Implementing Effective Control of Nonconformities in ISO 9001: A Professional Approach
- islam Arid
- May 1
- 5 min read
In today's competitive landscape, businesses are constantly striving for excellence and customer satisfaction. Achieving this requires implementing robust quality management systems, such as the ISO 9001 standard. This structured framework helps organizations manage their processes and enhance quality. A critical component within this framework is the control of nonconforming outputs. Effectively handling nonconformities is vital for compliance, process improvement, and maintaining product and service quality. This post explores actionable strategies for managing nonconforming outputs during ISO 9001 implementation, offering insights for organizations eager to boost their quality management practices.
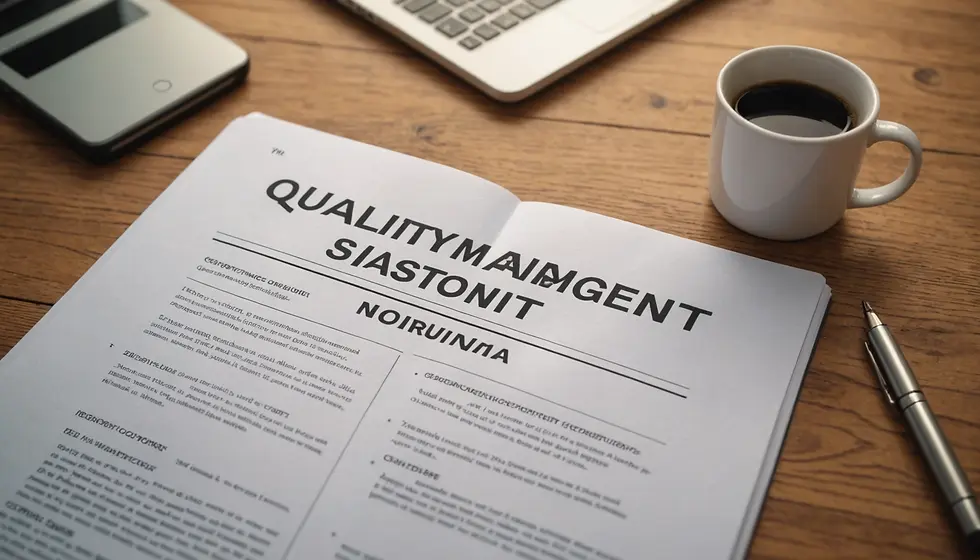
Understanding Nonconformities in ISO 9001
Nonconformities occur when outputs do not meet established requirements. These shortcomings can arise from various sources, such as processes, products, and services. Recognizing and managing nonconformities is a vital element of the ISO 9001 framework. The standard underlines that organizations must identify nonconforming outputs, assess their potential impact, and enact corrective actions to prevent future occurrences.
ISO 9001 mandates organizations develop procedures for addressing nonconformities. This includes rigorous documentation, implementation of corrective actions, and ongoing monitoring to ensure adherence to quality standards. Grasping the nature of these nonconformities is the crucial first step toward effective management.
The Importance of Control in Managing Nonconformities
Effective control over nonconforming outputs is essential for several reasons. First, it reduces risks associated with poor quality, which can lead to customer dissatisfaction, reputational harm, and financial losses. A structured approach to managing nonconformities also fosters continuous improvement efforts, aligning with ISO 9001's emphasis on enhancing operational processes.
Furthermore, controlling nonconformities cultivates a proactive quality culture within the organization. When employees understand the significance of addressing nonconformities, it fosters accountability and promotes active engagement in quality assurance practices across all organizational levels.
Steps in Managing Nonconforming Outputs
1. Identification of Nonconformities
Identifying and accurately defining nonconformities is the first step in effective management. Various methods can aid in this process:
Internal audits: Conducting regular audits can spotlight compliance gaps with ISO 9001 requirements. For example, companies that perform quarterly audits often detect 20% more nonconformities compared to those that audit annually.
Customer feedback: Actively gathering insights from customers can uncover instances of nonconformance that may not be evident within the organization. A customer satisfaction survey indicating 15% dissatisfaction could reveal underlying issues needing attention.
Monitoring performance metrics: Tracking key performance indicators (KPIs) can reveal trends signifying underlying problems. For instance, a 10% increase in product returns may flag a quality issue needing resolution.
