How to Successfully Navigate the ISO 9001 Certification Process: A Step-by-Step Guide for Quality Management System
- islam Arid
- Dec 7, 2024
- 5 min read
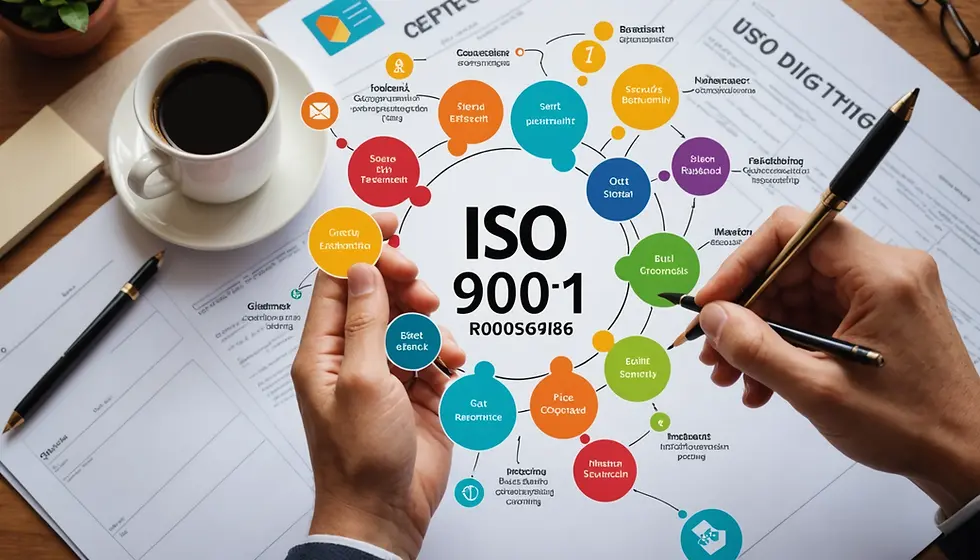
Achieving ISO 9001 certification is a vital goal for organizations aiming to improve their quality management systems. This globally recognized standard helps businesses ensure they consistently meet customer expectations and comply with regulations. In this post, we provide a detailed step-by-step guide to successfully navigate the ISO 9001 certification process, uncovering both the benefits and challenges involved.
Understanding ISO 9001
ISO 9001 is part of the ISO 9000 family of quality management standards. It emphasizes the need for organizations to reliably deliver products and services that meet customer and regulatory expectations. The standard supports continuous improvement and operational efficiency, making it suitable for businesses of all sizes—according to a survey, 80% of companies reported enhanced efficiency after obtaining ISO 9001 certification.
Benefits of ISO 9001 Certification
The benefits of obtaining ISO 9001 certification are clear. It can enhance process efficiency, leading to a remarkable 20% increase in productivity for many organizations. Furthermore, satisfied customers are key to success; companies that achieve ISO 9001 certification often see a 15% boost in customer satisfaction. Additionally, this certification helps businesses forge stronger relationships with customers and stakeholders, enhancing market position and enabling a competitive edge.
Step-by-Step Guide to the ISO 9001 Certification Process
Achieving ISO 9001 certification comprises several critical steps. Below is a breakdown of essential stages in the certification process that contribute to establishing a comprehensive quality management system.
Step 1: Initial Assessment
Before starting the certification process, organizations must assess their current quality management practices. This evaluation identifies gaps between existing practices and ISO 9001 requirements.
Key Actions:
Review Existing Processes: Conduct a thorough examination of current quality management practices and documentation.
Identify Gaps: Compare existing processes against ISO 9001 standards to pinpoint areas needing improvement—working with a consultant can help in this phase.
Engage Stakeholders: Involve team members to gain insights into existing quality practices and gather valuable feedback.
Step 2: Conduct a Gap Analysis
Performing a comprehensive gap analysis is crucial for understanding your organization’s readiness for ISO 9001 certification. This analysis highlights the current state of your quality management system and what is needed for compliance.
Key Actions:
Analyze Operational Procedures: Assess all operational processes against ISO 9001 guidelines; over 70% of organizations find efficiencies by this method.
Develop Action Plan: Create a detailed plan to close gaps, clearly outlining responsibilities and timelines for completion.
Image Placeholder:

Step 3: Develop a Quality Management System (QMS)
After identifying gaps, organizations must either develop a new Quality Management System or refine the existing one to align with ISO 9001 standards. The QMS should encompass all key documentation and processes, including policies, objectives, and major procedures.
Key Actions:
Document Processes: Create procedures and policies that adhere to ISO 9001 requirements, ensuring clarity and accessibility.
Define Objectives: Establish measurable quality objectives that align with the organization’s strategic goals.
Engage Employees: Involve employees from all levels to promote understanding and encourage active participation.
