Ensuring Adequate Resources for ISO 9001 Implementation: Professional Tips for Success
- islam Arid
- May 1
- 5 min read
Implementing ISO 9001 can significantly transform organizations aiming to enhance their quality management systems. This internationally recognized standard can lead to better operational efficiency, improved product quality, and higher customer satisfaction. However, success hinges on effectively allocating resources. In this blog post, you will find valuable insights on managing the necessary resources for ISO 9001 implementation, complete with actionable strategies to optimize these resources.
Understanding ISO 9001 Standards
ISO 9001 sets clear criteria for a quality management system (QMS) and is founded on quality management principles. Key principles include:
Customer Focus: Understanding and meeting customer needs improves satisfaction. For instance, companies that implement ISO 9001 often see a customer satisfaction increase of up to 20%.
Engagement of People: Involving all employees enhances their efforts to support quality.
Process Approach: Focusing on processes can streamline operations and reduce waste.
Continuous Improvement: Organizations can maintain and increase performance through regular improvements.
Adhering to ISO 9001 can increase operational efficiency and foster a culture of consistent growth. To achieve these benefits, adequate resource allocation and planning are crucial.
Identifying the Resources Needed
To ensure successful ISO 9001 implementation, organizations should pinpoint specific resources across several categories:
Human Resources: Experienced personnel are vital for implementing and maintaining ISO 9001. At least 80% of organizations that succeed in their ISO initiatives invest adequately in training and engaging personnel from all levels.
Financial Resources: Sufficient funding is necessary for training, development, consulting services, and quality tools. A survey showed that organizations typically allocate around 5% of their operational budget to quality management initiatives.
Physical Resources: Infrastructure, equipment, and technology must support quality management processes. Investing in the right technology can enhance process efficiency by up to 30%.
Information Resources: Effective documentation practices are essential. Accurate records, such as quality manuals and nonconformity reports, should be maintained.
Time: Organizations should dedicate time for training sessions, internal audits, and process improvements. Setting aside 10-15% of staff working hours for quality-related activities can lead to improved results.
Understanding these resources allows for a strategic approach to implementation.
Developing a Quality Policy
Establishing a quality policy creates a guiding framework for your organization's quality journey. This policy should communicate your commitment to quality while outlining specific quality objectives that align with ISO 9001.
To create an effective quality policy:
Involve Top Management: Educate and engage leaders to ensure the policy reflects the organization’s strategic goals.
Be Concise and Clear: The policy must be straightforward so that all employees can understand it.
Establish Specific Quality Objectives: Use the SMART criteria (Specific, Measurable, Achievable, Relevant, Time-bound) to set clear quality objectives. For example, a company might aim to reduce product defects by 15% within one year.
Once established, communicate this policy throughout the organization to promote a common understanding of quality goals.
Training and Development
Investing in training is essential for ISO 9001 success. Employees should understand their roles in the QMS and comply with ISO standards.
Effective Training Strategies:
Conduct Training Needs Assessments: Identify specific training requirements based on roles. Around 70% of failure to comply with ISO standards can be traced back to inadequate training.
Utilize Diverse Learning Methods: Use workshops, e-learning platforms, and hands-on training to cater to different learning preferences. For example, training that combines videos with interactive sessions can improve retention by up to 60%.
Provide Ongoing Training Opportunities: Establish a culture of continuous learning by offering regular updates and refresher courses. Offering training monthly can significantly enhance employee engagement.
Focusing on training ensures that your workforce is knowledgeable and committed to maintaining quality standards.
Document Control
Effective document control is paramount for managing quality processes and ensuring ISO compliance. Key documents include quality manuals, procedures, and records of nonconformities.
Document Control Considerations:
Establish Clear Procedures: Clearly define the steps for document creation, review, approval, and revisions to ensure consistency.
Utilize Technology: Implement a document management system to streamline control processes. Organizations that automate document control processes can save up to 30 hours per week in manual work.
Ensure Accessibility and Compliance: Make sure relevant personnel can easily access up-to-date documents. An accessible system enhances compliance tracking.
Proper document control supports ISO compliance while boosting operational efficiency.
Internal Audits and Compliance Checks
Internal audits are crucial for assessing the effectiveness of ISO 9001 implementation. They help identify nonconformities and gauge how well quality objectives are being met.
Internal Audit Strategies:
Establish an Audit Schedule: Plan internal audits regularly to monitor compliance continuously. Many organizations find that auditing quarterly leads to better compliance adherence.
Train Internal Auditors: Ensure auditors understand ISO 9001 standards thoroughly. A well-trained auditing team can improve findings accuracy by over 25%.
Act on Audit Findings: Use audit results to create improvement plans. Organizations committed to addressing nonconformities report a 40% decrease in recurring problems.
Regular auditing plays a vital role in maintaining compliance and enhancing the QMS's overall effectiveness.
