Driving Strategic Business Goals with ISO 9001 Quality Metrics: A Professional Guide to Long-Term Improvement
- islam Arid
- Apr 30
- 5 min read
Establishing quality metrics that align with strategic business goals is vital for organizations aiming for sustainable success. The ISO 9001 framework provides an effective structure that not only helps with compliance but also builds a culture of continuous improvement. In this guide, we'll discuss how organizations can implement ISO 9001 quality metrics effectively and use them to drive long-term growth.
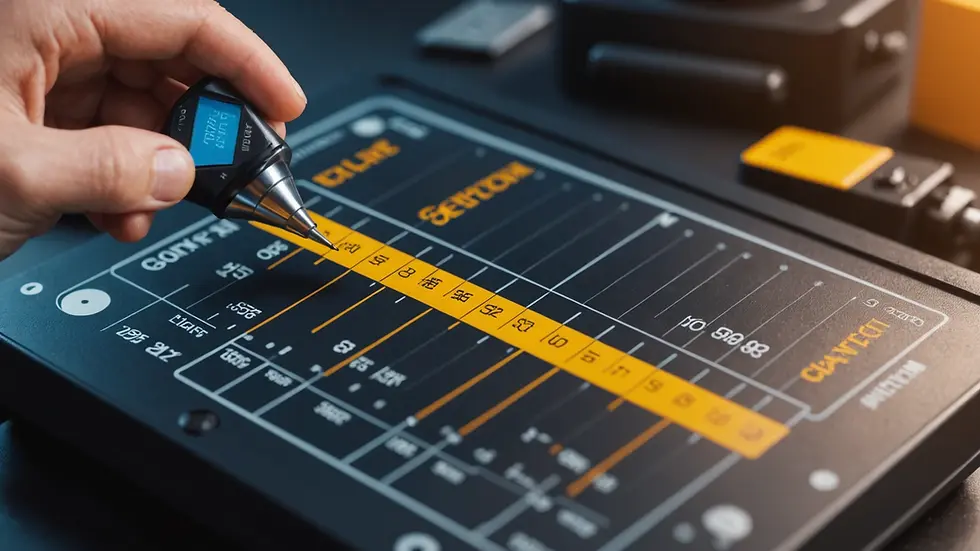
Recognizing the Value of ISO 9001
ISO 9001 is recognized as a premier standard for Quality Management Systems (QMS). It lays the groundwork for enhancing customer satisfaction, optimizing processes, and managing risks effectively.
The ISO 9001 framework highlights the importance of developing a quality policy, articulating clear quality objectives, and continuously assessing performance against these benchmarks. When quality metrics are linked to strategic goals, organizations create a strong connection that promotes ongoing improvement.
The Role of Quality Metrics in Strategic Planning
What Are Quality Metrics?
Quality metrics are quantifiable indicators used to assess the quality of processes, products, or services. They span various domains, such as customer satisfaction, process efficiency, and compliance with quality standards.
It's crucial to establish quality metrics that are relevant and can guide effective decision-making. Research shows that organizations with well-defined metrics are 20% more effective in achieving their goals.
Aligning Quality Metrics with Strategic Goals
To maximize their effectiveness, quality metrics should align closely with a company’s strategic business objectives. This includes:
Identifying key business objectives: For example, increasing annual revenue by 15%, enhancing market share by 10%, or achieving a customer retention rate of 90%.
Creating quality objectives that support these goals: For instance, reducing product defects by 25% or improving delivery times by 30%.
Ensuring that quality metrics directly measure progress toward these strategic goals.
This alignment lays the foundation for evaluating performance and identifying areas of improvement that directly impact the organization’s strategic aims.
Implementing ISO 9001 Quality Metrics
Step 1: Conducting a Gap Analysis
Organizations should start by conducting a gap analysis. This process identifies areas that need improvement by comparing current performance metrics against ISO 9001 standards.
For example, if a company currently experiences a 7% defect rate but aims for the ISO 9001 benchmark of less than 5%, the analysis helps pinpoint specific areas for action.
Step 2: Defining Quality Objectives
Quality objectives are specific, measurable goals to achieve within a set timeframe. They should be:
Specific: Clearly articulate the expectations.
Measurable: Allow tracking of progress.
Achievable: Be realistic and attainable.
Relevant: Align with business strategies.
Time-bound: Have a deadline for completion.
