Maximizing Quality: The ISO 9001 Approach to Designing and Developing Products and Services
- islam Arid
- May 1
- 5 min read
In today's fast-paced and competitive market, quality is no longer optional. Businesses that prioritize delivering high-quality products and services reap significant rewards, including enhanced customer satisfaction, increased market share, and greater profitability. One of the most esteemed standards for ensuring quality across industries is ISO 9001. This post will take a closer look at the ISO 9001 framework, focusing on its application during the design and development phases of products and services, and how it fosters a culture of excellence.
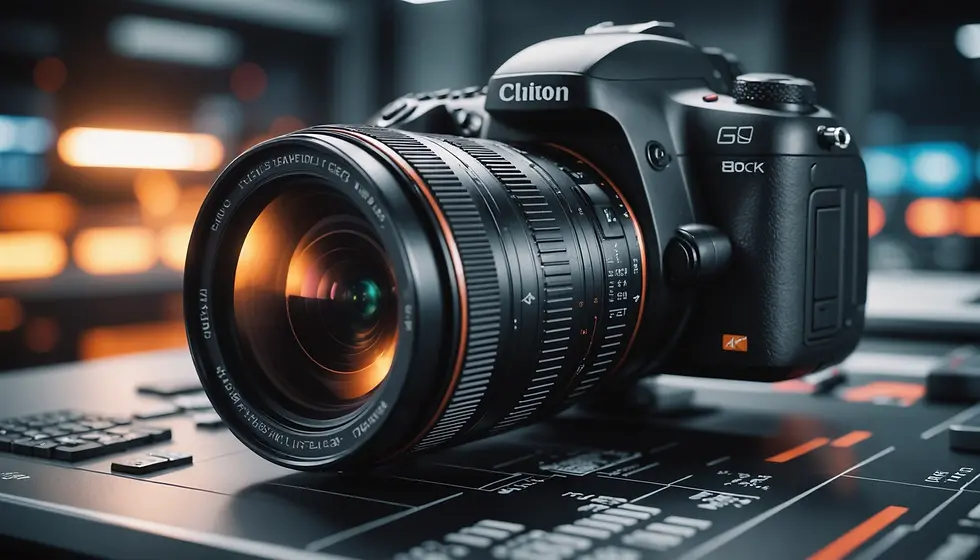
Understanding ISO 9001
ISO 9001, developed by the International Organization for Standardization (ISO), outlines criteria for a quality management system (QMS). Think of it as a roadmap for organizations aiming to boost customer satisfaction through effective quality management.
The goal of ISO 9001 is clear: businesses need to consistently provide products and services that meet customer and regulatory requirements. When organizations comply with this standard, they demonstrate a dedication to quality and continuous improvement. This commitment helps them compete confidently on a global scale.
ISO 9001 incorporates key principles such as customer focus, leadership, engagement of people, process approach, improvement, evidence-based decision-making, relationship management, and a systems approach to management. Adopting these principles allows organizations to develop a responsive and agile QMS.
The Importance of Design and Development in Quality Management
Design and development are pivotal phases in the lifecycle of products and services. These stages lay the groundwork for quality and align offerings with customer expectations and regulatory requirements. Integrating ISO 9001 principles during these stages can help organizations minimize risks, streamline processes, and improve overall performance.
Identifying Customer Needs
Grasping customer needs is crucial in the design and development stage. ISO 9001 encourages organizations to gather and analyze customer feedback, providing valuable insights into their expectations. This alignment with market demand can lead to impressive outcomes: companies that listen to customer feedback report a 20% increase in satisfaction rates.
Engaging with customers through surveys and focus groups enables teams to identify essential requirements. By documenting these needs, organizations can better shape their design and development efforts.
Defining Quality Objectives
Establishing clear quality objectives is vital within ISO 9001's design and development process. These goals should align with broader organizational aims and provide specific, measurable targets to guide projects from start to finish.
Quality objectives can include clear metrics such as reducing defects by 15%, increasing usability scores by 25%, or improving on-time delivery rates to 95%. By identifying these goals early, companies can set a clear roadmap that meets customer expectations and internal performance benchmarks.
Implementing a Structured Design Process
A systematic approach to design and development is critical under ISO 9001. This structured process outlines necessary steps, responsibilities, and timelines, ensuring that team members share a clear direction.
Key components of a structured design process may consist of:
Conceptualization: Generating initial ideas based on customer feedback and market research.
