Optimizing Organizational Processes for ISO 9001: Mapping and Implementing Quality Standards
- islam Arid
- May 1
- 5 min read
Enhancing Your Organization with ISO 9001
Implementing ISO 9001 standards can significantly improve how an organization manages quality. For businesses aiming to meet ISO 9001 requirements, it’s crucial to effectively map and identify organizational processes. This blog post highlights the importance of aligning processes with quality standards and provides clear, actionable steps for successful ISO 9001 implementation.
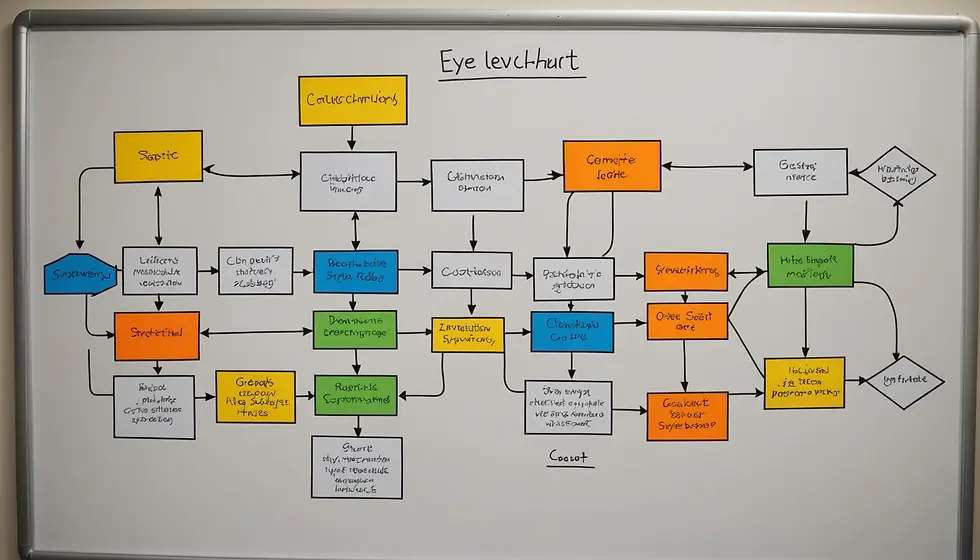
The ISO 9001 framework focuses on ensuring consistent quality and continuous improvement. A comprehensive understanding of existing processes is vital. By mapping these processes, organizations can identify improvement areas, ensuring compliance with ISO 9001 certification requirements while promoting a culture of quality and customer satisfaction.
Understanding ISO 9001 Fundamentals
Before diving into process mapping, it's important to grasp the basics of ISO 9001. This international standard sets the criteria for a quality management system (QMS) based on several key principles:
Customer Focus: Recognizing customer needs and striving to meet their expectations. For example, a survey conducted by the American Society for Quality found that companies prioritizing customer feedback report a 10-15% increase in customer satisfaction.
Leadership: Establishing a unified purpose and direction for the organization. Strong leadership can lead to a 20% increase in employee engagement, as shown by a Gallup study.
Engagement of People: Involving employees at all levels to contribute to success. Research indicates that engaged employees can boost organizational productivity by 17%.
Process Approach: Managing activities as interconnected processes, which improves overall efficiency.
Understanding these principles lays a solid foundation for effectively mapping organizational processes.
The Importance of Process Mapping in Quality Management
Process mapping is essential for implementing ISO 9001. By visually representing workflows, organizations can evaluate task interconnectivity, identify redundancies, and discover opportunities for improvement.
For example, a shoe manufacturing company that used process mapping found it could reduce its production cycle time by 25% by streamlining its supply chain processes. Effective mapping also ensures everyone involved knows their roles and responsibilities, helping identify areas that may not comply with the standards and aiding in the development of corrective actions.
Steps to Identify and Map Processes
1. Define Organizational Objectives
Start by defining your organization’s quality objectives. Ensure these objectives align with ISO 9001 requirements and create a clear roadmap for quality management. For instance, a goal to reduce product defects by 30% over the next year can guide process improvements.
2. Engage Stakeholders
Involve stakeholders from various departments. Different perspectives can uncover vital insights about process functionality and improvement needs. Collaboration encourages employee buy-in, fostering a quality culture throughout the organization. For example, a cross-departmental team at a tech firm discovered 15 process overlaps, leading to a streamlined operation.
3. Use Mapping Techniques
There are several techniques for process mapping, including flowcharts and SIPOC (Suppliers, Inputs, Process, Outputs, Customers) diagrams. Each technique has its advantages in visualizing processes.
