Quality Management Pillars: Design, Conformance, and Performance
- islam Arid
- Oct 22, 2023
- 6 min read
Updated: Feb 20, 2024
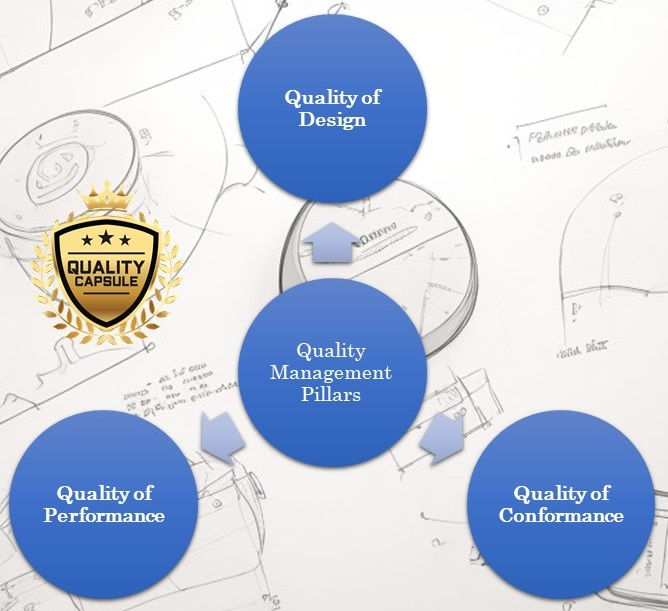
Introduction:
Welcome to an article where we're going to dive deep into Quality Management Pillars. Quality management is a comprehensive approach that enables companies to meet and exceed customer expectations while continuously improving their processes. So, let's discuss the three pillars associated with the definition of quality management: Quality of Design, Quality of Conformance, and Quality of Performance.
Quality of Design:
Quality of design is the first pillar of quality management, and it focuses on the foundational conditions or requirements that a product or service must meet to fulfill customer expectations. It's about crafting a product or service that not only meets but ideally exceeds the customer's needs, all without unnecessary complexity or additional costs. This balancing act involves creating a design that is not only effective but also cost-efficient to align with customer expectations.
To illustrate, consider a cell phone in the design stage. When designing a new one, the company must meet certain fundamental conditions to satisfy customers. It must have a functional touchscreen, support multiple apps, provide decent battery life, and have a camera capable of capturing clear photos. Quality of design is influenced by many factors, such as product type, cost, profit policy, market demand, and the availability of essential components and materials. Moreover, product reliability plays a critical role in ensuring that the design stands the test of time.
Design phase considerations:
Cost-Efficiency: Achieving a balance between quality and cost is crucial. While creating a product that surpasses customer expectations is important, it should also be economically viable. This requires careful decision-making regarding the use of materials, manufacturing processes, and technology.
Market Demand: Understanding market demand is essential for designing a product that will be successful in the marketplace. The design must align with current consumer preferences and anticipate future trends.
Sustainability: In today's environmentally conscious world, designing products with sustainability in mind is increasingly important. Quality of design should include considerations for minimizing environmental impact, such as reducing waste, conserving resources, and ensuring recyclability.
User-Centered Design: To excel in the quality of design, it is crucial to take a user-centered approach. This means conducting market research, gathering user feedback, and designing products that are intuitive and user-friendly.
Reliability: Reliability is a cornerstone of the quality of design. Products must be engineered to last, reducing the likelihood of defects and ensuring customer satisfaction over the long term.
Quality of Conformance:
Quality of conformance is all about ensuring that the product or service meets the standards defined during the design phase after it's manufactured or delivered. This phase is also concerned with quality control from raw material to the finished product. Three key aspects guide this part of the quality concept: defect detection, defect root cause analysis, and defect prevention.
Imagine you're in a car showroom for a new car. You have high expectations for safety, performance, and reliability. Here, Quality of conformance plays a vital role in the production of this car. It's about ensuring that every component, from the engine to the brakes and electronics, conforms to the precise standards established during the design phase.
Defect prevention is a proactive approach aimed at averting defects. It often involves the application of statistical process control techniques.
Detecting defects can take various forms, such as inspection, testing, and data analysis to identify any deviations from the specified quality criteria.
