Mastering Lean Six Sigma: A Professional Guide to Unknown Success in Business
- islam Arid
- Nov 11, 2024
- 4 min read
Updated: Nov 15, 2024
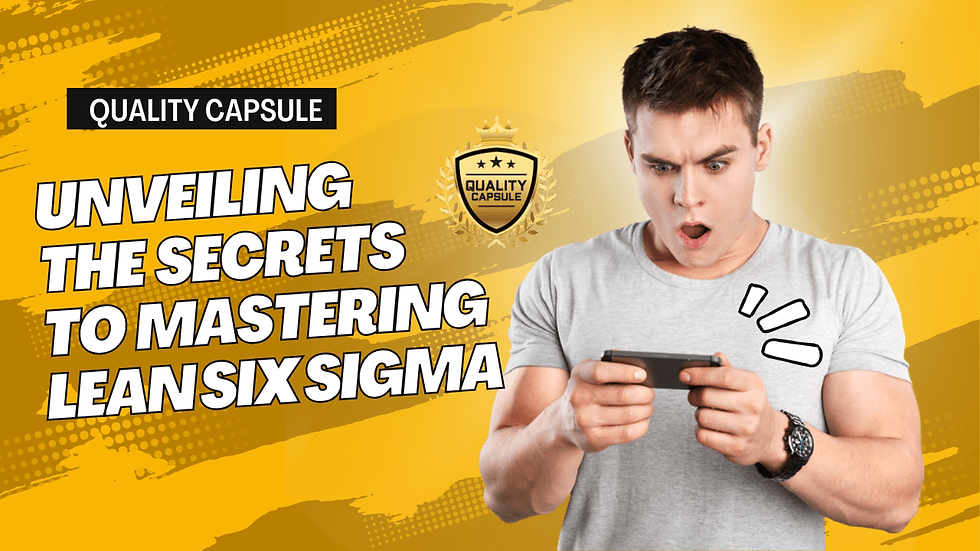
In today's fast-paced and competitive business environment, Lean Six Sigma has emerged as a vital strategy for organizations aiming to enhance processes and achieve operational excellence. This powerful approach combines Lean principles, which focus on reducing waste, with Six Sigma tools that aim to improve quality and reduce variations. When harnessed effectively, Lean Six Sigma can transform businesses, driving both efficiency and innovation.
This guide provides a clear pathway to mastering Lean Six Sigma, covering its essential components, practical applications, and strategies for successful implementation.
Understanding Lean Six Sigma
To truly master Lean Six Sigma, it’s important to grasp the foundational concepts of both Lean and Six Sigma.
Lean is all about efficiency. It removes waste in various forms, including excess inventory, long waiting times, and product defects. For instance, a manufacturing company might reduce its inventory costs by 30% simply by streamlining its supply chain processes.
On the other hand, Six Sigma focuses on quality. It aims to minimize defects so that processes produce a defect rate of fewer than 3.4 defects per million opportunities. For example, an electronics manufacturer that adopts Six Sigma might reduce its product defect rate from 5% to less than 1%, leading to significant savings and higher customer satisfaction.
By blending these methodologies, organizations embed a cycle of continuous improvement, enhancing quality while fostering innovation essential for long-term success.
Key Principles of Lean Six Sigma
1. Define
Every successful Lean Six Sigma project begins with a clear definition of the problem or the area that needs improvement. Setting specific goals is crucial. Tools like the SIPOC diagram (Suppliers, Inputs, Process, Outputs, Customers) can visually map out the process, ensuring that everyone involved understands the objectives and key players.
For example, a hospital may define a goal to reduce patient wait times in its emergency room by 20% over the next six months.
2. Measure
Next, it’s time to measure the current state of processes. This is where key performance indicators (KPIs) come into play. By measuring metrics like cycle time or customer complaint rates, organizations establish a baseline to assess improvements. For instance, a call center might measure its average response time of ten minutes and aim to reduce it to five minutes.
3. Analyze
Analysis revolves around identifying the root causes of inefficiencies. Employing tools like Pareto charts can help prioritize issues based on their impact. For instance, if 80% of complaints stem from just 20% of the processes, addressing those specific bottlenecks can yield significant improvements.
4. Improve
The improvement phase emphasizes implementing solutions. Techniques like Kaizen encourage teams to make small, ongoing changes for better results over time. Consider a scenario in a manufacturing setup where a new assembly method reduces production time by 15%. The PDCA (Plan-Do-Check-Act) cycle ensures these changes are evaluated before broader implementation.
5. Control
Post-implementation control is vital to keep improvements on track. Control plans with metrics ensure that processes stay within established parameters. Techniques such as Statistical Process Control (SPC) can help identify deviations swiftly. For example, a clothing manufacturer might track defect rates weekly to ensure they remain below their target threshold of 1%.
The Role of Leadership in Lean Six Sigma
Leadership is critical in the successful adoption of Lean Six Sigma. Leaders must be hands-on, facilitating a culture that values continuous improvement and employee involvement.
Investing in training programs helps equip employees with Lean and Six Sigma skills. For instance, having certified Green Belt and Black Belt professionals on your team can significantly boost expertise in project management and process improvement. Moreover, leaders need to communicate the vision behind Lean Six Sigma effectively, demonstrating its benefits to foster a shared commitment to quality across the organization.
Implementing Lean Six Sigma in Your Organization
1. Start Small
For organizations new to Lean Six Sigma, beginning with pilot projects can be a game changer. This focused approach allows teams to learn and apply the methodology in a low-pressure environment. Quick wins can illustrate the methodology’s benefits, encouraging broader implementation. A small project may involve improving a single process in production that results in saving two hours of labor each week.
2. Engage Employees
Employee engagement is key throughout the Lean Six Sigma process. Employees who are in the trenches possess invaluable insights into the day-to-day operations. Encouraging open communication and feedback nurtures a sense of ownership. For instance, holding regular brainstorming sessions can inspire innovative ideas to streamline operations.
3. Utilize Technology
Technology can be a powerful ally in tracking progress and analyzing data. Tools like Kanban boards can improve project transparency, while process mapping software can clarify workflows. Data analytics platforms will help organizations measure performance accurately, guiding decisions based on solid evidence.
Measuring Success: Indicators of Improvement
Evaluating the success of Lean Six Sigma initiatives requires a clear set of indicators.
Key performance indicators such as reduced cycle times, enhanced quality metrics, and improved customer satisfaction scores are essential to measure effectiveness. Financial outcomes, such as a 25% reduction in costs associated with defects and an increase in ROI from Lean Six Sigma projects, further underscore the value of these practices.
Regular assessment using these indicators helps organizations refine their strategies, ensuring improvements are sustained over time.
Achieving Operational Excellence
Mastering Lean Six Sigma goes beyond tool application; it requires building a culture that cherishes quality and continuous improvement. By understanding the principles, fostering effective leadership, and empowering employees, organizations can unlock hidden potential and realize operational excellence.
Whether beginning your Lean Six Sigma journey or enhancing existing efforts, maintaining a focus on quality and innovation will drive growth in today's dynamic business world. The key lies in embracing ongoing learning, efficient project management, and a relentless pursuit of improvement. Through these efforts, businesses can turn challenges into opportunities, paving the way for enduring success.
#sixsigma #leansixsigma #lean #leanmanufacturing #leadership #training #kaizen #s #iso #greenbelt #projectmanagement #processimprovement #quality #o #business #kanban #pdca #blackbelt #innovation #management #growth #improvement #operationalexcellence #dmaic #managementconsulting #qualityassurance #iatf #leanthinking #yellowbelt #certification
Comments