 20%
Streamline processes, potentially cutting operational costs by 15%
Decrease the likelihood of errors in production to less than 2%
Mitigate risks associated with quality failures
Cultivate a culture focused on ongoing improvement
Integrating effective quality management practices not only ensures compliance with ISO 9001 but also strengthens an organization’s standing in the market.
Conducting an Effective ISO 9001 Audit
A successful ISO 9001 audit depends on detailed planning and execution. Follow these steps to ensure the audit process is productive:
1. Preparation and Planning
Prepare thoroughly before the audit. Define the audit scope, pinpoint relevant processes, and ensure all essential documentation is ready. Check that your audit tools, like checklists, are current and tailored to the latest version of ISO 9001.
2. Conducting the Audit
During the audit, auditors must remain impartial and gather evidence through direct observations and interviews. They should assess the extent to which processes align with ISO 9001 standards and whether quality objectives are effectively implemented.
3. Documenting Findings
Documenting findings after the audit is critical. The report should detail strengths and weaknesses, along with any nonconformities. A thorough audit report provides a solid basis for further corrective actions and improvements.
Turning Audit Results into Actionable Steps
Turning audit findings into actionable strategies is crucial for continuous improvement. Here’s how to ensure effective outcomes from audit results:
1. Analyze Nonconformities
After documenting findings, analyze any nonconformities identified. Determine the root causes and assess the impact on quality objectives. For instance, if customer complaints rose by 25% in a particular area, understanding the underlying issues can guide meaningful corrections.
2. Develop a Corrective Action Plan
Once root causes are found, create a detailed corrective action plan. This should include specific steps to address nonconformities. Pay attention to these key aspects:
Ownership: Assign clear responsibilities for each action.
Timeline: Set implementation deadlines.
Resources: Identify resources required to support these actions.
3. Implement Changes
After finalizing the corrective action plan, implement the changes. Inform and train all relevant stakeholders to ensure everyone understands the updates. This may also involve revising ISO 9001 documentation, which is essential for ongoing compliance.
4. Monitor and Evaluate Effectiveness
Monitor the effectiveness of corrective actions continuously. Use performance metrics to measure improvements over time and check whether the desired results are being achieved.
Establishing a Culture of Continuous Improvement
To maintain the benefits gained from ISO 9001 audits, fostering a culture of continuous improvement is essential. Engage all employees in the quality management process so everyone understands their role in achieving success.
1. Encourage Employee Involvement
Promote a work environment where employees feel empowered to contribute to quality improvements. Conduct regular training sessions, workshops, or team meetings focused on quality goals. For instance, organizations that involve employees in decision-making often see a productivity increase of around 15%.
2. Regular Management Reviews
Establish regular management reviews to validate adherence to quality standards. These reviews can help identify necessary adjustments, ensuring continuous alignment with the organization's goals.
3. Streamline Communication
Create open communication channels between employees, teams, and management. This promotes collaboration, making quality improvements a shared objective. Using digital tools to circulate audit results and progress is an effective way to keep everyone in the loop.
Risk Management in Quality Improvement
An effective quality improvement strategy should include a strong approach to risk management. Identifying potential risks is crucial for addressing issues before they arise. Here are best practices for integrating risk management into your ISO 9001 strategies:
1. Identify Risks
Regularly conduct assessments to identify risks that may impact quality objectives. Risks could arise from suppliers, internal processes, or employee-related factors.
2. Develop Mitigation Plans
Once risks are identified, devise strategies to mitigate them. For example, diversifying suppliers can reduce dependence on a single source and the risks associated with it.
3. Monitor Risks Continually
Establish ongoing risk assessment practices to quickly identify and resolve new threats. This aligns with the continuous improvement mindset, as organizations must adapt to changing environments.
Utilizing Performance Metrics for Quality Improvement
Performance metrics are essential for gauging the effectiveness of the ISO 9001 framework. By evaluating this data, organizations can uncover trends and drive improvements. Here’s how to maximize the use of performance metrics:
1. Define Key Performance Indicators (KPIs)
Choose relevant KPIs tied to quality objectives. These can include customer satisfaction ratings, defect rates, or process efficiency scores.
2. Analyze Data Regularly
Set a routine for analyzing performance metrics. Regular reviews can help catch issues early, allowing for timely corrective actions and adjustments.
3. Implement Adjustments Based on Insights
Use data to inform decisions and refine processes. Being flexible and adapting to findings enhances the potential for quality improvement.
Training and Development for Quality Culture
Investing in training and development is crucial for fostering a quality-oriented culture. Training improves skill levels and ensures all employees are familiar with the ISO 9001 framework and its significance. Here are strategies for effective training programs:
1. Create Customized Training Programs
Design training sessions tailored to the unique needs of each department. Ensure that every employee understands how to align with ISO 9001 standards.
2. Promote Continuous Learning
Encourage an environment where employees can consistently enhance their skills in quality management. Consider offering workshops, seminars, and online resources to support ongoing education.
3. Evaluate Training Effectiveness
Regularly monitor the impact of training programs through employee feedback and performance metrics. Adjusting programs based on this information keeps training relevant and aligned with quality objectives.
Final Thoughts
Use insights from ISO 9001 audits to foster continuous improvement and establish a culture of quality within your organization. Analyzing nonconformities, implementing corrective actions, and managing risks will lead to sustainable improvements.
By committing to regular training and performance measurement, organizations can stay focused on quality. Remember, translating audit results into effective strategies is not only about meeting standards; it’s about enhancing customer satisfaction and solidifying your organization’s position as a trustworthy leader in the industry.
Quality improvement is an ongoing journey. Embracing lessons from ISO 9001 audits will lead to a stronger commitment to excellence and a more resilient, agile organization ready to face future challenges.
Comments