Managing Nonconformities
Nonconformities can obstruct achieving ISO 9001 certification. Establishing procedures to identify, document, and address them is vital.
Steps to Manage Nonconformities:
Define Nonconformity Procedures: Outline steps for handling nonconformities, including investigation and corrective actions.
Involve Relevant Personnel: Ensure all affected stakeholders are part of discussions for resolution.
Monitor Corrective Actions: Utilize metrics to analyze the effectiveness of actions taken to prevent recurrence. Tracking metrics can help organizations see a 35% improvement in process adherence.
By effectively managing nonconformities, organizations reinforce their commitment to quality improvement.
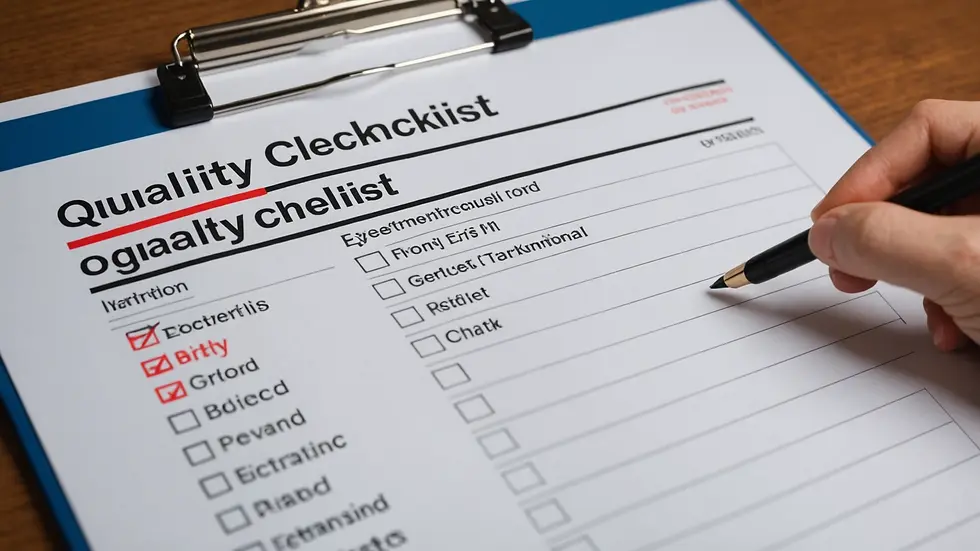
Continuous Improvement and Risk Management
Continuous improvement is fundamental to ISO 9001. Creating a culture that promotes ongoing evaluation and enhancement of processes is essential.
Fostering Continuous Improvement:
Implement Feedback Systems: Set up channels for employees and customers to provide input for improvements. Approximately 60% of companies that solicit feedback see process improvement.
Utilize Performance Metrics: Regularly review metrics to spot trends and areas for enhancement.
Incorporate Lean Techniques: Applying lean management can result in a waste reduction of up to 50% while improving quality.
Identifying potential risks to the QMS and developing mitigation strategies also enhances continuous improvement efforts.
Management Review
Management reviews are essential for evaluating the QMS's performance and alignment with strategic goals.
Elements of Management Review:
Regular Review Meetings: Schedule management reviews to assess the QMS's effectiveness. Organizations conducting reviews biannually often find updated insights to direct quality improvements.
Analyze Key Performance Data: Use performance data to evaluate the QMS and discover improvement opportunities.
Drive Strategic Decisions: Utilize insights from reviews for informed decision-making that supports continuous improvement.
Effective management reviews underpin the commitment to quality and help ensure sustained ISO 9001 compliance.
Cultivating a Quality Culture
Creating a quality culture is vital for successful ISO 9001 implementation. A focus on quality motivates employees to take ownership of processes and strive for improvement.
Strategies for Embedding a Quality Culture:
Lead by Example: Management should actively participate in quality initiatives to demonstrate their commitment.
Recognize Quality Efforts: Acknowledge employees who contribute to quality improvements to boost morale.
Encourage Open Communication: Promote discussions about quality issues and involve employees in solutions to problems.
An established quality culture promotes employee engagement and improves compliance with ISO 9001 standards.
Moving Forward with ISO 9001 Implementation
Effective resource allocation and management are essential for successful ISO 9001 implementation. Organizations must prioritize human resources, financial investments, and process optimization while fostering a community dedicated to continuous improvement.
By applying these strategic tips, organizations can confidently tackle the challenges of ISO 9001 implementation. With a deep understanding of resource needs, commitment from personnel across all levels, and efficient systems in place, the journey towards ISO 9001 certification can become a clear and attainable goal.
Investing in quality management not only ensures ISO compliance but also boosts operational efficiency, enhances customer satisfaction, and supports long-term success for organizations.
Opmerkingen