How to Foster a Culture of Innovation and Quality Improvement in ISO 9001 Implementation
- islam Arid
- Apr 30
- 5 min read
Implementing ISO 9001 goes beyond simply meeting regulations. It's a strategic journey toward quality excellence. This standard lays the groundwork for a strong Quality Management System (QMS) that not only meets compliance needs but also propels organizations toward constant improvement. Success requires a culture that promotes innovation while meeting rigorous quality standards.
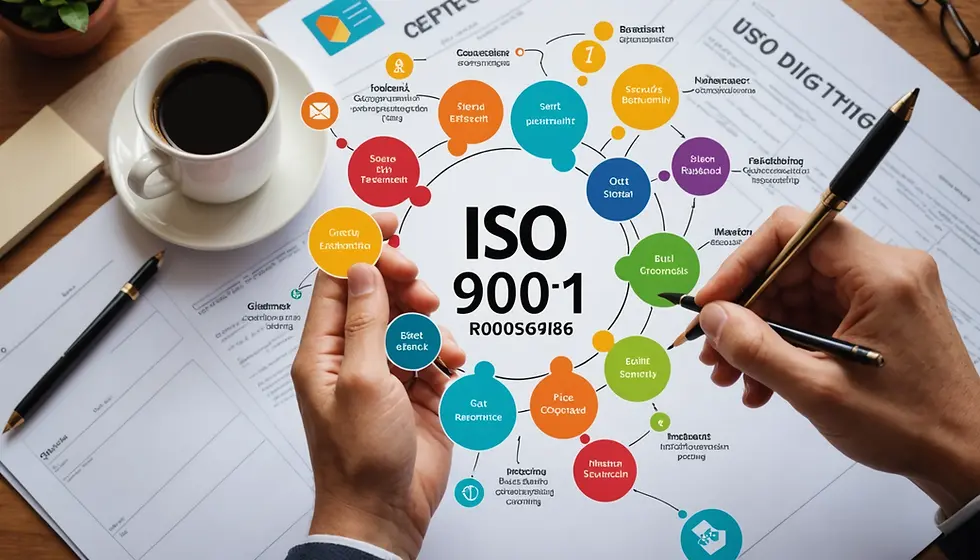
In this blog post, we will explore practical strategies to help organizations create an environment that supports innovation and continuous quality improvement during ISO 9001 implementation.
Understanding ISO 9001 and Its Importance
ISO 9001 is a globally recognized quality management standard. It outlines a framework that organizations can follow to maintain consistent product quality and service delivery. By adopting standardized processes, businesses can meet customer expectations while minimizing risks.
Achieving ISO 9001 certification boosts an organization’s credibility and enhances its competitive edge. For example, a study showed that companies with ISO 9001 certification improve their efficiency by about 20% within the first year. More importantly, the long-term value lies in how organizations integrate ISO principles into their culture, promoting ongoing quality improvement.
Embracing Continuous Improvement: The Cornerstone of Innovation
Continuous improvement is at the heart of ISO 9001. Organizations must recognize that innovation flourishes in a setting that encourages experimentation, learning from setbacks, and refining successful concepts.
Plan-Do-Check-Act (PDCA) Cycle
One effective tool for promoting continuous improvement is the PDCA cycle. This method allows teams to plan and implement changes, check the outcomes, and act on their findings. By following this cycle, organizations can foster innovation while keeping quality front and center. For instance, a manufacturing firm used the PDCA approach to streamline its production process, resulting in a 15% reduction in waste and a significant increase in overall efficiency.
Building a Quality Culture
A commitment to quality begins at the leadership level. Leaders must exemplify a dedication to quality and innovation through their actions and policies.
Quality Policy Development
Creating a clear quality policy that expresses the organization's commitment to quality and innovation is critical. This policy should be communicated throughout the organization, guiding all employees toward shared objectives.
Training and Development
Investing in employee training fosters a deeper understanding of the QMS and inspires ideas for improvement. For example, a hospitality company that provides quarterly training sessions for its staff has reported better guest satisfaction scores and a marked rise in new service offerings.
Engaging Employees: The Frontline Innovators
Employees can be invaluable sources of innovative ideas. They engage directly with processes and can pinpoint improvement areas others might miss.
