How to Effectively Evaluate Supplier Performance and Manage Supplier Risks in ISO 9001 Compliance
- islam Arid
- Apr 30
- 4 min read
Grabbing Your Attention on Supplier Evaluation
In today’s fast-paced supply chain environment, evaluating supplier performance and managing risks is more critical than ever. With customer demands rising and expectations for quality soaring, businesses cannot afford oversight in their supplier relationships. ISO 9001 offers a structured framework through Clause 8.4, which focuses on evaluating suppliers to ensure quality products and services that enhance customer satisfaction. The stakes are high; it is not just about compliance—it's about driving improvements that can lead to market advantage.
This post will break down effective methods for assessing supplier performance and managing risks within the ISO 9001 framework. You will leave with actionable strategies you can implement right away.
Understanding Clause 8.4 of ISO 9001
Clause 8.4 of ISO 9001 outlines clear requirements for evaluating suppliers. Organizations must establish criteria to assess these external providers, ensuring they deliver high-quality materials or services consistently. This is not just a checkbox exercise. Compliance requires attention to multiple factors, including:
Quality Control: Ensure products meet specifications.
Supplier Capabilities: Evaluate financial stability and risk management.
By prioritizing comprehensive evaluations, companies bolster their quality management systems and ultimately enhance their operational efficiency.
Key Components of Supplier Performance Evaluation
Performance Metrics
Effective supplier evaluation largely depends on selecting the right performance metrics. Consider these critical areas:
Quality: Aim for a defect rate of less than 2% to ensure a high standard.
Delivery: Monitor on-time performance, striving for a target of 95% or higher.
Cost: Analyze total cost of ownership, which should include warranty and maintenance costs, to ensure competitiveness.
Implementing a balanced scorecard can provide clarity by allowing more holistic evaluations across these metrics.
Regular Audits
Conducting supplier audits helps maintain control and confirm that suppliers adhere to ISO 9001 standards. Key audit types include:
On-Site Audits: Visiting supplier operations helps you see processes in action.
Document Reviews: Assess quality records to verify compliance with standards.
Supplier Self-Assessments: Encourage suppliers to evaluate themselves against your criteria.
Regular audits promote open communication and help identify areas for improvement, ensuring continuous compliance.
Feedback Mechanisms
Having structured feedback processes supports ongoing evaluations. Employ methods such as:
Surveys: Regularly distribute surveys to teams interacting with suppliers, gathering insights on performance.
Performance Reviews: Hold quarterly meetings to discuss metrics and potential enhancements.
Escalation Processes: Establish clear protocols for reporting concerns to address issues promptly.
These frameworks ensure suppliers receive feedback that encourages accountability and quality.
Supplier Risk Management Strategies
Identifying Risks
Risk identification is an essential first step in managing supplier health. Consider evaluating:
Financial Stability: Reviewing credit ratings and financial statements to prevent disruption due to insolvency.
Supply Chain Risks: Assessing potential disruptions from natural disasters, geopolitical changes, or logistical challenges.
Compliance Risks: Monitoring suppliers for adherence to environmental regulations and industry standards.
By being proactive in risk identification, companies create stronger action plans to mitigate threats.
Risk Mitigation Plans
After identifying risks, it is essential to develop effective mitigation strategies. Strategies could include:
Contingency Plans: Preparing alternative suppliers ensures smooth operations, targeting less than a week for sourcing changes.
Supplier Development Programs: Invest time in training and resources that enhance your suppliers' capabilities.
Regular Monitoring: Employ real-time dashboards to keep a pulse on supplier risk factors.
With well-defined mitigation strategies, organizations fortify their supply chain against disruptions.
Communication and Collaboration
Active collaboration ensures that both parties manage risks effectively. Strong communication allows organizations to:
Share performance feedback that helps improve quality.
Work together on problem-solving initiatives.
Build trust, essential for an effective risk management strategy.
This transparency promotes a shared commitment to improvement.
Continuous Improvement for Supplier Evaluation
Process Improvement
Continuous improvement is not just an idea—it's a practice that benefits supplier evaluations. Consider:
Conducting Reviews: Set up regular assessment meetings every six months to track performance trends.
Using the PDCA Cycle: Apply the Plan-Do-Check-Act strategy to refine supplier management processes.
Applying Lean Principles: Reducing waste in supplier management can improve both efficiency and performance.
These initiatives create a responsive environment that encourages supplier development.
Training and Development
Investing in supplier growth can yield significant returns. You might consider:
Training Programs: Help suppliers understand your quality standards.
Collaborative Workshops: Host learning sessions that bring suppliers together for shared insights.
Such investments enhance supplier performance and contribute to a strong quality culture.
Final Thoughts on Supplier Evaluation and Risk Management
Evaluating supplier performance and managing risks are essential for companies aiming to comply with ISO 9001. By implementing performance metrics, conducting regular audits, and nurturing communication, organizations can foster solid supplier relationships that align with quality management goals.
A proactive approach to identifying supplier risks not only protects an organization but also supports customer satisfaction and long-term growth. With ISO 9001 as a guide, companies can navigate the complexities of supplier management, ensuring they stay competitive and committed to excellence in their respective industries.
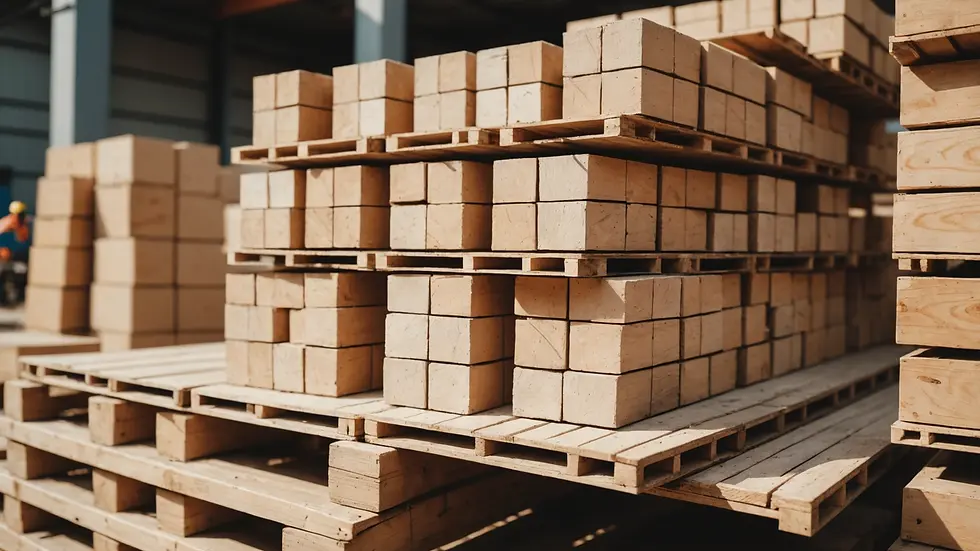
Comments