Flowcharts
Flowcharts detail the sequential steps of a process. They help identify decision points, responsibilities, and potential bottlenecks. Using flowcharts improved problem-solving efficiency by 40% in a food processing company.
SIPOC Diagrams
SIPOC diagrams provide a high-level overview of processes, ensuring that all team members have a shared understanding before digging deeper. They can reduce misunderstandings in project requirements by 25%.
4. Document Existing Processes
Collect data on how tasks are performed. Documenting includes understanding inputs, outputs, and performance metrics. It should incorporate relevant ISO 9001 procedures, which align processes with the organization’s quality policy.
5. Analyze and Identify Gaps
Conduct a gap analysis to find deviations from ISO 9001 requirements. This assessment tells you which processes need improvement and helps create a plan of action. Addressing gaps early is essential for effective ISO 9001 implementation.
6. Develop Improvement Actions
For each identified gap, develop targeted improvement actions. These may include retraining employees, altering workflows, or introducing new technologies. An electronics manufacturer that restructured its training program saw a 20% reduction in assembly errors.
7. Validate and Monitor Changes
Validate the effectiveness of changes made. Regular monitoring helps assess whether improvements achieve the desired impact. Metrics, such as defect rates or customer complaints, can help gauge success.
Integrating Risk Management in Process Mapping
Risk management is crucial in ISO 9001:2015. Organizations must analyze potential risks in processes. Implementing risk management helps address any issues affecting product or service quality.
Risk Assessment Techniques
Several techniques can enhance risk assessment, including:
Failure Mode and Effects Analysis (FMEA): A structured way to identify failure points and their impacts on performance. A manufacturing plant using FMEA reduced its defect rates by 30%.
Root Cause Analysis (RCA): A method for identifying the fundamental cause of a problem. This allows for effective corrective actions and can improve problem resolution efficiency by up to 35%.
Embedding Risk Management in Processes
Incorporate risk management by identifying potential risks, analyzing their likelihood and impact, and developing strategies to mitigate them. This approach ensures compliance with ISO 9001 requirements and protects product quality.
Leveraging Technology for Process Mapping
In today’s digital age, organizations can use various tools to streamline process mapping. Software solutions enhance process visualization and sharing, improving understanding and collaboration among employees.
Popular Process Mapping Software
Some widely-used tools include:
Visio: Ideal for creating detailed flowcharts and diagrams.
Lucidchart: A user-friendly tool that supports real-time collaboration.
Microsoft Project: Excellent for managing and visualizing project workflows.
Using these tools not only helps map processes effectively but also keeps documentation accessible and current.
Training and Development for Continuous Improvement
To align processes with ISO 9001, organizations must invest in training and development. Continuous employee training encourages a culture of quality awareness. Regular training boosts compliance and tackles newly identified risks.
Elements of Effective Training Programs
An effective training program should include:
Comprehensive education on ISO 9001 requirements.
Hands-on training for mapping techniques.
Ongoing evaluations to assess employee knowledge retention.
Providing these resources creates skilled employees who actively participate in quality management.
Conducting Internal Audits
Internal audits are vital for maintaining ISO 9001 compliance. They assess whether processes contribute effectively to quality objectives and identify areas for improvement.
Planning Internal Audits
To conduct successful audits:
Create a clear audit plan stating the scope and objectives.
Assign qualified personnel for audits.
Develop a checklist based on ISO 9001 requirements to guide the process.
Conduct regular internal audits to promote transparency and accountability across the organization.
Engaging Suppliers in Quality Management
The quality of products and services is often influenced by suppliers. Therefore, involving them in the ISO 9001 implementation process is crucial for consistent quality throughout the supply chain.
Supplier Quality Management
Collaborating with suppliers involves:
Clearly communicating quality standards and expectations.
Conducting regular evaluations of supplier performance.
Implementing corrective actions for any nonconformities.
Actively engaging suppliers builds a culture of quality and ensures all stakeholders contribute effectively to quality management objectives.
Final Thoughts on Process Mapping and Quality Standards
Mapping organizational processes is key to successfully implementing ISO 9001. By understanding and documenting workflows, organizations can identify areas for improvement that align with quality objectives. Enhancements through effective process mapping ensure not only compliance with ISO 9001 but also promote a culture of continuous improvement and customer satisfaction.
Integrating risk management, leveraging technology, investing in training, and involving suppliers further strengthen the effectiveness of quality management systems. Following these steps helps organizations stay competitive in a rapidly changing marketplace, ultimately fostering long-term success and enhanced customer trust.
Comments