Empowerment and Ownership
Encouraging employees to take charge of their roles and participate in decision-making can significantly boost innovation and morale. This empowerment leads to teams who are more invested in the quality results of their work. A case in point is a tech company that implemented employee-led innovation teams, which resulted in a surge of new product features based on customer feedback.
Feedback Mechanisms
Implementing feedback systems, like suggestion boxes or regular brainstorming sessions, helps spark innovative thoughts. Actively listening to employees not only creates a sense of inclusion but also uncovers insights that can lead to impactful quality improvements.
Utilizing Performance Metrics for Continuous Improvement
Monitoring performance is key to identifying improvement opportunities. By implementing performance metrics aligned with ISO 9001 standards, organizations can evaluate their effectiveness in quality management and innovation.
Key Performance Indicators (KPIs)
Establish KPIs that track both quality and the performance of innovative initiatives. For example, a logistics company can measure on-time delivery rates and customer satisfaction scores to assess the effectiveness of their quality improvement strategies.
Internal Audits and Management Reviews
Conducting regular internal audits and management reviews provides valuable insights into quality adherence and identifies innovation opportunities. These evaluations clarify areas needing attention and adjustments in QMS processes. A major health service provider reported a 30% increase in compliance scores and quality outputs after adopting rigorous internal reviews.
Integration of Risk Management in Innovation
Risk management plays a critical role in organizations pursuing ISO 9001 certification. Identifying potential risks in innovative processes can help in proactively addressing problems.
Risk Assessment Techniques
Employing risk assessment tools like Failure Mode and Effects Analysis (FMEA) during innovation initiatives can guide decision-making. For instance, a pharmaceutical company can use FMEA to identify potential pitfalls in drug development while still pursuing creative solutions.
Balancing Risk with Flexibility
While risk management is essential, maintaining some flexibility in innovation processes is crucial. Excessive rigidity can stifle creativity and prevent teams from freely exploring new ideas or solutions.
Supplier Quality and Collaboration
Quality improvement is not only an internal concern; it also involves suppliers and partners.
Supplier Audits and Quality Engagement
Conducting thorough supplier audits helps ensure that external partners meet the organization’s quality standards. Engaging suppliers in quality discussions fosters a shared commitment and can lead to more innovative approaches to shared challenges.
Collaborative Platforms
Creating platforms for suppliers to share best practices and innovations enhances the overall quality of products and services. This collective effort can lead to mutual success and elevated quality across the supply chain.
Communicating Success Stories
Sharing successes is vital for sustaining momentum in innovation and quality improvement efforts.
Recognition Programs
Establishing programs that recognize individuals or teams for their innovative contributions to quality can motivate a culture of excellence. An automotive company saw a 25% increase in employee engagement after launching a program that celebrated innovative milestones.
Sharing Best Practices
Developing channels for disseminating success stories within the organization can promote learning. Methods like newsletters, presentations, or team meetings foster an environment where colleagues inspire one another.
Maintaining Organizational Agility
In today’s fast-paced business world, organizations must remain agile to respond effectively to market shifts.
Encouraging Cross-Functional Collaboration
Encouraging teams from different departments to work together can yield diverse insights and solutions. For example, a consumer goods company formed cross-functional teams to address customer feedback, leading to quicker product adjustments and heightened quality ratings.
Continuous Learning and Adaptation
Fostering a culture of continuous learning prepares employees to adapt and innovate consistently. Organizations can offer workshops, training, and resources to promote ongoing development and flexibility.
The Ongoing Journey of Quality and Innovation
Fostering a culture of innovation and quality improvement during ISO 9001 implementation is not a one-time task; it involves continual commitment, engagement, and support. As organizations embrace continuous improvement practices while adhering to quality standards, they can enhance customer satisfaction and reinforce their market standing.
ISO 9001 provides a strong framework for managing quality, but the real change happens when organizations prioritize a culture of quality. By supporting employees, engaging suppliers, and promoting collaboration, businesses can cultivate an agile and innovative environment ready for future challenges.
As your organization embarks on ISO 9001 implementation, remember the journey extends beyond certification. It opens the door to ongoing learning, flexibility, and a tireless pursuit of excellence in quality and innovation.
Opmerkingen