Driving Continual Improvement: Applying the PDCA Cycle in ISO 9001 Quality Management
- islam Arid
- Apr 30
- 5 min read
In today's fast-paced business environment, quality management is essential for success. Continuous improvement allows organizations to refine their processes, boost customer satisfaction, and build a culture where quality is a priority. One of the most effective ways to achieve this is through the PDCA Cycle—Plan-Do-Check-Act.
The PDCA Cycle is a crucial framework for organizations working towards ISO 9001 certification. This blog post will break down each step of the PDCA cycle and provide practical examples to help you implement it effectively in your ISO 9001 Quality Management System (QMS).
Understanding the PDCA Cycle
The PDCA Cycle, created by Dr. W. Edwards Deming, is a simple, four-step management method that promotes continuous improvement in processes, products, or services.
Plan
The first step in the PDCA Cycle is Plan. This phase is about spotting opportunities for improvement within your processes. For ISO 9001 implementation, organizations need to define their quality objectives and create a quality policy that aligns with these objectives.
Identify Objectives: Define what you aim to achieve in quality management. For example, setting a target to reduce customer complaints by 10% in the next six months is a clear, measurable objective.
Analyze Current Processes: Evaluate your existing processes to see how well they meet your objectives. Using tools like SWOT analysis can reveal strengths and weaknesses. For instance, if you find that a lengthy product return process leads to dissatisfaction, it’s a clear area for improvement.
Develop Strategies: Create action plans to meet your quality goals. This could include allocating budget for training or setting up a timeline to streamline processes, ensuring everyone knows their responsibilities.
Document Control: Make sure to document your plans and processes carefully. Strong documentation is key for ISO 9001 compliance, as it builds a foundation for transparency and accountability.
A structured plan paves the way for success in the PDCA cycle.
Do
In the Do phase, organizations put their strategies into action.
Execute the Plan: Implement the action plans developed in the planning phase. Clear communication among team members is vital. For example, if a new procedure is introduced to reduce errors in product assembly, ensure all staff understand their roles in this process.
Training and Development: Invest in training for your teams. For instance, if you're rolling out a new quality control approach, providing hands-on training can help staff adapt and improve their skills.
Collect Data: Monitor the effectiveness of the implemented changes by collecting data. You might track performance metrics, such as defect rates, to see if they improve after changes are made.
This phase is all about executing the planned actions effectively, setting the stage for evaluation.
Check
The Check phase focuses on reviewing the outcomes of the actions taken.
Evaluate Performance: Use the data gathered to assess how well your processes are performing. This could involve measuring Key Performance Indicators (KPIs) such as on-time delivery rates, which can provide a quantifiable measure of improvement.
Identify Nonconformities: Look for discrepancies between your outcomes and quality goals. For instance, if customer surveys show a satisfaction rate below 80%, investigate what might have caused this.
Management Review: Conduct management reviews to assess how well the quality management system is functioning and how it aligns with business goals. Discuss findings and necessary adjustments with your team.
This phase plays a critical role in identifying areas that need refinement as it informs future actions.
Act
The final phase of the PDCA Cycle is to Act. This step involves making changes based on your evaluations.
Implement Corrective Actions: Address any issues by taking corrective actions. For example, if certain quality checks are found lacking, modify the procedure and provide additional training where needed.
Standardize Successful Processes: If changes lead to successful outcomes, make them a standard practice. Update all relevant documentation to reflect these new processes.
Foster a Quality Culture: Promote a culture that values continuous improvement. Encourage staff to suggest improvements and reward initiatives that lead to better quality.
Review: The cycle doesn’t end here. Regularly revisit the PDCA cycle to initiate new planning activities that reflect changes in your business environment.
By continuously cycling through these stages, organizations can maintain a culture of excellence and adaptability.
Applying the PDCA Cycle to ISO 9001 Implementation
Implementing the PDCA Cycle within ISO 9001 is a strategic process. Here's how you can align each step with ISO requirements.
Integrating PDCA with ISO 9001 Requirements
Leadership Commitment: Strong support from leadership is crucial for effective ISO 9001 implementation. Leaders must actively participate in the planning process and provide resources.
Customer Focus: Align your objectives with customer needs. For example, gather customer feedback to better understand their requirements during the planning phase.
Risk-Based Thinking: Include risk management in each phase of the PDCA cycle. By identifying risks when planning, organizations can prevent potential issues.
Performance Metrics: Set specific KPIs to link with quality objectives, which helps assess progress during the "Check" phase.
Best Practices for Each PDCA Step
Best Practices for Planning
Engage Stakeholders: Involve different stakeholders in planning to gather varied insights and gain support.
