Identifying Risks in ISO 9001: Practical Tools and Methods for Quality Management
- islam Arid
- Apr 24
- 5 min read
Updated: Apr 29
In the world of quality management, recognizing potential risks is essential for maintaining standards that comply with ISO 9001 requirements. The ISO 9001 framework helps organizations produce high-quality products and services. However, effective risk management must be woven into the fabric of organizational processes to meet these standards. This post discusses practical tools and methods for identifying risks, which not only support compliance but also drive continuous improvement in quality management.
Understanding the Importance of Risk Identification
Identifying risks is crucial because it reveals potential problems that could prevent an organization from achieving its quality goals. For instance, a company that fails to identify a risk in its supply chain could suffer delays, resulting in a potential loss of up to 25% in revenue based on industry estimates. By proactively recognizing these risks, organizations can implement corrective actions before issues escalate, leading to smoother operations and improved customer satisfaction.
Neglecting to identify risks can result in nonconformities that damage compliance and erode stakeholder trust. A strong risk management strategy cultivates a culture focused on quality, enabling organizations to quickly adapt to changes while remaining compliant with ISO 9001 standards.
Common Risk Identification Techniques
Numerous tools and methods can be utilized for risk identification within the ISO 9001 framework. Below are some of the most effective techniques:
1. SWOT Analysis
SWOT analysis assesses an organization’s Strengths, Weaknesses, Opportunities, and Threats. By identifying risks as Threats or Weaknesses, organizations can pinpoint areas of concern and develop strategies for improvement.
*Example: A manufacturing firm may identify a Weakness in its outdated machinery, which could lead to higher failure rates. Conversely, recognizing an Opportunity in emerging markets could inform their growth strategy.
This method encourages teams to consider both internal and external factors when identifying risks.
2. Failure Mode and Effects Analysis (FMEA)
FMEA is a detailed method for recognizing potential failure modes within a process and evaluating their likelihood and impact. Here’s how it works:
Identify the Process: Define the specific process to analyze.
List Failure Modes: Brainstorm possible failure modes and their repercussions.
Assess Risk: Rate the likelihood, severity, and detection of each failure to prioritize risks.
Implement Actions: Create plans to mitigate high-priority failure modes.
This structured analysis helps organizations understand where failures may occur, enabling them to take preventive actions effectively.
3. Process Mapping
Process mapping involves visually outlining a process to identify possible risk points. By creating a flowchart, organizations can reveal inefficiencies, uncertainties, and areas that may cause quality issues.
*Example: If a company maps its production workflow and identifies a bottleneck at the quality inspection stage, it can take steps to streamline operations and minimize delays.
This clarity enhances communication among team members and strengthens overall risk management.
4. Brainstorming Sessions
Holding brainstorming sessions with employees from diverse departments can lead to rich insights into risk identification. By fostering a space where team members can voice their concerns and ideas, organizations can uncover risks that may have otherwise gone unnoticed.
*Example: A customer service team may highlight a potential risk related to customer complaints that the production team was unaware of, leading to a more comprehensive risk profile.
Documenting these sessions creates valuable insights for future ISO 9001 audits and management reviews.
5. Root Cause Analysis (RCA)
Understanding the root causes of identified risks is essential for effective corrective action. RCA helps organizations trace back the factors contributing to risks, facilitating proactive improvements.
*Example: Using the “5 Whys” technique, a team might discover a recurring quality issue stems from inadequate training for new employees. By addressing this root cause, they can significantly reduce the risk of future problems.
By tackling root causes, organizations strengthen their quality management systems.
Risk Identification Tools in ISO 9001 Implementation
Employing specific tools can enhance risk identification during ISO 9001 implementation. Here are some valuable tools organizations should consider:
6. Risk Matrix
A risk matrix visually displays the likelihood of risks occurring alongside their potential consequences.
Organizations can categorize risks as low, medium, or high based on their assessments, which helps prioritize risk management efforts
This practical tool allows organizations to allocate resources effectively to areas requiring the most attention.
7. Checklists
Risk identification checklists provide a systematic means of evaluating compliance with ISO 9001 requirements.
Teams can use these checklists to ensure that every critical aspect of a process is examined, reducing the chance of overlooking issues
This tool is especially beneficial during internal audits or ISO 9001 certification reviews.
