Integrating data analytics into ISO 9001 quality management systems
- islam Arid
- Nov 30, 2024
- 4 min read

In today's fast-paced and data-driven marketplace, organizations are constantly searching for ways to excel. Leveraging the power of data is essential for staying competitive. One area that is seeing significant growth is the integration of data analytics into ISO 9001 Quality Management Systems (QMS). By weaving data analytics into these systems, organizations not only comply with global quality standards but also foster continuous improvements that can transform their operations.
Understanding ISO 9001 and Its Importance
ISO 9001 is a globally recognized standard that lays out the requirements for a quality management system. It is built on key principles such as customer focus, leadership, a process approach, and a commitment to continuous improvement. By embracing these principles, organizations can enhance customer satisfaction while improving decision-making and operational efficiency.
Implementing ISO 9001 helps businesses of all sizes maintain consistent quality in their products or services. However, the success of a QMS is closely linked to how effectively an organization utilizes data from its processes. Embracing data analytics can significantly enhance this framework, offering insights that lead to informed decisions and strategic improvements.
The Role of Data Analytics in Quality Management
The impact of data analytics on quality management is substantial. Organizations can analyze data patterns and trends to gain valuable insights into performance, defects, process efficiencies, and customer satisfaction.
Enhancing Decision-Making Through Data
Data analytics can transform raw information into actionable insights, enabling organizations to make better decisions about their quality management processes. Moving from instinct-based choices to data-supported decisions boosts reliability and efficiency in tackling quality issues.
For example, a manufacturing company might analyze defect rates over several months. By identifying a trend where defects spike during a particular production run, the organization can proactively address potential problems, thus reducing waste. In fact, companies utilizing data-driven decision-making have reported up to a 25% reduction in defect rates.
Streamlining Reporting and Compliance
Compliance with ISO 9001 often requires extensive documentation and reporting, which can be tedious. Data analytics can automate many of these processes, allowing organizations to save both time and resources.
With automated data analysis, key quality metrics can be gathered, documented, and reported more efficiently. This automation minimizes errors and provides real-time insights into compliance status. Organizations employing data analytics tools have seen efficiency improvements of up to 30% in their reporting processes, enabling quicker responses to compliance challenges.
Implementing Data Analytics in ISO 9001
To successfully integrate data analytics into an ISO 9001 QMS, organizations should follow a focused approach. Here are some practical steps to consider:
Step 1: Assess Current QMS and Identify Data Sources
Start with a thorough evaluation of the existing quality management system and identify available data sources. These may include customer feedback, internal audits, process performance, and product quality metrics.
Conducting a comprehensive assessment will help you determine where data can drive the most meaningful improvements. For instance, a retail company may find that analyzing customer return data can provide insights into product quality and expectations.
Step 2: Define Key Performance Indicators (KPIs)
Establish clear and measurable KPIs aligned with quality management goals. These KPIs should reflect the quality objectives outlined in ISO 9001.
By defining relevant KPIs, organizations can effectively analyze data and monitor their performance against specific benchmarks. A transportation company, for example, might track on-time delivery percentages as a key indicator of service quality.
Step 3: Select Appropriate Data Analytics Tools
After identifying KPIs, seek out data analytics tools that meet your quality management needs. Various software solutions can analyze data and provide dashboards and reports that visualize performance metrics, making data more accessible.
Choosing the right tools ensures that the insights gained can be easily understood and acted upon. Companies that have implemented effective data analytics platforms report improved decision-making processes and enhanced team collaboration.
Step 4: Train Teams on Data Usage
Introducing data analytics tools is just the beginning. Employees must receive training on how to utilize these tools and understand the insights derived from data analytics. Fostering a culture of data-driven decision-making empowers teams and encourages collaboration across departments.
For example, a healthcare organization could train its staff on data analytics to better analyze patient feedback and improve service quality, ultimately enhancing healthcare delivery.