Subsequently, the root causes behind the presence of defects are investigated, and corrective actions are taken to prevent the recurrence of the defect.
Suppose during quality checks, a car's braking system exhibits an anomaly that could affect its performance. This is where defect root cause analysis comes into play. Skilled engineers investigate the underlying cause of the defect. Once the root cause is identified, corrective actions are swiftly implemented to prevent similar defects in future production runs. This quality control ensures that every car you purchase meets the promised quality standards, providing you with a safe and reliable vehicle.
Quality of conformance considerations:
Total Quality Management (TQM): Many organizations employ TQM principles, which encompass all aspects of conformance, from raw materials to finished products. This comprehensive approach involves everyone in the organization, from top management to frontline employees, in the pursuit of quality.
Continuous Improvement: The quality control process doesn't end with the first batch of products. It's a continuous cycle of monitoring, evaluating, and improving. Techniques such as Six Sigma, Lean Manufacturing, and Kaizen are commonly used to maintain and enhance conformance.
Supply Chain Management: Quality of conformance extends beyond a company's four walls. Ensuring that suppliers meet the same quality standards is critical. Companies often work closely with their suppliers to ensure the quality of raw materials and components.
Regulatory Compliance: In some industries, regulatory requirements play a significant role in quality conformance. Companies must adhere to these regulations to ensure the safety and quality of their products.
Customer Feedback: Incorporating customer feedback into quality conformance is invaluable. It allows companies to identify areas for improvement and make adjustments based on real-world usage and customer expectations.
Quality of Performance
Quality of performance is all about how well a product or service functions when put to use. It measures the degree to which the product or service satisfies the customer from the perspective of both the quality of design and the quality of conformance.
When we talk about quality of performance, meeting customer expectations is the primary focus. A product or service must not just meet but exceed customer expectations because if a product or service does not live up to customer expectations, it can lead to dissatisfaction and potentially, a loss of business.
Consider a smartphone, a product many of us use daily. The quality of performance for a smartphone is crucial. A high-quality smartphone not only has a sleek design but also functions smoothly. It should provide fast processing, a long-lasting battery, and a user-friendly interface. Now, imagine purchasing a smartphone that doesn't live up to your expectations. It lags, the battery drains quickly, and the interface is confusing. In this case, adjustments would be needed in the design phase. The manufacturer must improve the phone's functionality, optimize its software, and address any hardware issues.
On the other hand, when you have a high-quality smartphone that meets or exceeds your expectations, it enhances your daily life. It becomes a valuable tool that you rely on. This illustrates how 'Quality of Performance' directly impacts our satisfaction with a product. Whether it's a smartphone or any other product or service, meeting and surpassing customer expectations is paramount.
Quality of performance consideration:
Customer-Centric Metrics: Measuring the quality of performance often involves customer-centric metrics. For example, in the case of a smartphone, key performance indicators might include processing speed, battery life, camera quality, and ease of use. These metrics are derived from direct customer feedback and market research.
Feedback Loops: To continually enhance the quality of performance, companies need to establish feedback loops with customers. This includes collecting data on product usage and seeking input on potential improvements.
User Experience (UX) Design: UX design is integral to the quality of performance. It's about creating products and services that not only function well but also provide a satisfying and enjoyable experience for users.
Product Testing: Rigorous product testing is essential to verify that a product performs as expected. This includes performance testing, usability testing, and functionality testing.
Service Quality: In the case of service-based businesses, quality of performance involves elements such as responsiveness, efficiency, accuracy, and customer satisfaction. Customer service, for instance, is a critical aspect of the quality of performance in these cases.
In conclusion,
quality management pillars encompass the three key aspects of quality: design, conformance, and performance. These pillars ensure that companies deliver products and services that not only meet but exceed customer expectations, ultimately leading to customer satisfaction and business success. Quality management is an ongoing process that requires a commitment to continuous improvement and a keen focus on these pillars.
Our courses :
Hashtags:
#qualitycontrol #migos #qualityassurance #quality #hiphop #lilbaby #quavo #qc #culture #atlanta #quavohuncho #qualitycontrolmusic #cardib #iso #explore #offset #explorepage #music #migosnation #rap #nickiminaj #yrn #guccimane #drake #rocnation #pf #manufacturing #liluzivert #dababy #migosnews
Comments