For instance, a company may aim to reduce customer complaints by 20% within six months. This improvement not only enhances quality but also boosts customer satisfaction, directly contributing to business objectives.
Step 3: Selecting Key Performance Indicators (KPIs)
After setting quality objectives, the next step is selecting relevant KPIs to monitor progress. Relevant KPIs might include:
Customer satisfaction ratings, which can be tracked through surveys and feedback.
Rate of nonconformities, indicating how often processes fail to meet standards.
Process efficiency metrics, like average turnaround times.
Training effectiveness, which can be measured through post-training assessments.
Using these KPIs, organizations gain valuable insights into their performance regarding quality objectives.
Step 4: Monitoring and Reporting
A strong monitoring and reporting system is vital for success. Regular reviews of KPIs help organizations spot trends, progress, and areas needing correction.
Consider holding quarterly management reviews to evaluate the effectiveness of current quality metrics, discussing strategies for further improvements. This approach keeps the organization aligned with its strategic objectives and fosters continuous enhancement.
The Influence of ISO 9001 on Long-Term Improvement
Building a Quality Culture
Adopting ISO 9001 fosters a quality-centric culture. This means more than just compliance; every employee must understand their role in ensuring quality.
Encouraging employee participation in quality discussions and providing ongoing relevant training can increase ownership of quality processes, improve morale, and lead to better overall performance.
Continuous Improvement and Audits
A key component of ISO 9001 is the concept of continuous improvement. Utilizing the Plan-Do-Check-Act (PDCA) cycle enables organizations to systematically evaluate and refine their processes.
Regular internal and external ISO 9001 audits are essential for spotting areas needing improvement. Organizations should view audit feedback as opportunities to improve processes and enhance customer satisfaction, ensuring they consistently meet quality standards.
Integrating Risk Management and Document Control
Risk Management in ISO 9001
Effective risk management is crucial for ISO 9001 compliance. Organizations need to identify potential risks related to their quality objectives and develop strategies for mitigation.
Risk assessments must be documented and regularly reviewed to ensure proactive management. This focus on risk management strengthens an organization’s resilience and prepares it for market changes.
Document Control
Proper documentation is essential for maintaining ISO 9001 compliance. Every quality procedure and policy should be documented, regularly reviewed, and updated.
Implementing a document control system enables organizations to manage revisions and track changes effectively, ensuring that all stakeholders have the latest information.
Maximizing Supplier Quality Management
Ensuring Supplier Compliance
Suppliers greatly influence the quality of a company’s final products or services. Hence, it’s critical to set quality metrics that ensure supplier compliance with ISO 9001 standards.
Regular assessments of suppliers, including performance metrics and audits, can confirm their adherence to quality policies and contribute positively to the organization’s quality aims.
Strengthening Supplier Relationships
Long-term relationships with quality suppliers can lead to greater efficiency and reliability. Organizations should work collaboratively with suppliers to address quality issues, share best practices, and drive mutual improvements.
This continuous improvement mindset with suppliers reinforces the overall quality culture and aligns more closely with strategic objectives.
Investing in Training and Development
The Critical Role of Training
Training is essential for implementing ISO 9001 quality metrics successfully. A skilled workforce is crucial for understanding and executing quality policies and procedures effectively.
Organizations should invest in training programs that help employees acquire the necessary skills for quality improvement initiatives. Examples include:
Workshops on quality standards for relevant teams.
Skills development sessions focused on process improvement.
Training not only contributes to employee engagement but also enhances competence, both crucial for improving quality metrics.
Assessing Training Effectiveness
It is equally important to evaluate the effectiveness of training programs. Organizations should regularly assess how deployment impacts employee performance and overall quality metrics.
Utilizing surveys, performance feedback, and assessments can provide valuable insights into training impact and help identify necessary adjustments for future initiatives.
The Path to Long-Term Success
Implementing ISO 9001 strategic quality metrics is crucial for organizations aiming for long-term improvement and alignment with business goals. By adopting a structured quality management approach, organizations can boost customer satisfaction, improve processes, and nurture a culture of continuous improvement.
Organizations must regularly monitor performance, engage employees, and ensure that quality policies are well-integrated. A strong commitment to these principles enables organizations to achieve ISO 9001 certification and thrive in a highly competitive market.
By embedding quality into their business strategy, organizations pave the way for sustained growth and resilience, benefitting both customers and stakeholders.
Comments