8. Audits and Reviews
Conducting regular internal audits and management reviews is crucial for maintaining ISO 9001 compliance. These processes help organizations identify weaknesses in their quality management systems and recognize potential risks.
*Example: If audit findings indicate frequent nonconformities in customer returns, this insight can guide adjustments to improve product quality.
This ongoing approach not only aids compliance but also promotes a culture of continuous improvement.
9. Data Analysis
Data plays a vital role in identifying risks. By analyzing performance metrics, organizations can identify trends that suggest potential problems.
Metrics such as nonconformities, customer complaints, and corrective actions provide critical insights into areas needing enhancement
Advanced analytics tools can make this process more efficient, allowing for faster identification and response to issues.
10. Stakeholder Feedback
Gathering feedback from customers and other stakeholders can reveal potential risks related to product quality and service delivery. Regular surveys or customer feedback loops can inform organizations about perceptions of their operations.
*Example: If a significant percentage of customers report dissatisfaction with customer service, this critical feedback can indicate a risk area that needs urgent attention.
Integrating stakeholder feedback into risk identification fosters a responsive and robust quality management system.
Fostering a Risk-Aware Culture
Establishing a risk-aware culture within an organization is vital for sustaining ISO 9001 compliance. Here are some strategies to promote such a culture:
1. Training and Development
Invest in training for all employees on risk management principles to improve their ability to identify risks. Make risk identification a regular topic in training sessions.
2. Open Communication
Create an environment where discussing risks is encouraged and stigma-free. Building trust among team members fosters proactive risk identification.
3. Management Commitment
Leadership must actively demonstrate their commitment to risk management practices. Leading by example underscores the importance of quality standards and encourages participation from everyone.
4. Recognition and Rewards
Recognizing and rewarding those who contribute meaningfully to risk management can boost motivation. Celebrating achievements not only empowers employees but also emphasizes the significance of maintaining quality.
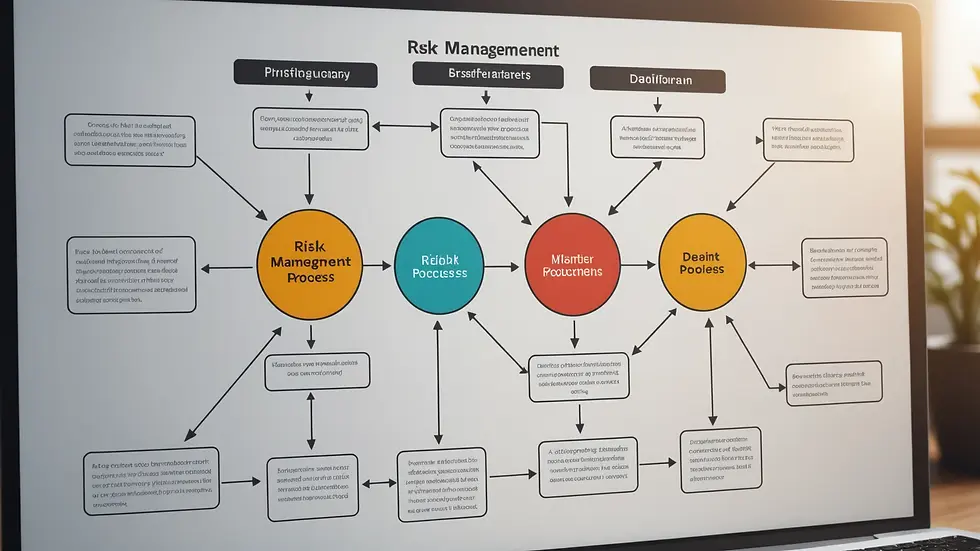
Final Thoughts
Identifying risks is a crucial part of successful ISO 9001 implementation and ongoing quality management. Utilizing practical tools and methods like SWOT analysis, FMEA, and data analysis helps organizations uncover potential issues that might undermine their quality objectives.
Moreover, cultivating a risk-aware culture through targeted training, open communication, and recognition inspires teams to engage in risk management actively. By prioritizing risk identification and mitigation, organizations not only ensure compliance with quality standards but also set the stage for continuous improvement, higher customer satisfaction, and sustainable operational success.
In a landscape where quality and compliance go hand in hand, dedicating time and resources to effective risk management strategies promises significant long-term benefits for any organization striving for ISO 9001 certification.
Comentarios