Step 4: Implement the QMS
With a clear management system defined, it is time to implement these processes organization-wide. This stage is vital for instilling a culture of quality.
Key Actions:
Train Staff: Provide comprehensive training sessions for all employees to ensure they understand ISO 9001 principles.
Communicate Changes: Inform all stakeholders about new processes for transparency.
Monitor Implementation: Regularly check adherence to the new practices to ensure consistency.
Step 5: Conduct Internal Audits
Internal audits are essential to verify that the QMS operates effectively and complies with ISO 9001 standards. This review evaluates processes for any deviations from planned activities.
Key Actions:
Develop Audit Schedule: Establish a timetable for regular internal audits covering all areas of the QMS.
Conduct Audits: Execute audits as per the schedule and gather data on compliance and effectiveness.
Document Findings: Record audit results, noting any non-conformities discovered during the process.
Step 6: Address Non-Conformities
If internal audits expose any non-conformities, it’s crucial to address these issues promptly. Closing audits' gaps strengthens the QMS and prepares the organization for the external audit.
Key Actions:
Investigate Non-Conformities: Determine root causes of any issues highlighted during audits.
Develop Corrective Actions: Create plans for rectifying identified non-conformities and implement necessary changes.
Follow Up: Monitor the effectiveness of corrective measures to ensure problem resolution.
Step 7: Management Review
A management review is a crucial step that allows top management to evaluate the QMS's performance. This review ensures the system's effectiveness and alignment with strategic goals.
Key Actions:
Analyze Audit Results: Review internal audit outcomes, customer feedback, and performance metrics to assess effectiveness.
Evaluate Changes: Reflect on any significant organizational changes that might impact the QMS.
Set Future Objectives: Revise QMS strategies and establish new quality objectives, if necessary.
Step 8: External Certification Audit
After completing internal audits and addressing non-conformities, the next important step is the external certification audit conducted by an accredited certification body.
Key Actions:
Choose a Certification Body: Select a reputable certification body with ISO 9001 audit experience.
Prepare for the Audit: Ensure documentation is organized and relevant staff are ready for questions.
Conduct the Audit: Facilitate a thorough evaluation by auditors, welcoming their feedback on ISO 9001 compliance.
Step 9: Certification Decision
Following the external audit, the certification body will determine whether your organization meets ISO 9001 certification standards based on their findings.
Key Actions:
Receive Audit Report: Review the audit report, which includes findings and suggestions for improvement.
Certification Granted: If compliant, your organization will receive ISO 9001 certification.
Address Any Non-Conformities: If minor non-conformities exist, your organization may be allowed time to rectify them before final certification.
Step 10: Continuous Improvement
Certification marks the start of a continuous improvement journey. Organizations should regularly assess and enhance their QMS to stay attuned to customer needs and market shifts.
Key Actions:
Review QMS Performance: Continuously monitor and measure the QMS's progress.
Engage Stakeholders: Collect feedback from employees and customers to spot improvement areas.
Adapt to Change: Stay adaptable and refine the QMS based on feedback and lessons learned.
Challenges and Solutions in the Certification Process
While pursuing ISO 9001 certification is rewarding, organizations may face challenges. Recognizing these hurdles and crafting strategies to overcome them can aid in successful certification.
Resource Allocation
A significant challenge organizations encounter is managing both financial and human resources for the ISO 9001 certification. This struggle can be particularly severe for small businesses.
Objective Strategy:
Develop a Budget Plan: Create a budget that accounts for all certification-related costs, including training and external audits.
Assign Dedicated Team: Form a specialized team to manage and oversee the certification process, alongside setting clear objectives and deadlines.
Employee Buy-In
Securing employee commitment is essential for implementing an ISO 9001-compliant quality management system. Employee resistance can hinder certification if not effectively addressed.
Objective Strategy:
Communicate Benefits: Help employees understand the advantages of ISO 9001 certification, such as improved processes and reduced errors.
Involve Employees: Engage employees in the development and implementation phases to foster ownership.
Managing Documentation
Documentation can be overwhelming during the ISO 9001 certification process. Having comprehensive but manageable documentation is critical for compliance.
Objective Strategy:
Create Clear Templates: Develop templates for documentation to standardize processes and avoid duplication.
Establish Document Control: Implement a robust control system to manage updates and maintain accessible documents.
Charting Your Course Toward Certification
The ISO 9001 certification process offers an essential opportunity for organizations to enhance their quality management systems, paving the way for operational excellence. By following the outlined steps and addressing potential challenges with strategic solutions, businesses can enjoy the numerous benefits that come with ISO 9001 certification.
Investing in a quality management system improves operational efficiency and elevates customer satisfaction, offering organizations a strong competitive advantage in their respective markets. As the business landscape shifts, a commitment to quality and continuous improvement remains vital for sustained success.
Comments