Utilize Data: Use historical data and customer feedback to inform your planning process accurately.
Set Realistic Objectives: Make sure quality objectives are SMART (Specific, Measurable, Achievable, Relevant, Time-bound) to facilitate effective evaluation.
Best Practices for Doing
Communicate Clearly: Keep communication open with all team members involved in implementation to avoid misunderstandings.
Use Quality Tools: Implement ISO 9001 tools such as process flowcharts to aid in execution.
Monitor Progress: Regularly check in on the project's status to ensure everyone stays on track and address any issues promptly.
Best Practices for Checking
Data Analysis Techniques: Use statistical tools to analyze the collected data thoroughly.
Gather Feedback: Collect feedback from employees involved in the process to identify any challenges they face.
Document Findings: Maintain records of observations to assist in the review process.
Best Practices for Acting
Conduct Root Cause Analysis: Identify the root causes of nonconformities to address issues effectively.
Communicate Changes: Inform all employees about changes before codifying new processes into standard practice.
Promote Learning: Encourage a learning culture where feedback from both successes and failures is valued.
PDCA Cycle Tools for ISO 9001 Implementation
Leverage specific tools to bolster your PDCA Cycle efforts during ISO 9001 implementation:
Process Mapping Software: Use software to visualize workflows and identify inefficiencies.
Document Control Systems: Implement systems for organizing and versioning quality documents.
Performance Measurement Tools: These tools track KPIs, helping you assess progress against objectives.
Training Management Systems: Such systems ensure all employees receive training on the required quality standards.
Feedback Tools: Utilize tools to collect customer feedback, allowing you to address issues and improve service.
Common Challenges and Solutions
While implementing the PDCA Cycle, organizations may face challenges. Here are some common issues with potential solutions:
Resistance to Change: Employees may resist changes to established processes. Involving them early in discussions can help build acceptance.
Insufficient Data: If there isn't enough data for analysis, ensure a robust data collection process is in place during the planning phase.
Lack of Management Support: Without leadership backing, initiatives can struggle. Regular updates to management about progress and importance can foster their involvement.
By anticipating challenges and crafting strategic solutions, the PDCA cycle can be successfully implemented in your ISO 9001 quality management system.
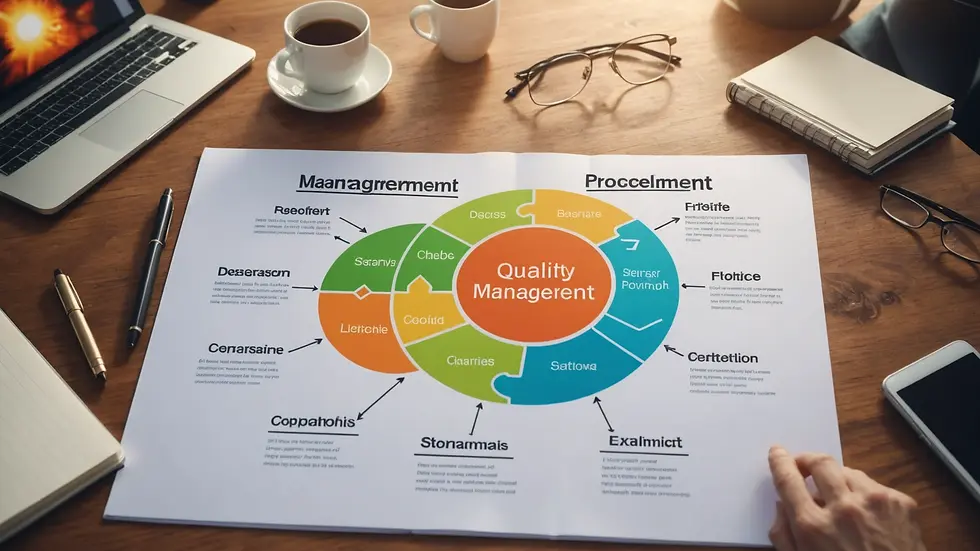
Embracing Continuous Improvement
The PDCA Cycle is essential for any organization pursuing continuous improvement in quality management under ISO 9001. Knowing how to apply each stage of this cycle equips businesses to systematically identify, implement, evaluate, and refine their processes.
As organizations adopt the PDCA cycle, they foster a quality culture that promotes ongoing enhancement. By integrating this approach into all aspects of their operations, they not only prepare for successful ISO 9001 certification but also position themselves for long-term growth.
By committing to the principles of the PDCA Cycle, leaders can steer their organizations towards not just compliance with ISO standards, but excellence in quality and performance.
Comments