Establishing a clear definition of what constitutes a nonconformity in your organization is crucial to ensure that all employees share a common understanding.
2. Documentation of Nonconformities
Once nonconformities are identified, thorough documentation is essential. Effective documentation should include:
The nature of the nonconformity
The affected process or product
The date of identification
The person responsible for addressing it
This documentation serves multiple purposes. Beyond acting as a reference for future cases, it helps track the effectiveness of corrective actions.
3. Assessment and Analysis
Following documentation, organizations need to assess the potential impact of nonconformities. This evaluation should consider:
The severity of the nonconformity
Implications for customer satisfaction
The potential for recurrence
By analyzing these factors, organizations can prioritize their responses, directing resources to address the most critical nonconformities first.
4. Implementing Corrective Actions
Corrective actions are vital in resolving nonconformities and preventing their recurrence. Organizations should adopt a systematic approach to implementing these actions:
Identifying root causes: Techniques like the 5 Whys or Fishbone Diagram can be employed to discover underlying causes.
Developing action plans: Creating specific, measurable, achievable, relevant, and time-bound (SMART) action plans is crucial for addressing root causes effectively.
Assigning responsibilities: Designating individuals or teams responsible for executing action plans ensures accountability at every stage.
By structuring corrective actions, organizations can not only resolve current issues but also build resilience against future nonconformities.
5. Monitoring and Measuring Effectiveness
Monitoring the effectiveness of corrective actions is essential. This can involve:
Conducting regular follow-up audits
Continuously tracking performance metrics
Gathering customer feedback
Regular monitoring allows organizations to assess whether implemented measures achieve desired outcomes and whether further adjustments are necessary.
6. Training and Development
Training employees is critical for fostering a culture of quality and compliance. Employees should understand:
The importance of identifying nonconformities
The established procedures for reporting and resolving them
By investing in training, organizations empower their workforce to actively engage in quality management initiatives.
7. Review and Continual Improvement
The ISO 9001 standard emphasizes the principle of continual improvement. Organizations must routinely review their procedures for managing nonconformities. This can be achieved through:
Management reviews
Internal audits
Employee feedback sessions
By nurturing a mindset of continual improvement, organizations can adapt their quality management strategies to meet evolving standards and customer expectations more effectively.
Common Challenges in Managing Nonconformities
While managing nonconforming outputs can yield significant benefits, organizations often face common challenges, such as:
1. Resistance to Change
Employees may hesitate to adopt new processes or report nonconformities out of fear of repercussions. To combat this, organizations need to establish a non-punitive culture that encourages open dialogue about quality issues.
2. Insufficient Training
Without proper training, employees may not fully grasp the significance of nonconformities or how to address them. Comprehensive training programs can equip staff with the necessary skills to manage nonconformities effectively.
3. Lack of Documentation
Failure to document nonconformities can impede compliance and improvement efforts. Organizations must prioritize maintaining accurate, detailed records to support transparency and accountability.
Best Practices for Controlling Nonconformities
To enhance the control of nonconforming outputs within the ISO 9001 framework, organizations can adopt the following practices:
1. Foster a Quality Culture
Encouraging a quality-centric approach across all levels of the organization ensures that every employee understands their role in managing nonconformities.
2. Implement Technology Solutions
Leveraging technology, such as quality management software, can streamline documentation and tracking of nonconformities. Many organizations that utilize such software have reported a 30% improvement in efficiency.
3. Engage Stakeholders
Collaborating with stakeholders, including suppliers and customers, during the nonconformity management process can yield valuable insights and collective solutions.
4. Regularly Review Processes
Establishing a routine for reviewing processes related to nonconformities ensures that they remain relevant and effective in addressing current quality challenges.
Final Thoughts
Managing nonconforming outputs in ISO 9001 implementation is a crucial component of quality management that organizations must prioritize. Implementing an effective control system for nonconformities not only supports compliance with ISO 9001 requirements, but also promotes overall business success—evident through enhanced quality, improved customer satisfaction, and a culture of continuous improvement.
In an increasingly competitive environment, companies that master the art of managing nonconformities will not only meet but exceed customer expectations. By embracing ISO 9001 principles while navigating the journey of nonconformity control, organizations pave the way for sustained success and operational excellence.
Comments