Step 5: Monitor and Evaluate Outcomes
After data analytics systems are up and running, organizations need to continuously monitor and evaluate results. Regular assessments of the impact of data analytics on decision-making, compliance, and overall performance can reveal both successes and areas for enhancement.
Staying flexible in response to insights gained from ongoing data analysis is key. For instance, a software company might adjust its features based on user feedback trends to improve product quality continuously.
The Future of Quality Management with Data Analytics
The future of quality management within ISO 9001 is increasingly driven by data analytics. As technology advances, tools such as Artificial Intelligence (AI) and Machine Learning (ML) will enhance predictive capabilities.
Increased Predictive Capabilities
Predictive analytics can help organizations identify potential quality challenges before they arise. By analyzing historical data patterns, organizations can proactively adjust processes or products, minimizing disruption.
A prime example is a food manufacturer using predictive analytics to forecast spoilage risks, allowing for timely interventions that can reduce waste by up to 20%.
Enhanced Customer Experience
Data analytics provides a deeper understanding of customer preferences and expectations. By continuously analyzing customer feedback and behavior, organizations can fine-tune their quality management efforts to deliver exceptional products and services.
Companies that prioritize a customer-centered approach through data analytics often achieve higher customer satisfaction ratings—sometimes exceeding 90%—thereby strengthening their market position.
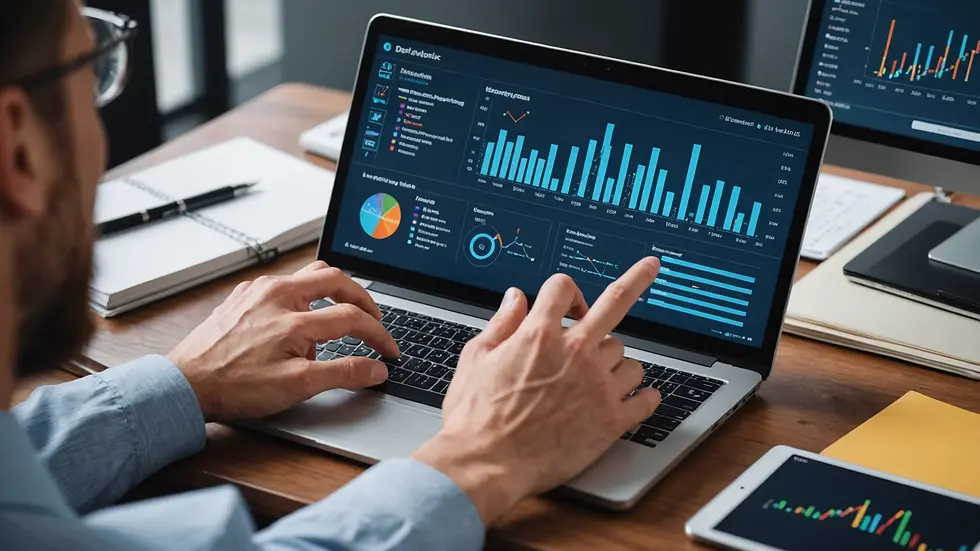
Elevating Quality Management with Data Analytics
Integrating data analytics into ISO 9001 quality management systems introduces exciting new opportunities for organizations striving for excellence. By embracing data-driven decision-making, businesses can elevate their processes, enhance compliance, and ultimately boost customer satisfaction.
Understanding the significance of data analytics in quality management allows organizations to create a resilient framework that not only aligns with ISO 9001 standards but also promotes ongoing improvement and operational success.
As industries evolve, adopting analytical methodologies will be crucial for organizations wanting to stay ahead in quality management. Committing to quality enhancement through data analytics reflects an organization’s dedication to excellence and its readiness to thrive in a competitive environment.
The journey to integrating data analytics into ISO 9001 may require time and adjustments, but the benefits—greater efficiency, improved compliance, and enhanced customer satisfaction—are invaluable.
Comentarios