Prototyping: Creating models to test and refine design concepts based on real-user interactions.
Following this structured method helps organizations reduce unnecessary iterations and enhances efficiency, ultimately leading to a superior quality end product.
Managing Risks in Design and Development
Risk management is essential in ISO 9001 and has a significant impact on the design and development of products and services. Early identification of potential risks can save valuable time and resources while improving quality outcomes.
Conducting Risk Assessments
Conducting regular risk assessments during the design and development process helps organizations identify vulnerabilities. For example, statistics show that businesses implementing structured risk assessments see a 30% decrease in product recalls.
Tools like Failure Mode and Effects Analysis (FMEA) allow teams to evaluate design elements systematically, pinpointing possible flaws and executing corrective actions before a product reaches the market.
Incorporating Feedback Loops
Setting up feedback mechanisms ensures that insights from customers and stakeholders are incorporated into the design and development process. For instance, a company that actively integrates customer feedback can see a 25% improvement in user satisfaction post-launch.
Establishing regular internal audits gives organizations a chance to assess the effectiveness of their design and development processes and identify areas needing corrective action.
Document Control and Traceability
Documentation plays a vital role in the ISO 9001 framework. Well-organized and thorough records are key to quality management and compliance, simplifying decision-making processes.
Effective Document Control Systems
Creating an efficient document control system helps organizations keep track of design and development documents, including specifications and regulatory guidelines.
Key elements include:
Version Control: Ensuring all team members use the latest documentation.
Accessibility: Making essential documents readily available for all stakeholders involved in the design and development process.
This organized approach supports quality management and fosters accountability throughout the organization.
Maintaining Traceability
Traceability is essential to ensure that every design decision is documented, allowing organizations to trace back to the root of any issues or defects. For example, businesses that maintain proper traceability find that they can resolve quality issues 40% faster.
Such practices bolster compliance with ISO 9001 by demonstrating diligence and transparency throughout design and development.
Quality Control and Assurance
Quality assurance and control are crucial to effectively implementing ISO 9001. Concentrating on these aspects throughout the design and development stages leads to high-quality results.
Implementing Quality Control Measures
Quality control involves systematic inspection and testing of products and services. By establishing robust quality control measures, organizations can catch and address defects early in the design process, avoiding costly revisions later.
Common quality control techniques include:
Statistical Process Control (SPC): Monitoring and controlling processes to ensure quality.
Inspection Procedures: Rigorously checking products against quality standards.
These strategies help maintain ISO 9001 compliance, leading to superior outputs.
Fostering a Quality Culture
Creating a company-wide culture focused on quality is crucial for successful design and development. This can be achieved by:
Training and Development: Educating team members on ISO 9001 principles and quality tools.
Management Commitment: Ensuring leaders visibly support quality initiatives.
Recognizing and rewarding teams for their quality-driven efforts cultivates motivation and a commitment to continuous improvement.
Emphasizing Continuous Improvement and Innovation
Continuous improvement and innovation are foundational to the ISO 9001 framework. By embracing these principles, organizations can maintain high-quality standards and respond effectively to changing market demands.
Embracing the PDCA Cycle
The Plan-Do-Check-Act (PDCA) cycle provides a practical framework for continuous improvement by encouraging teams to:
Plan: Set quality objectives and identify where improvements can be made.
Do: Apply these improvements in the design processes.
Following this cycle allows organizations to create a pathway for sustained innovation and quality enhancement.
Encouraging a Culture of Innovation
Fostering an innovative environment encourages creative thinking within the organization. This can be implemented by:
Allocating resources for research and development projects.
Encouraging collaboration across different teams.
A strong focus on innovation not only boosts product quality but also keeps companies competitive in a constantly changing landscape.
Final Thoughts
Implementing the ISO 9001 framework during the design and development of products and services establishes a pathway toward maximizing quality. Highlighting customer needs, managing risks, and cultivating a culture of continuous improvement enables businesses to align their offerings with market demands, resulting in greater customer satisfaction.
The principles of ISO 9001 enhance quality management processes, promote accountability, and aid compliance with industry standards. By refining quality objectives, document control practices, and overall management systems, companies build a solid foundation for growth and innovation in a dynamic business environment.
Embracing the ISO 9001 approach goes beyond attaining certification; it signifies a commitment to embedding quality throughout all organizational operations. In doing so, businesses not only maximize quality but also forge strong, lasting relationships with customers, ensuring long-term success.
Comments