Tailoring ISO 9001: Effective Strategies for SMEs
- islam Arid
- Apr 30
- 4 min read
For small and medium enterprises (SMEs), adopting Quality Management Systems (QMS) like ISO 9001 may initially seem overwhelming. Yet, with the right strategies, implementing ISO 9001 can be straightforward and beneficial. This blog post explores methods that allow SMEs to efficiently integrate ISO 9001 into their operations, helping them comply with quality standards while enhancing their business processes.
Understanding ISO 9001
ISO 9001 is a globally recognized standard that sets out the criteria for a quality management system. It helps organizations consistently meet customer expectations and regulatory requirements, boosting customer satisfaction.
The standard provides a structured framework for process management and performance improvement. It emphasizes key concepts such as process enhancement, risk management, and continuous customer satisfaction.
For SMEs, adopting ISO 9001 is not just about achieving certification. It’s about infusing quality management principles in daily operations to build a culture of continuous improvement. In fact, businesses with ISO 9001 certification often improve operational efficiency by an average of 20%.
Why ISO 9001 Matters for SMEs
Obtaining ISO 9001 certification brings notable advantages to SMEs.
Enhanced Credibility: It boosts a business's reputation, making it easier to secure contracts, particularly against larger competitors.
Cost Savings: By identifying process inefficiencies, companies can reduce waste, leading to savings of up to 30% in operational costs.
Increased Customer Satisfaction: Improved quality management systems can lead to higher customer satisfaction rates, directly affecting loyalty and repeat business.
Employee Engagement: An effective QMS fosters an engaged workforce, improving retention by as much as 40%.
Streamlined Documentation: ISO 9001 promotes better organization of records, reducing time spent on administrative tasks.
Key Challenges for SMEs
Despite the advantages, SMEs face specific challenges during ISO 9001 implementation.
Complex Requirements: The detailed requirements of ISO 9001 can be daunting for smaller teams.
Resource Constraints: Limited budgets and personnel can impede the effective adoption of ISO 9001.
Lack of Dedicated Teams: Many SMEs do not have dedicated quality management personnel, making compliance challenging.
Immediate vs. Long-term Goals: The focus on daily operations often leads to neglecting quality objectives.
Tailoring ISO 9001 Implementation Strategies
To successfully implement ISO 9001, SMEs need to adjust the standard to fit their realities. Here are effective strategies to consider:
1. Start with a Quality Policy
A quality policy serves as a commitment to quality and customer satisfaction. Involve employees in its development to ensure clear communication and engagement. For example, set specific goals, such as improving product quality by 15% within a year.
2. Simplify Document Control
Document control can be simplified by using templates and standardized forms to manage paperwork. Employ user-friendly software or cloud-based solutions to keep documents organized and up-to-date without overwhelming staff.
3. Implement Process Mapping
Using process maps to visualize workflows simplifies understanding and compliance. This method allows employees to recognize inefficiencies. For instance, a company that mapped its production process identified unnecessary steps, reducing production time by 25%.
4. Focus on Training and Development
Training is crucial for implementing ISO 9001 effectively. Offer sessions on quality standards to make sure employees understand critical practices. Regular training can lead to a 50% reduction in errors reported.
5. Identify Key Performance Metrics
Establishing performance metrics helps in tracking progress. Metrics to consider might include customer feedback scores, error rates, and production efficiency. Monitoring these metrics guides continuous improvement efforts.
6. Conduct Internal Audits Regularly
Regular internal audits assess adherence to ISO 9001. Scheduling audits biannually ensures processes are followed and provides insights into areas needing improvement.
7. Emphasize Customer Feedback
Implement systems to gather and analyze customer feedback. Tools like surveys or direct communication help businesses adapt to customer needs, potentially leading to a 20% increase in client retention.
8. Foster a Quality Culture
Creating a culture focused on quality motivates employees to take ownership of their work. Management should consistently model quality practices and reward those contributing to improvements in customer satisfaction.
The Role of Management in ISO 9001
Management plays a critical role in successful ISO 9001 adoption. Leaders must commit necessary resources and actively engage in quality initiatives. Regular management reviews of quality policies and objectives ensure alignment with goals and promote continuous improvement.
Overcoming Resource Constraints
Given the limited resources of SMEs, maximizing existing capabilities while enhancing quality is vital.
1. Leverage Technology
Investing in quality management software can streamline ISO 9001 processes, such as document control and audits, saving hours of manual work each week.
2. Collaborate with Other SMEs
Networking with other SMEs can lead to sharing resources and best practices. Forming a consortium allows for shared training costs and mutual support in quality improvement initiatives.
3. Seek Expert Guidance
Hiring quality professionals or consultants can help navigate ISO 9001 complexities. While it may seem like an upfront cost, their expertise can expedite the compliance process, potentially saving money in the long run.
4. Utilize Government and Industry Resources
Look for grants, training programs, or workshops provided by governmental or industry bodies to assist in achieving ISO 9001 certification. These resources can significantly lighten the financial burden.
Characterizing a Successful ISO 9001 Implementation
A successful ISO 9001 implementation is marked by strong leadership, effective employee engagement, and a committed culture of quality. Regular review of goals and metrics ensures that organizations remain on track for improvement and compliance. Engaging employees in training, gathering feedback, and assessing supplier quality are crucial practices that drive success.
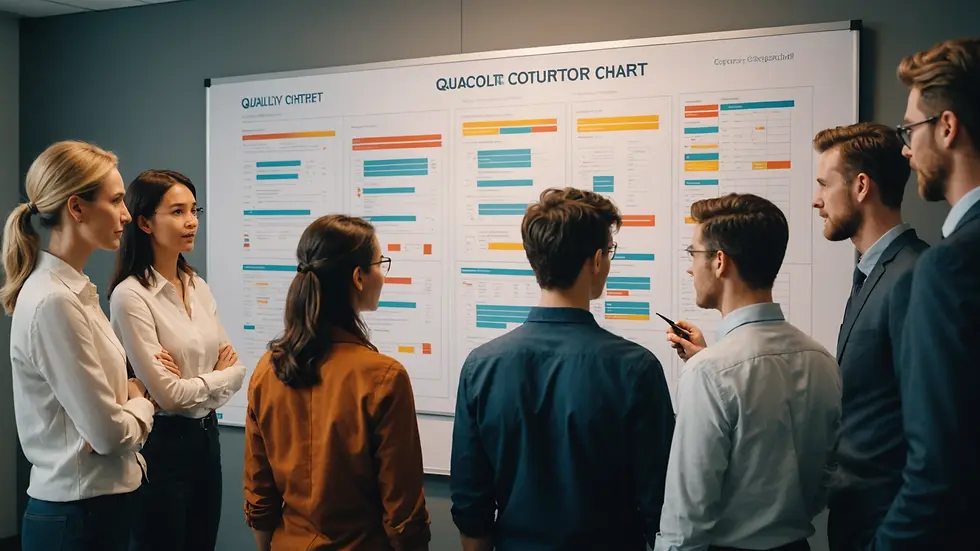
Final Thoughts
Tailoring ISO 9001 for small and medium enterprises is not only feasible but offers considerable rewards when approached thoughtfully. By breaking down the implementation process and focusing on practical steps— like utilizing technology, training, and fostering a quality culture— SMEs can achieve ISO 9001 certification without overstretching their resources. With dedicated management and active employee involvement, ISO 9001 can turn a challenging process into a valuable opportunity for growth and continuous success. Embracing these strategies will empower SMEs to create effective quality management systems that both meet ISO standards and contribute to overall business goals.
Comments